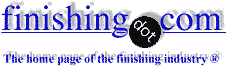
-----
Flatware Pitting - Production Problem?
2007
I represent a retailer marketing several patterns of flatware made in China by Haida and Tomerry. While we urge our customers to treat their flatware sensibly, not to use citric dishwasher detergents, not to use the high heat dry cycle, to sort their flatware handle down in the dishwasher, not to wash their flatware with other metals, we seem to be experiencing a high rate of return due to customer dissatisfaction with staining, rusting and pitting. The manufacturers assure us they are using 18/10 stainless. I'm wondering if during the manufacturing process there might be heat treatments or other processes that may be performed outside the intended tolerances, or if anyone can help us direct the proper line of questions to the manufacturer?
I have noticed that most of the prestigious brands are having their flatware produced in Korea rather than China. Can anyone speak to the differing standards of manufacturing in these countries?
Thank you for any help,
Retail / Wholesale - Halifax, Nova Scotia, Canada
A. Garbage in, garbage out. I use 1960's Made in USA 18/10 stainless steel tableware which hasn't any signs of corrosion. In 2007, China will probably produce more steel (all types) than the US, Japan, Russia, Korea & Germany combined. Some will be top quality, some bottom, probably mostly average. Companies buying low priced material w/o verifying quality get burnt. I don't have a crystal ball to allow me to see overseas (I'd be one rich consultant if I did), so no definite answers, just suggestions.
Send the stainless steel (SS) to a lab for analysis of the actual composition. 18/10 is very generic; includes SS grades with 10-12% Ni, but also 8-10% Ni. Perhaps specify 305 [17-19% Cr, 10.5-13 Ni] or 316 [16-18 Cr, 10-14 Ni, 2-3 Mo] per
ASTM A480; you may be getting free-machining 303 (contains corrosion-inducing sulfide inclusions).
Re heat treatment: Send some parts to a lab for intergranular corrosion testing (in the as-received condition) per Practice E of ASTM A262. The SS starting material should have been solutionized at 1040 °C and quenched. This minimizes chromium carbide formation, as demonstrated by passing the intergranular corrosion test. The surface condition will be better if the solutionizing is done in vacuum, inert gas or dry hydrogen or similar; you can specify 'bright annealing' as per ASTM A480. Otherwise, acid pickling is necessary. Next, I expect that the material is cold rolled, cut into blanks and stamped to shape in polished steel dies. The product should then be polished, buffed, cleaned and then passivated per ASTM A967.
Check for properly passivation: Set aside one batch of parts as a control, passivate another, then send both for salt spray testing per ASTM A967, Paragraph 16 (for 2 hours, using the ASTM B117 method). If the passivated batch performs better, the manufacturer probably skipped passivation.
Hope this helps.
- Goleta, California

Rest in peace, Ken. Thank you for your hard work which the finishing world, and we at finishing.com, continue to benefit from.
Q, A, or Comment on THIS thread -or- Start a NEW Thread