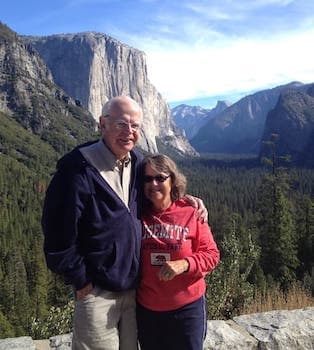
Curated with aloha by
Ted Mooney, P.E. RET
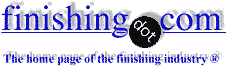
The authoritative public forum
for Metal Finishing 1989-2025
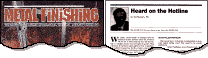
-----
Corrosion in centrifugally casted and machined CF8M Seat rings
2007
We are using C8M grade rings in the Water treatment pressure vessel. These rings are centrifugally casted and fully machined all over. No cast surfaces are left .Upon putting on line within 3 months we observed these rings have started corroding with a formation of Red rust.
The soLUTION ANNEALING AND mICRO FOUND OK. In chemistry check we found Si was up to 1.88% as against 1.5%maximum allowed.
Want to know if this increase in Silicon has any impact on the corrosion
Component Speciality India P ltd - Bangalore, Karnataka, India
Some specifications allow 2.0% Si for CF8M (e.g., ASTM A743) although ASTM A351 (pressure-containing parts) has a 1.5% limit. I believe this is for structural reasons, to avoid intrangranular formation of a Laves phase, Fe2Mo (stabilized by Si), which forms slowly at 600-900 °C. Mo additions necessitate lower Si (cf. 2% Si allowed in CF8), while higher Mn, Ni & N contents allow higher Si. Solutionizing and rapid cooling should eliminate any Laves phase as well as most carbide.
Higher Si increases resistance to acids, oxidation, galling and wear. Some austenitic stainlesses with higher Si: CN7MS, Carpenter's Gall-Tough®, 302B, Nitronic® 60, UNS S30600, S32615, S38815 & S70003. So, Si probably not the problem.
Try cleaning and passivation in place. If rusting recurs, conditions may be too severe for CF8M. Any intergranular corrosion? If so, and if service temperature is moderate ( < 425 °C), try the low carbon grades CF3M or CF3MA. This should avoid any (Cr,Fe)23C6 carbide formation during quenching.
- Goleta, California

Rest in peace, Ken. Thank you for your hard work which the finishing world, and we at finishing.com, continue to benefit from.
2007
Q, A, or Comment on THIS thread -or- Start a NEW Thread