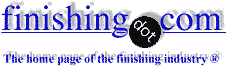
-----
Do I need to use Hard Chrome over E-Nickel when plating D2 Tool Steel?
2007
I am trying to determine the best (and correct!) plating specification for a tooling application that requires corrosion resistance, hardness and wear resistance - in equal measures, of course! I've been researching and talking with several plating vendors and frankly I'm more confused than when I started. Below is the situation:
- Base material is D2 Tool Steel at 60-62Rc
- Used in a rotary tool application against an anvil roll
- Both rolls ~200mm diameter. One is a "die" roll with a cross-hatch pattern cut in to impart a pattern to the materials rolling through the nip (~25,000psi)
- Tooling is subject to chloride atmosphere
- Materials must be FDA approved
- plating needs to be occasionally stripped for re-grind/re-plating
I have spoken with multiple resources and researched this site as well. But I'm no metallurgist or plating specialist....I've gotten some conflicting info from two vendors that both seem quite reputable/knowledgable, so I'd like to do a cross check... The reasonable recommendation appears to be as follows (in terms of ASTM B733 specs....new to me):
- Pre-heat-treat to stress relieve the D2 prior to plating
- Use Electroless Nickel, 25 micron (.001") "Service Condition SC3";
Hi-phosphorous content (10+%) "Type 5"
- Post Heat Treat "Class 3" - 180-200C for 2-4 hours for Hydrogen Embrittlement Relief
That all sounded pretty good, but one vendor suggested that mid-Phos should suffice (Type 4 5-9%), while another vendor said that Hi-Phos is a must, but that the post heat-treat would drastically reduce the corrosion resistance of the EN. If it's bad for Hi-Phos, I assume it's worse for mid-phos(?). Further, he stated that the Hi-Phos EN goes on at <50Rc while, therefore he recommended a chrome finish over the EN. From what I've read, Chrome has inherent cracking through to the substrate, so there's no real corrosion resistance value there.
So that's the basics. What I'd like to know is:
1) With respect to the hardened tool steel and need for post heat-treat, does the mid-Phos EN stand a chance at all?
2) If Hi-Phos is a must (and the post heat treat), can anyone estimate the relative loss of corrosion resistance?
3) Recommendations to maintain the corrosion resistance after post heat treat step?"
4) Finally, I've been told that stripping the old plating prior to re-plate becomes much more challenging (takes more time/attention). Since only part of the surface actually needs to be stripped, is there a method to protect the areas I'd like to 'save' to reduce re-work?
Thanks in Advance
Engineering - Cincinnati, Ohio, USA
First of two simultaneous responses --
Here's an idea. If you could change your roll design to a softer steel (i.e. SAE 4340 heat treated to not more that 35Rc) and have it coated with tungsten carbide+nickel in a modern HVOF equipment you would forget about stripping, regrinds, corrosion, wear, etc. Apparent hardness goes up to 68-70 Rc, corrosion resistance is very good and porosity approaches zero for coatings over 0.010" thick. A better but more expensive option would be a solid tungsten carbide roll. One drawback: to shape that stuff requires diamond tools. One doubt: if it is FDA approved. Further comments appreciated.
Guillermo MarrufoMonterrey, NL, Mexico
2007
Second of two simultaneous responses -- 2007
I like the high P idea and the post heat treat will lower the corrosion protection, but not that bad.
For a better shot at it but at a higher cost, go to boron reduced EN. Harder and more corrosion resistant. Not many shops do it.
You would be well off to run a few beta test parts to see what you can get by with.
I did not remember D-2 as having bad corrosion resistance, at least when compared to A-2 or 4340.
- Navarre, Florida

Q, A, or Comment on THIS thread -or- Start a NEW Thread