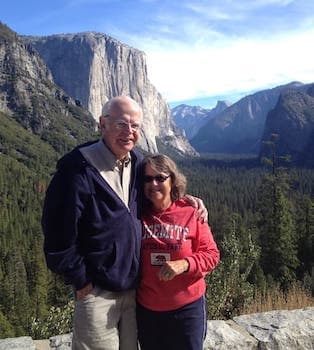
Curated with aloha by
Ted Mooney, P.E. RET
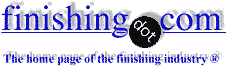
The authoritative public forum
for Metal Finishing 1989-2025
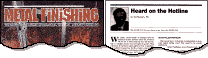
-----
CAN 6061-T6 BE REPLACED WITH 6082-T6 CONSIDERING WEAR RESISTANCE
2007
Dear Friends ,
I'm a product design engineer working in a Rubber products Mfging. company located at UAE
The materials specified are extrusion grade Aluminium . Inserts made of 6061 T6 are to be used in one of our rubber products which are exposed to wear.
I would like to know ,
1)among the elements ( Cr,Cu,Fe, Mg, Mn..) which is the key element that enhances wear resistance of aluminium.
and
2)CAN 6061-T6 BE REPLACED WITH 6082-T6 CONSIDERING WEAR RESISTANCE.
Please advice me on this regard.
Thanking you
Shankar
rubber factory - Sharjah, UAE
2007
The 6xxx aluminum alloys are strengthened (hardened) by precipitation of Mg2Si and also, in some newer alloys, by Cu-containing intermetallics. Cr & Mn are primarily grain refiners. Typical hardnesses (Brinell & Vickers) & strengths of some 6xxx alloys are given below, by increasing tensile yield strength (YS). Data are from www.matweb.com. 6082-T6 is similar to
6061-T6; some sources show 6082 as 5% stronger than 6061, with YS 290 MPa.
6082-T6 Brinell n/a, Vickers 95 YS: 260 MPa, 37700 psi
6061-T6 Brinell 95, Vickers 107 YS: 276 MPa, 40000 psi
6351-T6 Brinell 95, Vickers 107 YS: 283 MPa, 41000 psi
6151-T6 Brinell 100,Vickers 112 YS: 295 MPa, 42800 psi
6009-T6 Brinell 91, Vickers 102 YS: 320 MPa, 46400 psi
6070-T6 Brinell 120,Vickers 137 YS: 352 MPa, 51000 psi
6066-T6 Brinell 120,Vickers 137 YS: 359 MPa, 52000 psi
6013-T651 n/a, Vickers 149 YS: 359 MPa(min), 52100 psi(min)
6033 T6 Brinell 120, n/a YS: 393 MPa, 57000 psi
6069-T6 n/a, n/a YS: 441 MPa, 64000 psi
If compatible with the application, consider hard anodizing or electroless nickel plating the aluminum.
- Goleta, California

Rest in peace, Ken. Thank you for your hard work which the finishing world, and we at finishing.com, continue to benefit from.
In my opinion both 6061 and 6082, and just about any other wrought aluminum alloy you want to name (except maybe deltalloy, 4082) are wretched in wear resistance. The cast alloys that have significant silicon contents are reasonably wear resistant, but the wrought alloys really, really need a hard anodize coating if you are planning on abrading it with anything harder than feathers.

Lee Gearhart
metallurgist - E. Aurora, New York
2007
Dear Shankar.S Have you considered using a PEO coating on your aluminium inserts? The Keronite PEO process produces a surface conversion which can produce hardnesses of up to 2000 vph using aluminium alloys 6000,2000,7000 series.
The process converts the aluminium surface to a hard durable wear resistant ceramic oxide material.
- Cambridge, UK
2007
Hi. I'm perhaps not understanding the situation correctly, but I find it hard to believe that aluminum is a good material for inserts to improve wear resistance regardless of what you coat it with ... because we are talking about wear, and what do you have when the very thin coating wears away?
Regards,
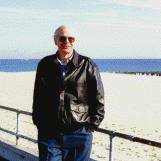
Ted Mooney, P.E.
Striving to live Aloha
finishing.com - Pine Beach, New Jersey
October 2013
Q, A, or Comment on THIS thread -or- Start a NEW Thread