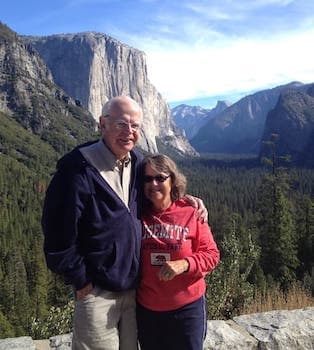
Curated with aloha by
Ted Mooney, P.E. RET
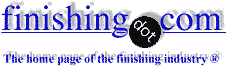
The authoritative public forum
for Metal Finishing 1989-2025
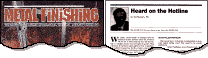
-----
Finishing tool steel for corrosion resistance
Q. I HAVE A PART MADE FROM TOOL STEEL, GR A2 AND HEAT TREATED TO ROCKWELL C50-54. IT PRESENTLY HAS A BLACK PHOSPHATE COATING PER DOD-P-16232 [ed. note: replaced by MIL-DTL-16232 [from DLA] ]. THIS PART IS EXHIBITING RUST DURING ENVIRONMENTAL TESTING. I AM LOOKING FOR A MORE CORROSION RESISTANT FINISH, THAT IS HARD ENOUGH FOR WEAR ISSUES. ANY SUGGESTIONS?
LEE ERICKSONopticals - BARRINGTON, Illinois, USA
2007
![]() |
A. In my opinion TiN (PVD titanium nitride) is your best bet, followed by plain nitriding second, specially if corrosion is not of paramount importance and the part is intended for extreme mechanical conditions such as cutting, cold forming, high pressure sliding, etc. Some electroplated coatings (thin dense chrome or heat treated electroless nickel for example) may also work but they will be limited in thickness, adhesion and hardness. Guillermo MarrufoMonterrey, NL, Mexico 2007 A. Typically, for tools that saw a lot of use, we used a hot black oxide finish and kept them very very lightly oiled with a very thin oil. James Watts- Navarre, Florida 2007 |
Q. I should have stated that the above part is not a tool. We are using tool steel and its hardness due to the way the part operates within the assembly. We are under military contract and no rust is to appear after or during operation in the field. Shiny finishes are frowned on, finish needs to be matte and prevent rust corrosion. This part is already in the field but is exhibiting rust.
LEE ERICKSON [returning]optical - BARRINGTON, Illinois, USA
2007
A. Since you still have not told us the size or shape or use of the part or the conditions that it operates in, it is nearly impossible to offer suggestions. I would suggest an iron-zinc with a black chromate as being practical and better than the phosphate.
James Watts- Navarre, Florida
2007
Q. Sorry for slow response, very busy. The part is triangular in shape one side is 2.05" the other 2.28" and is .50" thick. It has to function in an environment range of -50 to +140 °F and is exposed to rain, dirt, dust, sand pretty much anything a soldier's .50 caliber machine gun would see.
LEE ERICKSON [returning]- BARRINGTON, Illinois, USA
2007
A. My old company has a patented process that would be perfect for this application. They apply a hard coating, in this case TiAlN would be best, then zinc phosphate the coated part, followed by a light oiling. After oiling, the part is wiped down until it feels dry.
While coating such as TiN and TiAlN provide some corrosion protection, they never fully cover the surface. There are always holes down through the coating exposing the base metal to the environment. The zinc phosphate only reacts with the metal exposed in the holes, forming a crystal structure that absorbs the oil, which in turn provides the corrosion protection.
TiAlN is not the best coating for this application from the corrosion viewpoint. You'd be better off with ZrN, but ZrN is a champagne gold color, not exactly suitable for military applications, while TiAlN is a matte gray.
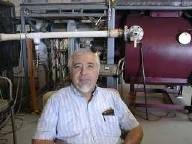
Jim Treglio - scwineryreview.com
PVD Consultant & Wine Lover
San Diego, California
2007
S7 Tool Steel Black Coating Options
August 24, 2015Q. To whom it may concern,
I currently work for US Ordnance in Reno Nevada. I am finishing my last semester of school at the University of Nevada, Reno and plan to continue working after graduating at US Ordnance with my BS in Mechanical Engineering.
I recently was asked about coating S7 tool steel so I started doing some research. The three coatings we are looking at are Phosphate, Black Oxide, and Black Nitride. We do phosphating in house so being able to phosphate the part would be preferred; however, from past experience and research I have found that the S7 does not take phosphate well. We have been able to phosphate the parts but it usually requires the part to be dipped in the tank multiple times.
A local metallurgist recommended black oxide. I know we have black oxide coated S7 tool steel parts in the past and it works well. I would like to stay away from Nitride personally due to hydrogen embrittlement issues we have had in the past, this is a very high stress part. We actually had a case of a batch cracking during test firing. All were black nitride coated and baked for a few hours afterwards although clearly the parts were not baked properly (unfortunately no records exist of time and temperature used for the baking process).
Will the black oxide coating be a viable solution? A local vendor offered to coat a sample part for me, I will drop it off today and hopefully have it back tomorrow.
Am I overlooking good options? We do have to follow certain Mil Specs but I am always interested to hear other ideas.
Thanks,
Engineer in Training - Reno, Nevada, USA
A. Hi Justin. What finishes are satisfactory is going to depend on the application. Black oxide is an extremely thin finish and cannot accept nearly as much wax or oil as a granular finish like zinc phosphate or manganese phosphate. I am surprised that nitriding would cause hydrogen embrittlement (but I'm no expert on the subject), but not surprised that it could cause failure since the hard surface might crack under tension or suffer fatigue stresses. I like Jim T's idea of TiAlN as much as anything, although I don't know the application.
Regards,
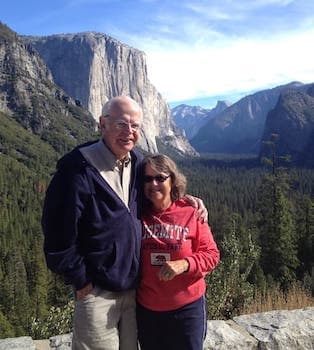
Ted Mooney, P.E. RET
Striving to live Aloha
finishing.com - Pine Beach, New Jersey
August 2015
Q, A, or Comment on THIS thread -or- Start a NEW Thread