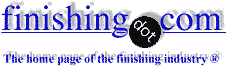
-----
Nickel or Other Plating on Copper + Stainless Steel for Service at 600 °C
Q. I am looking to plate copper + stainless steel with nickel or similar material for use at 600 °C in a high vacuum chamber. The stainless steel tubes are soldered to the copper plate then everything is plated. We have already tried electroless nickel. As heating occurs, is changes to brown to maroon to blue to a pale green/yellow color. It then blisters and peels off at 500 to 550 °C. I was informed by my vendor that they do not have anything that will work at 600 °C. This test was done in atmosphere. Previously I was under the understanding that nickel would work at these temperatures. Can someone suggest a plating/process to use? We can use anything that is compatible with a high vacuum.
Thanks,
- Boulder, Colorado, USA
2007
![]() |
A. I did not think that high temp silver solder was functional at 600 °C. That is high. The differences in coefficient of thermal expansion should make this joint under considerable stress (impending failure) or be relatively tiny tubes. - Navarre, Florida A. A. Electroless Ni is an alloy (normally 7-12% P) that shrinks when heated and has a moderate melting point of about 880oC. Sulphamate nickel (+99.9% Ni, melting point +1,400 °C) is usually plated very thick (sometimes over 0.100") on copper mold plates that are used for continuous casting of steel at 1,500 °C (mold is water cooled but nickel surface has been found to reach above 800 °C). But remember, anything may fail if adhesion is not superior. Guillermo MarrufoMonterrey, NL, Mexico |
by Jack Dini
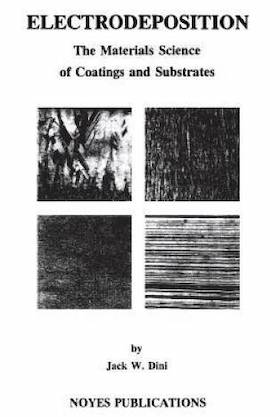
on eBay or Amazon
or AbeBooks
(affil link)
A. Solder melts < 800 °F (427 °C). Maybe actually brazing?
Rapidly (?) heating as-plated electroless nickel (EN) in air sounds like sabotage. Done properly, EN can be heat treated to 800 °C. However, I don't see any advantage to electroless nickel (EN) vs. electroplated nickel w.r.t. properties for your application. Maybe uniformity of plating? Also, a low-phosphorus EN may be more suitable than a mid- or high-P EN.**
Adhesion seems poor; use a Wood's nickel strike and follow either EN or electrolytic nickel plating with an adhesion bake.* Slowly heat and hold 1-4 hours at 190 °C to improve adhesion (via Ni interdiffusion with Cu & SS) while minimizing CTE problems. Then, slowly heat to 600 °C (even to 750 °C), followed by slow cooling to < 200 °C. Thereafter, rapid temperature changes can be made.
* ASTM B656 [withdrawn 2000] & ASTM B733: "Inert or reducing atmospheres or vacuum sufficient to prevent oxidation are recommended for heat treatment..." An Ar-5%H2 atmosphere is suitable.
** Mid- & high-P EN deposit with amorphous microstructures. During initial heating, amorphous EN crystallizes at ~300 °C, resulting in a 0.1-1.3% volume shrinkage. This causes microcracking, which reduces ductility and corrosion resistance. Properties can be largely restored by prolonged annealing at 600-750 °C -- cracks may heal [if not oxidized!], although hardness will be less than if heated to only 400 °C.
References:
• ASTM B656 & ASTM B733;
&null; W. H. Metzger, Jr., in Symposium on Electroless Nickel Plating, ASTM STP No. 265 (1959);
• Chapter 4 in "Electroless Plating", Glenn O. Mallory & Juan B. Haidu (eds.) (1990) [on
eBay ,
Amazon, or
AbeBooks affil links]
.
Electrodeposition
[on
Amazon
or
on AbeBooks affil links], Jack W. Dini, pp. 153-4 (1993).
- Goleta, California

Rest in peace, Ken. Thank you for your hard work which the finishing world, and we at finishing.com, continue to benefit from.
Q, A, or Comment on THIS thread -or- Start a NEW Thread