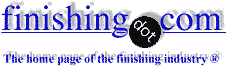
-----
Want to remove mineral oil from steel
2007
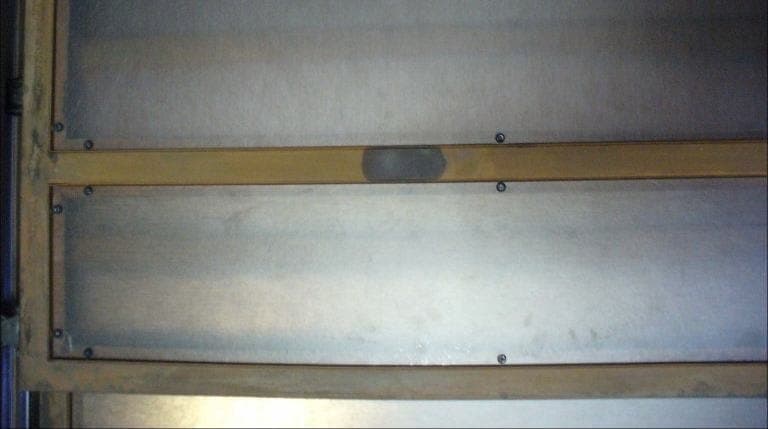
Q. I am a consumer. I recently had three steel framed sliding doors installed in my apartment. The frames are a "T-cross" of 1 1/2" steel tubing with a resin material filling the gaps. Due to a workmanship problem, the original matte finish on the steel had to be sandblasted. I then had them apply a black oxidizer for a weathered look. Because of the sandblasting, the steel became very porous and the steel turned more rusty orange than black -- which looks even better as it turns out.
Here's my problem. I had been advised to apply mineral oil over the metal to condition the steel and prevent any possible corrosive rust. I was under the impression it would sink in, dry and return to its rusty orange color. Not the case. It now looks dark brown and shows no signs of fading after a week. I only did a small section but it's very visible. I assume that the sandblasting is the culprit. Is there ANYTHING I can do to recover the look I want? Or do I need to bite the bullet and cover the rest of the door with mineral oil for a uniform brown look?
Consumer - New York, New York
A. It's not clear what you want, but mineral oil seems to be a problem rather than a solution. Remove it with warm detergent solution. For a more uniform appearance, have the entire steel frame sanded or sandblasted. Perhaps then apply a colored lacquer rather than intentionally causing rust; frame rust appears to be affecting adjacent sheet metal. Always test coatings in inconspicuous locations.
Ken Vlach [deceased]- Goleta, California

Rest in peace, Ken. Thank you for your hard work which the finishing world, and we at finishing.com, continue to benefit from.
2007
Removal of mineral oil before electroplating
November 29, 2017Q. We are having trouble cleaning parts machined with mineral oil.
We will obtain 120+ hours salt fog test on test plates hand washed before testing, and parts machined with emulsion based cutting fluids, but on this paraffin-based mineral oil (Unocut Neat Ax 12) we can at most achieve 24 hours salt fog test.
We are using alkaline zinc with trivalent colored passivate as per ASTM B633 type VI.
Our chemical pre treatment setup is based on alkali clean.
Hot alkali soak 5 min, 60 °C, Cons 30-70 ml/l, Potassium hydroxide
Hydrochloric acid dip 5 min, cons 15%l
El-alkali soak 5 min 80-120 ml/l cons 60 °C, Sodium hydroxide
After almost a year of testing we see that the pre-treatment will not remove the mineral oil: we have tried pre washing the parts with both alkali and acid based soap in a parts cleaner with ultrasonic but only achieving 36 hours in the salt fog tester.
The only thing that has managed to remove this mineral oil is either soaking in alcohol overnight or soaking in thinner.
Earlier we used to have a Trichlorine cleaner, but due to safety regulation we are not allowed to use this.
- Gjovik, Norway
A. Hi Robert. Perhaps the problem can be brought to Texaco's attention for either a suggestion of a cleaning regimen or substitution of a more-easily removed oil.
I would suggest at least trialing the raising of the temperature of your electrocleaner to closer to the boiling point, as this is usually very effective in improving the cleaning action. If the components are not very hard steel, you might also try reversing the direction of the current on the electroclean tank.
Regards,
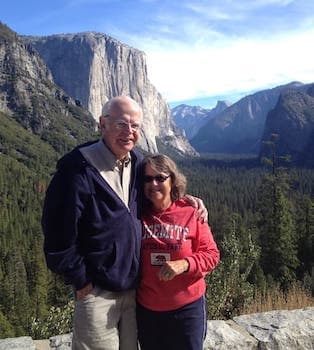
Ted Mooney, P.E. RET
Striving to live Aloha
finishing.com - Pine Beach, New Jersey
December 2017
A. Commercial alkaline cleaners contain (typically) not only a variety of alkalies but surfactants (to emulsify the oils) and dispersants to keep the dirt and organic matter suspended so they can be rinsed off. Plain sodium or potassium hydroxide will not perform anywhere near as well. (Although to a small extent strong alkalies will saponify some organic materials, forming soaps.) Some alkaline cleaners have chelators or complexing agents that also enhance their performance.
And you didn't ask, but I will also give my opinion on pickles. Uncompounded mineral acids won't come close to acids with proprietary additives that inhibit the attack of the acid on the substrate (saving acid) and allow better rinsing.
You might think that you are saving money by not buying proprietary products.
But you're not.
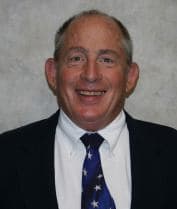
Tom Rochester
CTO - Jackson, Michigan, USA
Plating Systems & Technologies, Inc.

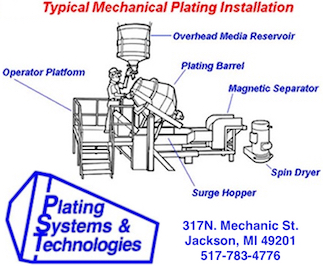
December 4, 2017
Thanks Tom, you're right of course. I probably wasn't paying close enough attention and assumed Robert was talking about alkali-based cleaners and HCl-based pickle rather than straight commodity chemicals. As William Wittke taught us many decades ago, a proper alkaline cleaner must "saponify, wet and emulsify, deflocculate, chelate or sequester, buffer, and inhibit." Few home-brews will do that.
Regards,
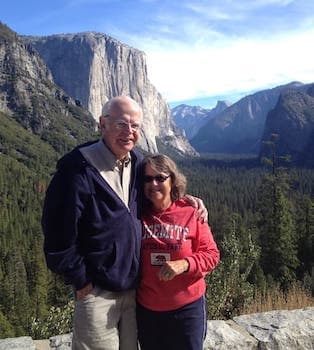
Ted Mooney, P.E. RET
Striving to live Aloha
finishing.com - Pine Beach, New Jersey
December 2017
December 6, 2017
Q. To clarify:
We are using commercial alkali cleaners with emulsifying agents for both electro clean & soak clean.
We have also tried a commercial soak cleaner with 25-50% sodium carbonate
⇦ on
eBay or
Amazon]
+ 20-25% sodium hydroxide, before "normal" soak clean and electro clean.
We have tried washing the parts first with a water based industrial parts washer, with both alkaline and acidic soap recommended by the parts washer. The parts washer is used by our NDE department, so we even have no visible oil on surface when using UV fluorescence test on washed parts.
Despite all this we have not been able to get clean parts.
Our chemical supplier has no more suggestion for the removal of the oil.
The cutting oil supplier has suggested a solvent based washer based on Perchloroethylene or 3-butoxypropan-2-ol.
- Gjovik, Norway
A. Robert,
I don't know size of your parts and your special requirements or process restrictions, but I would propose to try on small test piece the following cleaning sequence:
1. Soak in heated Lemonene (~35-50 °C) for 20-30 min
2. Soak inacetone
⇦ on
eBay
or
Amazon
[affil links] Warning! Flammable!
(room temp) 10-30 min
3. Soak in Isopropyl Alcohol (2-propanol 70% in water), room temp, 10-30 min
After that, do your regular alkaline cleaning, electrocleaning etching, etc.
- Winnipeg, Canada
December 6, 2017
December 8, 2017
A. Hi Robert
I must disagree with Leon.
Soaking in any solvent means that the part is removed from a solution of oil.The solvent evaporates and a film of oil remains.
Acetone is a great solvent for many oils but will do nothing that the Limoline has not already achieved. It is highly flammable and evaporates rapidly exacerbating both problems.
Isopropanol is a polar solvent, flammable (with a near invisible flame) and a poor solvent for oils.
Using three different solvents is pointless. The only possible advantage is that each is slightly less contaminated than the previous - until the oil builds up and the entire line stops working.
Your supplier is correct in advising one of the modern substitutes for TCE but you need to use it in a vapour degreaser or you are back to the re-depositing problem again.
There are alkaline cleaners and even bacterial cleaners but both depend on proper process control. High pressure water jetting can be partially effective but much depends on the shape and quantity of your parts.
You should speak to your zinc process supplier. Your problem is typical of the difficulties encountered by companies moving away from cyanide based zinc processes which are much more forgiving.
I would pursue the search for a more readily removable cutting oil and try to minimise its use.
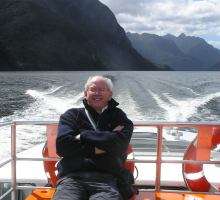
Geoff Smith
Hampshire, England
Q, A, or Comment on THIS thread -or- Start a NEW Thread