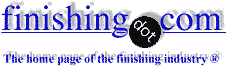
-----
Hot-dip galvanizing plant - relatively small scale
2007
Q. Hello,
My name is Carlos, I am from Argentina,
Currently I see a market opportunity in my area for hot dip galvanizing plant.
I'd like to start something in a relatively small scale (small parts up to a meter of diameter or so). Needless to say that budget is limited.
Since I am a mechanical engineer and electrical technician I'm willing to do as much as possible in house. Otherwise project is not viable.
What I am looking for is a good book that covers furnace design, or at least basic criteria, materials to be used, etc. Good books about HDG suggestions are very welcome too.
Thanks in advance,
- Rosario, SF, Argentina
by NACE
[only rarely available]
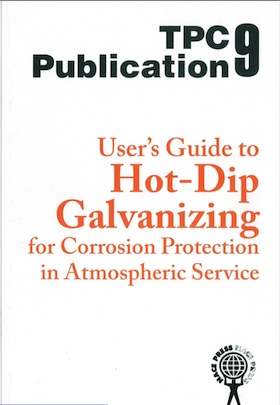
on eBay or Amazon
or AbeBooks
(affil link)
A. Well I think you have to refer for standard online which will supports you a lot, just like I have with chromating.
TARIQ SUNNICITY SIGN - Manama
2007
A. I would look into local Galvanizing associations I know there is one in Mexico I am not sure of South America. I would web-search galvanizing furnace and try a few vendors by email or phone calls.
Good luck,Joe
- Pittsburgh, Pennsylvania, USA
2007
A. Sir:
From interlibrary loan at a large library you can get a xerox copy of my article on kettle furnace design in the journal
Metal Finishing.
Kettles are heated on the sides, but never on the bottom or 9 to 12 inches from the bottom and never from 6 inches down from the top. The side walls heating area is heated not more than 10,000 btu's/sq.ft/hour and as evenly as possible. End firing with high velocity burners is the most efficient with about 67% of the burner heat going through the kettle walls. Looking from above the hot exhaust gases circle in the furnace around the kettle until exiting near the bottom of the furnace. Properly designed and operated a kettle should have a lifetime of 10 or more years. Heat can be captured from the exhaust kettle furnace gases to heat process tanks (e.g. caustic, H2SO4, or flux solution). Constructing a kettle and furnace are NOT do-it-yourself projects. Too small of a kettle is normally not cost effective unless you have a specialty like spin or a location far from other galvanizers.
Regards,
Galvanizing Consultant - Hot Springs, South Dakota, USA
2007
Q. As I learned from earlier answers we must heat the furnace from sides between from bottom 12" & below 6" from up. so my questions are;
1) the firing side wall will not be over heated ?
2) if only one burner will it give a uniform heat to the whole kettle?
3) the exhaust will start from bottom of the furnace?
Please provide a rough drawing if possible. We are planning to install a new diesel burner on our existing electric furnace 1000 x 500 x 500 size kettle
wire galvanizing - kuwait city; kuwait
September 12, 2010

Q, A, or Comment on THIS thread -or- Start a NEW Thread