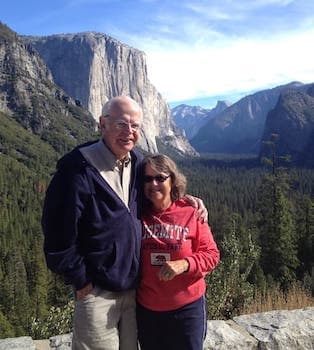
Curated with aloha by
Ted Mooney, P.E. RET
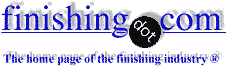
The authoritative public forum
for Metal Finishing 1989-2025
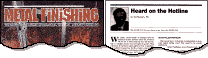
-----
Unexplainable Pitting of 6061 Aluminum Parts
2007
Hello, I am a metallurgical engineer working at an aerospace company and we have been recently having pitting problems with several of our aluminum parts. The problem started on one of our dip brazed aluminum (6061) domes. After being deoxidized, the parts were exhibiting pitting along the bottom area of the dome as well as inside the dome. We analyzed the pits and found the pits to have sulfur, chlorine, oxygen, and sometimes nickel present. We initially attributed the problem to improper cleaning and a contaminated salt bath until we had other parts, that are not dip brazed (they are welded), show similar pitting. The only thing all the parts have in common are that they are 6061 aluminum and are anodized. We have tracked the process several times, but each time, that particular lot shows no pitting. We are running out of ideas here and any thoughts or suggestions would be much appreciated. Included are some pictures of the pitted parts.
Metallurgical Engineer (Aerospace) - Windsor Locks, Connecticut, USA
It is because of welding or braze process. I am sure areas far from welding no pit.
More mechanical polish needed.
- Singapore
2007
You say you first see the pits after the deox. Then tell us what is the deox. Any chlorides present? Are your racked on titanium and the deox is in stainless steel - then the galvanic action in the presence of chloride will start pitting any aluminum alloy. Come back with more data.
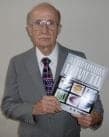
Robert H Probert
Robert H Probert Technical Services

Garner, North Carolina
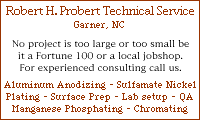
2007
2007
HELLO,
You are looking at the grain structure at the heat affected zone of the weld. The larger the grains the lower the chemical resistance to corrosion. The wrought alloy will have very high resistance ( in relation to ) compaired to the new grain boundries at the heat effected zone. I believe your vendor is burning the part in the anodization. When someone is watching the tank, better care is taken and your samples are excellent. When production is running, the parts sit in the bath and are etched deeply by any chemical that would attack the aluminum. You will have to adjust the process so the anodization is for the new grain size ( part will need less time in bath ) than of a typical wrought product. If the grain size is too big...you may also have a strength issue around the weld.
Just a thought.
- LAKE IN THE HILLS, Illinois, USA
Q, A, or Comment on THIS thread -or- Start a NEW Thread