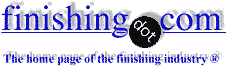
-----
Color fastness for anodized aluminum parts
2007
I am interested in learning more about your capabilities to anodize aluminum parts.
Currently we are producing materials from Aluminum 6061 T6 and 7075-T7 and using Type II anodizing. The parts are machined and then the parts made from T7 are bead blasted using glass beads prior to the anodizing step and sealed with a nickel acetate bath.
After anodizing we have had problems when exposing these parts to methanol
[affil links]- in one instance the color came off within 10 minutes leaving bare metal. On other batches of the same part with the same dye, the anodizing is stable and not affected. We also have a test that uses tetrasodium pyrophosphate (TSPP) and one of the 6061 T6 parts will withstand this alkaline detergent and another part will not and the dye is stripped.
What causes the instability to solvents from batch to batch? Does temperature of the plating bath affect the stability of the anodized part? Is there something that can be done to make the part more resistant to the TSPP? What is the purpose of testing an anodized part with TSPP.
manufacturer of commercial products - Torrance, California, USA
First of three simultaneous responses -- 2007
I would try to find out if the parts were run at the same time.
Typically, what you describe would be a poor seal, with the most likely problem being too low a temperature on one batch (run) of parts. It could be too thin a layer of anodize, but the depth of color of the dye would not be the same.
Talk to you anodizer. He has a problem and should be eager to solve the problem, especially if there is a small possibility that you will take your business elsewhere if he can't solve the problem.
I would start looking for another anodizer just in case this one does not work out so you will have a source available on short notice.
- Navarre, Florida
Second of three simultaneous responses --
It's the seal or lack thereof! Any reputable anodizer providing dyed coatings will always seal his anodize. Not doing so exposes the organic dyestuffs to light, chemical and heat degradation. Sealing the anodic coating, that is exposing the porous anodic cells to either hot water or nickel acetate, will hydrate the outer most layer of aluminum oxide in essence locking in the dye. Without a seal, or using a poor seal, will result in just what you're seeing! A simple "seal integrity" test is detailed in ASTM B136 and will quickly tell you if you have a sealed anodic film or not. If you're anodizer tells you he didn't do it because you didn't ask for it, find a new anodizer!
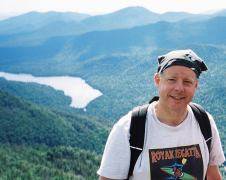
Milt Stevenson, Jr.
Syracuse, New York
2007
Third of three simultaneous responses --
In the case of methanol your parts are not properly sealed. Job shops are notoriously negligent in maintaining seal quality. In the case of the TSPP, some of your parts are sealed better than others, but ANY alkali will gradually degrade (dissolve hydrated aluminum oxide) sealed anodized aluminum. - including regular machine dishwashing detergent.
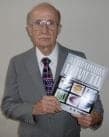
Robert H Probert
Robert H Probert Technical Services

Garner, North Carolina
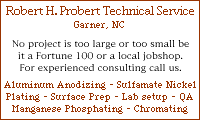
2007
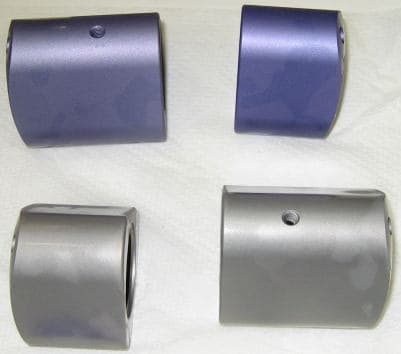
This is the picture of the part before and after soaking in methanol for 10 minutes.
The blue anodize color is not stable.
Q, A, or Comment on THIS thread -or- Start a NEW Thread