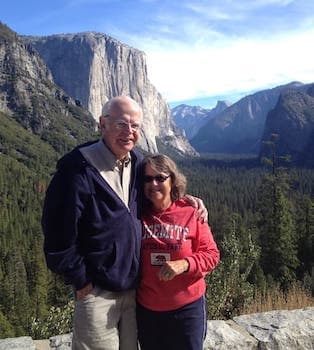
Curated with aloha by
Ted Mooney, P.E. RET
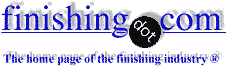
The authoritative public forum
for Metal Finishing 1989-2025
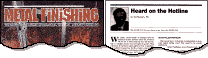
-----
Silver Plating is Blistering
Q. Simple yes / no question. Can anyone barrel plate per AMS2411 and pass the heat/blister test?
I really want to understand if AMS2411 is fundamentally broken without a bake after plate.
- East Hartford Connecticut
June 9, 2022
Q. Good day fellas,
Our customer is reporting nuts with coating peeling. The nuts have bright silver electroplate process done as per AMS2411. This nut is installed on our finish good and sent to customer. The customer takes our good finish and put it into an oven at 800 °F for one hour. After this process, blisters shows up on the nuts. Our supplier of the nuts performs the diffusion bake at 1000 °F for two hours and this does not show any blister.
All the best, aloha. Carlos A. Martinez
Quality Engineer - Reynosa/ Mexico
October 28, 2022
Q. What is the base metal (the nuts), how thick is the silver, is there a brightener, what is the purity of the silver plating solution?
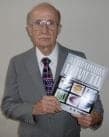
Robert H Probert
Robert H Probert Technical Services

Garner, North Carolina
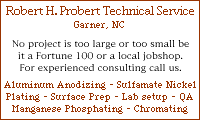
A. Hi Carlos. Is the diffusion baking done in a controlled atmosphere (vacuum, inert gas, or in bags) and the customer baking done in the open air?
Luck & Regards,
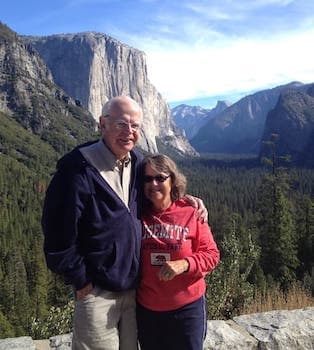
Ted Mooney, P.E. RET
Striving to live Aloha
finishing.com - Pine Beach, New Jersey
⇩ Related postings, oldest first ⇩
by T.V. Harper
(classic reprint of an old book)
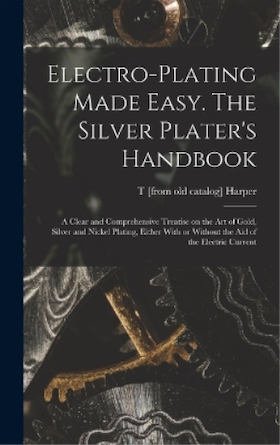
on AbeBooks
or eBay
or Amazon
(affil links)
Q. We are plating Silver .002 to .004 inches thick over nickel strike. Nothing out of the ordinary. After 10,000 hours at 400 °F, the silver plating shows blistering. I know this is not unexpected after such a test, but my question is: What is the mechanism that causes the silver to blister? It seems that in order to form a blister the silver must have been stretched and plastically deformed by some force. What is the is the source of this force? A colleague has suggested differential thermal expansion of the silver after the plating bond is broken. Is this plausible?
Kenneth W. Cornett- North Haven, Connecticut, USA
2007
![]() |
A. Blistering is normally a result of improper cleaning or the strike. It can also result from the brightener component in the silver breaking down and volatilizing. There is an outside chance that you are baking out hydrogen from hydrogen embrittlement, but I would have thought that it would have shown up a lot sooner. - Navarre, Florida A. Some silver brighteners are antimony, some are selenium; both cause a stressed deposit that cannot take high heat. ![]() Robert H Probert Robert H Probert Technical Services ![]() Garner, North Carolina ![]() A. Where does one start? Your colleague could be on to something, but there are a zillion other possibilities. If your bake cycle is indeed 10,000 hours (=400 days!), all sorts of diffusion can occur - is your substrate copper? If it is some sort of brass, bronze or such, my guess is insufficient nickel to prevent copper-silver diffusion which in the right proportion form a brittle intermetallic and upon cooling -- lead to you guessed it. What does the interface between the blister and part look like - both surfaces might give all a hint! ![]() Milt Stevenson, Jr. Syracuse, New York A. What is the atmosphere? If it is air, then: - New Jersey A. More details (substrate, process details, exposure atmosphere) may be necessary to get a response from the silver platers. Analysis of the Ni surface under the blister would help, preferably with the blister broken open inside an SEM. Analyze the gas within a blister if possible. - Goleta, California ![]() Rest in peace, Ken. Thank you for your hard work which the finishing world, and we at finishing.com, continue to benefit from. |
2007
Q. A little more info:
- Substrate is Inconel 718, a nickel-based superalloy not normally susceptible to hydrogen embrittlement
- Plating procedure is a) clean in ultrasonic tank with mild detergent, b) rinse with deionized water, c) alkaline clean 3-5 minutes (MacDermid Process 235L, Concentration 16-18 oz./gal), d) rinse with deionized water, e) acid activator (30-40% HCl), f) nickel strike (Nickel Metal 8-9 oz/gal, HCl 10-12.5%, g) rinse with deionized water, h)silver strike (Silver Metal 0.5 - 0.7 TR. oz/gal, Free Potassium Cyanide 8-12 oz/gal), i) silver plate (Silver Metal 3.0 - 5.0. oz/gal, Free Potassium Cyanide: 8-13 oz/gal)
- The silver plating tanks have Sel-rex Silver Industrial Brightener added at 4 ml / gal (nice unit mix, huh?)
- Silver anodes are certified 99.99% pure. Silver plate purity is 99.9% min (tested monthly).
- I peeled off some of the silver around one of the blisters. The nickel layer underneath was clearly oxidized (very dark grey in color)
- I don't think out-gassing is the culprit. I just can't see where the gas would be coming from. The parts were examined every 1000 hours. No blisters were seen until the 6000 hour mark. If caused by out-gassing, wouldn't this have occurred much sooner?
- Identical seals (processed at the same time and in the same tanks) showed no blisters after 10,000 hours at 150 °C.
- Identical seals (processed at the same time and in the same tanks) but with gold strike before the silver strike show no blisters after 12,000 hours at 250 °C.
- All tests were conducted in standard atmosphere
- North Haven, CT,USA
Q. I am having a problem getting silver to not blister in a 900 degree bake. Material is ASTM A276 [stainless steel]. We have tried all kinds of activations. Hydrochloric acid, reverse sulfuric, Actane 340, Powered direct HCl, Combined with a range of strikes. Woods nickel, sulfamate nickel, copper. Every time parts completely blister after 900 deg bake. At a loss.
Ian M [surname deleted for privacy by Editor]plater - Westfield, Massachusetts, USA
January 18, 2012
by Jack Dini
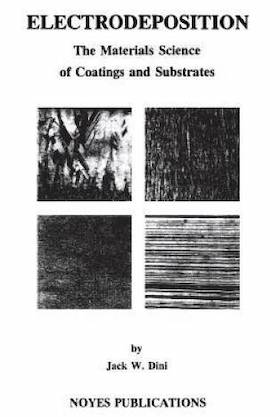
on eBay or
AbeBooks
or Amazon
(affil links)
A. Hi, Ian.
I hate to respond with something as general as "read this book", Ian, but anybody who is having trouble with adhesion on stainless steel and hasn't yet seen Jack Dini's "Electrodeposition - The Materials Science of Coating and Substrates" might be overlooking a vital tool. Jack tested many different plating conditions, and offers actual adhesion values in his "Adhesion" chapter.
Regards,
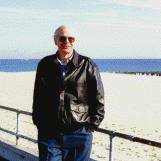
Ted Mooney, P.E.
Striving to live Aloha
finishing.com - Pine Beach, New Jersey
Silver Plated Copper Blisters when Brazed
Q. Hi everyone!
We have a brazing process of terminals. They are made out of copper (substrate) and have a silver plating, which is made by a 3rd party. The silver plating has to conform to ASTM B700.
These pieces are brazed to an electrical motor, but we are having two specific problems:
1) Little blisters (bubbles) after brazing.
2) After brazing, the silver plating comes off in some other pieces.
Our client is rejecting all the pieces with these problems and it's causing serious problems for us.
Do you have any ideas on how to fix this?
- El Paso, Texas
February 9, 2018
Blistering of silver electroplated parts after high temp. bake (760 °C)
Q. Hello my dear friends,
I am working in company which is producing fasteners. I am responsible for special processes department (Heat treatment, Plating, NDT).
My problem is that we are trying to plate some parts with silver electroplating. Specification AMS2411 wants us to make adhesion test at 760 °C for minimum 2 hours. All the time I see blisters all around the parts.
My process is as below (we are doing barrel plating):
1) Alkaline cleaning
2) Sandblast
3) Alkaline cleaning
4) Stress relief
5) Surface activation
6) Nickel plating
7) De-passivation
8) Pre-Silver Plating
9) Silver Plating
10) Hydrogen embrittlement treatment (190 °C, 23 hours)
When I examine the parts by using microscope, there is a gap between nickel and silver. My opinion is that problem is about somewhere between nickel and final silver plating. From my experience most critical parameter about adhesion is cleaning of the surface. I changed all of the rinse bath water. But problem is still there. The funny thing is when I did the same test at 650 °C for different raw-materials, I didn't see any blisters on the parts. This is the all information that I remember. If you need additional information to help me, just let me know. Thanks in advance for all.
- Izmir, Turkey
October 5, 2018
? Hi Baris.
That is indeed a very high temperature and I would suspect that you are right about the issue being between nickel plating and silver plating. Is this sulfamate nickel plating?
Regards,
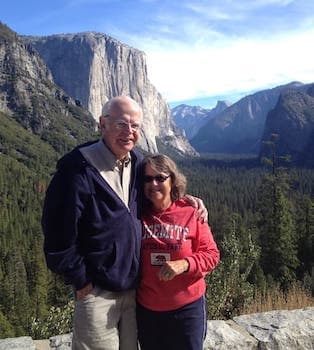
Ted Mooney, P.E. RET
Striving to live Aloha
finishing.com - Pine Beach, New Jersey
Q. Yes Mr. Mooney our nickel bath contains nickel sulphamate and also nickel chloride and boric acid. But the funny thing is I am not still sure that are these bubbles really blisters ? Because when I scratch it with something sharp like a needle, it doesn't flake.
Baris Irmak [returning]- Izmir, Turkey
December 4, 2018
A. Hi Baris. Those are indeed interesting "blisters", being very small, and with many on the bolt head exhibiting a "deflated" look, like a mylar helium balloon that got too old :-)
You might see if you can pull any off with strong adhesive tape to study their backside. Your issue is not within my experience set, and again that temperature strikes me as very hot, and perhaps this looks more like melted silver than blistered silver? Hopefully a reader with more experience in this will comment.
Regards,
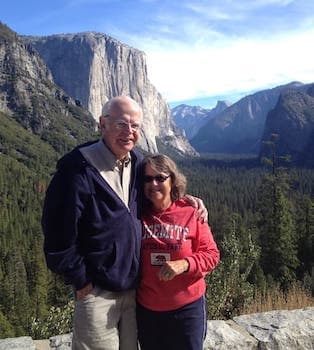
Ted Mooney, P.E. RET
Striving to live Aloha
finishing.com - Pine Beach, New Jersey
A. Come back and let us know: (1) What do you mean, in detail, about "depassivation" -- is it a "strike", what kind of anodes, has the metal concentration increased? (2) Do you have metallic brightener in the silver solution, like antimony or selenium?
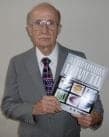
Robert H Probert
Robert H Probert Technical Services

Garner, North Carolina
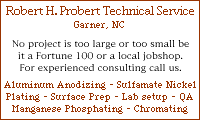
Q. Actually de-passivation bath is used to prepare suitable surface for pre-silver plating bath. It is used to clean surface from nickel oxide. Bath include potassium cyanide and potassium carbonate. We use stainless steel anodes for de-passivation bath.
No we don't have any brightener in our silver bath. Actually we had it (antimony based brightener) but we didn't add brightener in more than 1 year.
- Izmir, Turkey
December 11, 2018
A. Assume you use the cyanide activator with the work cathodic. That kind of activator will not always remove tenacious nickel oxide so you might want to use a strong "Woods" strike (one pound per gallon nickel chloride and one quart per gallon Hydrochloric acid), rolled depolarized nickel anodes, bagged, not s-rounds, and take the anodes out when not in use to prevent the metal content from climbing.
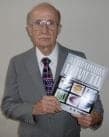
Robert H Probert
Robert H Probert Technical Services

Garner, North Carolina
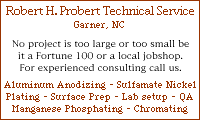
Interpreting AMS2411 Requirements
Q. Silver plating per AMS2411 on Waspaloy material blisters after 1400 °F bake. What are the criteria for blister evaluation? Please help to clarify: size of blisters shall be less than 0.015" and 25 blisters are allowed per square inch.
If blisters are more than 25 but size are all less than 0.015" ("small blisters"), and pass chisel test, is it considered acceptable?
- Los Angeles California
July 15, 2021
A. Miong,
It's probably worth contacting SAE directly. They may not give you an interpretation, but it should at least alert them that the language is difficult to interpret.
It's possible that the intention was to say that either the presence of blisters larger than 0.015" or a blister quantity greater than 25 per square inch are separately considered not acceptable.
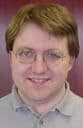
Ray Kremer
Stellar Solutions, Inc.

McHenry, Illinois
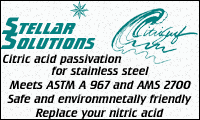
adv.: Supplier of Copper Anodes, Nickel Anodes, Bismuth Metal, & Other Metal Products for Industry & The Arts
Q, A, or Comment on THIS thread -or- Start a NEW Thread