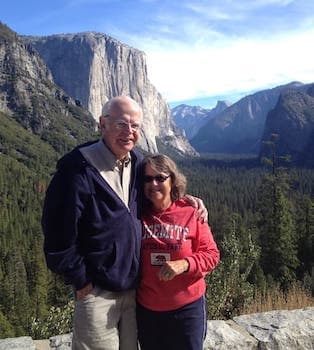
Curated with aloha by
Ted Mooney, P.E. RET
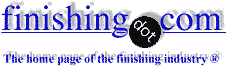
The authoritative public forum
for Metal Finishing 1989-2025
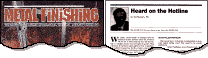
-----
Powdercoat and achieve 1000 hrs salt spray with little or no pre treatment
I need to achieve 1000hrs salt spray on a range of large tanks manufactured from hot rolled plate. I have to powder coat and not wet spray because of the shape of certain areas of the tanks. I can't set up a dipping system for zinc/iron phosphate as the quantities are too small and I can't shot blast as the vessels are leak tested before finishing. any suggestions would be greatly appreciated.... is there such thing as a powder form E-coat/primer that would give me the necessary results... ?
Everett Johnston- Wexford, Co. Wexford, Rep. of Ireland
2007
2007
The pretreatment system serves a number of roles, Everett, but one of them is to get the parts clean. Re-word your inquiry in your own mind like this: "I have steel parts and wish to deposit a layer of powder coating on them which will adhere properly to the steel despite the fact that in between the steel and the powder there will be a layer of oils, greases, and soils of poorly defined composition".
So I'd say your most serious issue is how to get the parts clean and assure that cleanliness. There still may be a number of ways to do that despite the limitations of the project. Good luck.
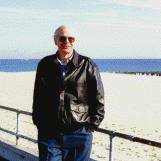
Ted Mooney, P.E.
Striving to live Aloha
finishing.com - Pine Beach, New Jersey
As Ted says, getting the parts clean is all important. If you expect any sort of adhesion, then you have to let the powder be in contact with the real substrate, not with surface contaminants.
There are powder-based primers, including zinc rich primers, but what will you stick them to? You could achieve good adhesion between the top coat and primer, but if the primer is not stuck to the substrate you're no better off.
Tanks made of Hot Rolled plate, presumably arc welded will have mill scale, rust, fabrication dirt, Mig welder anti-spatter spray perhaps, drilling lubricant (if holes drilled) and such like contamination. To achieve 1000 hours SS test without competent pretreatment. You say the small quantities prevent setting up pretreatment. So perhaps you should contract this job out if its too big for you, to a coater that can do big stuff, and do it with the pretreatment.
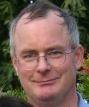
Geoff Crowley
Crithwood Ltd.
Westfield, Scotland, UK
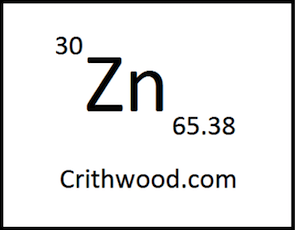
2007
2007
Considering your predicament there can be a few steps which might bring you closer to your objective.
As already pointed out pre treatment and cleaning are critical. Mill scale, oils and grease have to be removed before you can get good adhesion. Can you use HRPO - hot rolled pickled and oiled sheets? This will remove the mill scale!
Is it possible to do full dip phosphating before you do the welding? The phosphating will need to be protected with some polymer film which can be removed at the line of welding and then put back after the metal has cooled.
Can you actually try powder coating all metal before welding? Whatever surface is damaged due to the high temperatures of welding will require removal of the damaged coating and then a fresh layer?
And having said all of the above, may I know:
How do you plan to powder coat tanks of such size?
How do you plan to heat tanks of these sizes to nearly 200 degrees C?
What will happen to leak testing after the tank is subjected to thermal stresses at 200 degrees C?
When a kid in college, we had a dictum - If you cannot convince, confuse!
Wish you the very best.
Mohali, Punjab, India
Everett, the short answer is no, mainly because most "best case scenario" (cleaner, iron phosphate, DI, spray impingement) systems will only give you about 600 hrs on steel. Forget dipping them, if you seal them they'll float, if you allow them to fill they'll be way to heavy to handle.
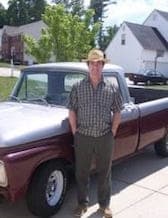
Sheldon Taylor
supply chain electronics
Wake Forest, North Carolina
2007
May 27, 2009
Have you considered sandblasting the metal? That'll clean up the layer of oil/grease, and good sandblasting will give that micro-rough texture that will greatly increase surface area to give the powdercoating something to really hold on to, with a relatively smooth finish with only about 3-4 microns thick powder.
If you do want to dip, just dip them in sideways -- then the liquid inside can just run out the open "side" (normally the top).
I don't know what you mean when you say you can't shot blast -- we must be using terminology differently..
- Redlands, California, USA
Q, A, or Comment on THIS thread -or- Start a NEW Thread