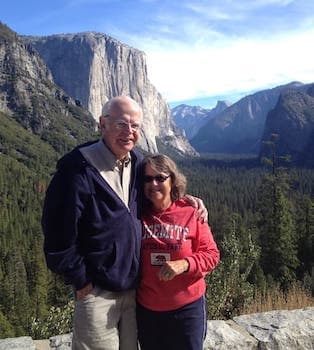
Curated with aloha by
Ted Mooney, P.E. RET
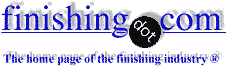
The authoritative public forum
for Metal Finishing 1989-2025
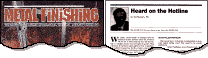
-----
Nickel Electrowinning Q&As, Problems & Solutions
Q. Hi, I am trying to make nickel electrolysis and I have a nickel sulphate solution that is coming from mining industry.
I used between 5-6.5 amperes and solution nickel concentration was around 35-45 g/l.
My end product was metallic nickel powders and I want to obtain metallic nickel foil from electrowinning. Do you have any idea for me to try and get foil?
- Oslo, Norway
October 17, 2022
A. Hi Alice. A really proper nickel plating solution for generating a nice deposit would be a Watts Nickel solution, which contains about twice as high a concentration of Nickel sulphate as that, plus some Nickel Chloride, Boric Acid, some small quantities of addition agents like wetters, levelers, and brighteners, and operates at 140 °F.
While it's fairly easy to get nickel to plate out of solution, it's not so easy to get a nice foil-like deposit :-)
I think the first thing I'd try is adding about 38 g/l of boric acid, a small bit of sodium lauryl sulphate wetter, raising the temperature to 140 °F., and providing some agitation somehow (air agitation, spargers, or mechanical movement. Please advise whether this brings any progress at all. Thanks..
Luck & Regards,
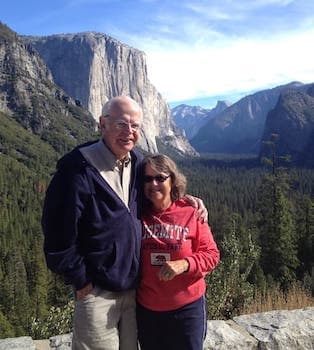
Ted Mooney, P.E. RET
Striving to live Aloha
finishing.com - Pine Beach, New Jersey
⇩ Related postings, oldest first ⇩
I am looking to remove dilute concentrations of nickel in the rinse water from a nickel sulphate plating bath. Currently I've found that @ pH 3-4 using a chelating type IX resin removal from the rinse is near 100%.
After complete loading of the IX column I find that removal of the nickel from the resin (regeneration) is easily accomplished via
10-15% sulfuric. My resultant is a volume of @ 10-15 g/l Nickel in the sulfuric solution. Precipitation of this material is then very simple.
My question then becomes, is it possible to electrowin this acid solution to attain a 1 g/l Nickel-sulfuric solution which could be reused as regenerant? Currently, the hydrolysis of the water/acid mixture prevails and all that happens is the liberation of H2/O2. Assuming this to be impossible, how about electrowinning the solution at an increased pH level, or alternate temp, or from a different regenerant... For the sole purpose of recovering the nickel.
Has anyone experience with this?
- Fergus Falls, Minnesota
2000
2000
One possibility is to dilute it to the desired nickel strength, adjust the pH to what you need, carbon treat it and drum it for future use. I would have it analyzed for other metals that could affect your bath. Like copper and iron. Ion chromatography works well for this and atomic adsorption is a little bit more specific.
You may have to peroxide treat to remove the iron.
Dummying helps the solution also.
For electrowinning, you need to raise the pH to about 4 to 4.5 and check it several times a day as it will change because you will be using an insoluble anode. Yes, you will get some H2 and O2 given off, but it will be minimal. Stay below 4 volts and you will have a lot less. Intense agitation speeds up the process, so you could use a lower voltage. This nickel will include some of the copper, so you are are right back where you started above.
- Navarre, Florida
You might consider using another type of resin that doesn't require 10-15% sulfuric acid for regeneration. Resins are available that will remove nickel from your rinsing bath only requiring 2-3% sulfuric acid for regeneration. You will need less alkali chemicals for pH-adjustment to pH 3-4 for electrowinning and of course save on H2SO4 consumption.
Ruud Gerritsen- Simpelveld, Netherlands
2000
2000
Brad,
I have personally accomplished this task several times, and in varying scales up to several hundred pounds of recovered nickel per day.
We have a process that we use to regenerate ion exchange resins that gives us 120-130 g/L of metal in the solution (and for the doubting thomases out there, we are NOT taking cuts of the regeneration!)
You could use a weak acid resin, as is suggested previously, however you may find that this resin will scavenge other unwanted items from the solution too, and render it unacceptable for plate-out. I would stick with a good quality chelated resin. Pound for pound, it will hold more nickel.
I could fill several pages discussing this. You're on the right track - just have to make a few adjustments in the approach.
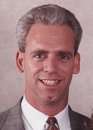
Tom Baker
wastewater treatment specialist - Warminster, Pennsylvania
Electrowinning is a process that requires special equipment, mainly special cathodes with high surface area.


Sara Michaeli
Tel-Aviv-Yafo, Israel
2000
2000
Sara,
Actually, your suggestion to use high surface area cathodes is a good one, however not necessarily always required. You can plate out quite effectively on low surface area (2 dimensional cathodes - basically plates) with the correct plating parameters. Remember the 5 basics - concentration, current density, agitation, temperature, chemistry. Keep control of these, and you can just about plate out anything.
Nickel is no different, but does require careful control over the free acidity present in the solution (creates hydrogen, which burns the plate and passivates it). Many of our earlier clients used to use boric acid to give the solutions some stability, however with boron limits getting tighter, that may not be the best option anymore. We use an acid recovery unit on the system to remove the free acid as it is created (1 lb metal plated makes 1 lb of acid).
High surface area cathodes were originally developed to plate out of very dilute solutions as an effluent control device. As limits dropped, their effectiveness was challenged to meet sub-ppm requirements. However, they gained acceptance as a straightforward electrowinning system for certain applications, such as plating out of IX regenerants. Care should be taken, however, to evaluate the cost effectiveness of using consumable cathodes in a high concentration application. Based on the resale value of the metal, you might spend more on replacement cathodes than the metal is worth. In that case, you could use a low surface area cell, followed by a high surface area cell to get all the metal out.
Good design and understanding these costs is critical.
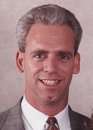
Tom Baker
wastewater treatment specialist - Warminster, Pennsylvania
Q. I have nickel solution waste from electroplating industry. Our company try to find an effective electrode to recover nickel from that solution by electrowinning process. We've tried to use Cu as electrode but not reach satisfaction result. Therefore, we ask you to help us to find right electrode.
Thanks,
Yori Suaib- Tangerang, Banten, Indonesia
2001
A. You don't say what type of nickel bath is being processed, so an exact selection of the correct electrode is hard to determine. For the sake of the answer here, let's assume that it is a decorative or bright nickel (Watts or similar). You also do not identify whether you are trying to find an anode material or a cathode material. I'll try to explain both here.
ANODE
These baths contain a fairly high amount of chloride and will therefore require an electrode that is resistant to chlorine attack, as chlorine will be evolved at the anode electrochemically. Other base metals are not suitable for use as anodes, and the use of graphite blocks, lead, etc. all have issues withstanding what is a fairly aggressive environment. The complicating factor here is also the production of oxygen at the anode too. Most materials are resistant to either chlorine or oxygen, but not both, or at least not well.
You should look at inert or insoluble catalyst coated anodes applied on an inert substrate. Usually, the best bet is to use a layered inert anode material. The chlorine attack usually occurs on the substrate itself, so it should either have a high chlorine overpotential (such as tantalum), or it can be titanium with a small layer of platinum electroplated to it. Then, the electrode substrate can be coated with an oxygen evolving catalyst, such as iridium dioxide or similar coatings. This will give you an excellent lifetime in most of application, however care must be exercised not to allow the electrode to be cathodic, or the coating will be quickly lost.
CATHODE
We have found that a copper cathode sheet will work very well in nickel recovery applications, if the material is flashed with a nickel layer prior to use. Also, care must be exercised to not allow the cathode to be exposed to air after the electrowinning process is started, or the nickel will quickly passivate, making it all but impossible to restart the electrowinning process. In straight nickel plating, you can remove the passivation layer from nickel anodes by immersion in nitric acid or some other activator process - here, you are not dealing with an annealed material, but a substantially grainy deposit, and the material will continue to oxidize or still be partially passivated.
You might also look at using thin nickel sheet that has been slit and expanded as a cathode. It increases the surface area significantly, and the nickel to nickel grain structure allows you to electrowin a very refined deposit.
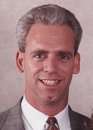
Tom Baker
wastewater treatment specialist - Warminster, Pennsylvania
Q. Our company is dealing with waste management and wants to recover Ni from waste Ni solution (30 g/L). The other metal content is very low, but it has organic contamination. When current density of 1.5 A/dm2 was applied, we find Ni comes out with Ni(OH)2 sludge and cracking and peeling of deposit. Why does this occur? Another problem is the anode. We use Ti anode and the resistance is very high. Only 100 A achieved at applied 10 V. (we expect 5 v and 1000 A). So we change to stainless steel 316 (10 V and 600 A were achieved). May I know why this happen?
Thank you
- Singapore
2006
![]() |
A. I once saw Ni reclaimed from spent electroless nickel solutions with great efficiency. The operator added ammonium hydroxide to the waste to bring the pH up to about 10. He got very solid, adherent deposits. ![]() Dave Wichern Consultant - The Bronx, New York A. Ti is a poor conductor of electricity. SS is a poor choice as it will dissolve with + current. To plate out the nickel, you need a large cathode area, superior agitation and tight control of the pH, since it will rapidly drop when you use an insoluble anode. - Navarre, Florida |
A. Nickel is one of the more difficult metals to electrowin, especially to low concentrations.
In general, it requires a heated solution, pH control, agitation, and a buffer such as boric acid in order to prevent nickel hydroxide formation at the cathode.
You may want to consider other possibilities such a chemical reduction to metal with a strong reducing agent such as sodium borohydride.
consultant - Cleveland Heights, Ohio
I appreciate Mr David, Mr James and Mr Lyle's suggestions and advice.
Q. I would like to ask another question. Normally how can we clean the cathode (stainless steel)? I tried to use NaOH(5%) with detergent. Can I use any acid? I feel that the surface cleaning affects the quality of deposit greatly. We have changed to carbon anode and it seems to work well.
- Singapore
2007
Lead anodes in nickel electrowinning
Q. In my experiment, I use lead anode to electroplate out the nickel from nickel sulphate solution . However the lead is also deposited on the cathode which contaminate the purity of my electroplated nickel product. As I know, the dissociation of the lead anode will compound the lead sulphate which is in solid form without chemically pollute the electrolyte. But in fact, my plating product did contain the 1 % of Pb in the nickel metal.
My question is what do I do to eliminate the Pb ions in the electrolyte to prevent it from plating on the cathode?
Thanks to anyone who answer my question.
Chemist - Malaysia
2007
A. Platinized titanium anodes would probably solve this problem, HF.
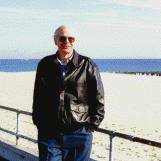
Ted Mooney, P.E.
Striving to live Aloha
finishing.com - Pine Beach, New Jersey
Q. Thanks Mr Mooney. To cut cost of my electrowinning unit, lead anode will be more suitable to use. Is it possible to use the lead anode without contaminating the electroplated product?
HF AngChemist - Malaysia
2007
Buffer for nickel electrowinning
2007Q. Hi all, I do a experiment to test the effect of buffer on the nickel electrowinning (Nickel sulphate bath). The parameter are as below:
Electrode : lead anode & Stainless Steel cathode
Nickel concentration : 40 g/l of Ni
current : 3 Amp
Duration : 3 hours
pH : 3.5-5
I did two tests: one with 40 g/l of boric acid as buffer and the other one without buffer in order to observe their pH change and volume of ammonia
⇦ this on
eBay or
Amazon [affil links] aqueous used for pH adjustment. However, I discovered that the use of the buffer did not give significant difference for maintaining the constant pH with the one without buffer. For instance, in both of the tests, their pH similarly dropped below pH 3.5 in every ten minutes that 2 ml of ammonia aq was added to rise back the pH around 4.5.
Then, is the use of buffer necessary for electrowinning? Or did I use the wrong buffer or quantity of buffer used for the electrowinning?
Chemist - Malaysia
A. You are using an insoluble anode. A lot of hydrogen is formed because of it, so the pH must drop. No buffer that I am aware of will compensate for that amount. You simply generated more acid than the buffer could accommodate.
James Watts- Navarre, Florida
2007
A. I once consulted for a guy that literally had collected a million gallons of waste nickel plating solutions, mainly from the electronics industry. Most of the solutions were full strength modified watts nickel baths with a little contamination. The idea was to electrowin the nickel from the solution. The problem was that, when using inert anodes, the hydrogen ion produced from the water splitting rapidly reduces the pH. This lowers the cathode efficiency and, at some point, maybe a pH of 1 or 2, the nickel stops plating altogether.
I tried all sorts of buffer systems with no success. The problem was solved by producing nickel carbonate, from some of the solutions, and continually using it to raise the pH. This also replaced the nickel in the solution. If I remember right, we put the nickel carbonate in anode bags and hung them in the solution. The dissolution tended to stabilize itself, since it slowed down as the pH increased. We used saccharine as a grain refiner.
- Nevada, Missouri
2007
Q. Thanks for sharing your experience. Mr Chris Owen, I know the nickel carbonate has the function to neutralize the acid of the electrolyte bath, so put nickel carbonate into the anode bad to slow down the pH drop is the good idea , however for the cost effectiveness, is it possible to use ammonia solution as the pH adjuster (raise pH) instead of using nickel carbonate?
Hf Ang [returning]Chemist - Malaysia
2007
A. Just one thing about ammonia that may be important to you - it is a stress inducer and will result in tensile stress being imparted into your deposit.
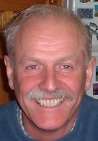
Trevor Crichton
R&D practical scientist
Chesham, Bucks, UK
2007
Q. Thanks for your information, Mr. Trevor Crichton. Do you mean that ammonia is applicable but with the disadvantage that it produces tensile stress on the deposit product?
As I know, the tensile stress will cause wrinkles on the plating; however, will it affect the efficiency of nickel deposition? Because my purpose is to electroplate out the nickel for nickel recovery.
And besides resulting the tensile stress, does ammonia create other effects on the plating as well as the electrolyte bath? According to some journals and experiments that I did, adding of ammonia do compound with nickel and easy to form crystals (even though the concentration of nickel is lower than 20 g/l of Ni). So does anyone have any ideas to the prevent the crystallization of the Nickel salt that resulted from ammonia used?
Chemist - Malaysia
2007
A. Most modern nickel electrowinning systems use membranes to separate the anode compartment from the cathode compartment. That prevents the hydrogen ion, produced at the anode, from entering the cathode compartment, thus not lowering the pH. There are many references to this on the internet.
Chris Owen- Nevada, Missouri
2007
Q. I just want to ask some questions.
1) Will your lead anode deposit small amount of lead onto the stainless Steel cathode together with your nickel?
2) What is the effect of lead if it does get deposited?
3) Does refilling the recovered nickel solution with constantly new nickel solution maintain the pH?
Thank you.
- Singapore
2007
A. Personally I would not use ammonia, as it will induce stress and continued use of it will just increase the stress and cause other problems. The simplest way to keep the pH up is to something like nickel carbonate or even sodium hydroxide. I know people claim that sodium hydroxide will also induce stress from the sodium, but I don't think I have ever seen it. The idea of a divided cell also has its attractions
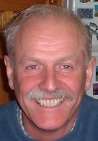
Trevor Crichton
R&D practical scientist
Chesham, Bucks, UK
2007
A. 1) Will your lead anode deposit small amount of lead onto the stainless Steel cathode together with your nickel?
From previous posts, it seems like it will slightly dissolve and co-deposit. Use carbon anodes.
2) What is the effect of lead if it does get deposited?
The deposited nickel will be less pure.
3) Does refilling the recovered nickel solution with constantly new nickel solution maintain the pH?
Without the additions of nickel carbonate, I don't think you'll ever be able to keep up with lowering of the pH. You'll never get all of the nickel out. Use a membrane and you won't have to worry about all these problems.
- Nevada, Missouri
2007
Q. Mr. Crichton, I had used the sodium hydroxide for pH adjustment before, the NaOH will first compound with the nickel ions in the nickel sulphate solution, coagulate into greenish precipitate before it raised up the pH. what should I do when I use the NaOH for the pH issue?
Besides, the lead anode do contaminate a bit of deposited metal on cathode. In my experiment,there was 0.2% of Pb in the electroplated nickel.
Chemist - Malaysia
2007
![]() |
A. You absolutely will have nickel precipitation by adding concentrated NaOH to a nickel tank. You can make a dilute solution by using some of your tank solution in a pH adjusting tank that overflows back into the main tank. You put the caustic into the adjusting tank with extreme agitation and dropwise! Consider a metering pump. James Watts- Navarre, Florida 2007 A. Sodium hydroxide reacts with dissolved nickel salts to form insoluble nickel hydroxide, which is a green gelatinous substance. However, the excess acid in the bath will dissolve the nickel hydroxide to form the nickel salt of the acid and water. The nickel hydroxide may take some agitation to dissolve it, but it will go back into solution. Obviously do not have your filter pump on when you do this, or the nickel hydroxide will be filtered out. ![]() Trevor Crichton R&D practical scientist Chesham, Bucks, UK 2007 |
Q. I met a few problems when I used the diluted NaOH (24%) as pH adjuster:
- dropwise of NaOH is time taken to adjust pH.
- The diluted NaOH (24%) still able to precipitate the Nickel hydroxide out and manually strong agitation/stirring was required to dissolve the substance, but some can not be dissolved.
- more volume of the diluted NaOH used to raise the pH (compared to ammonia) ,that cause the dilution of the nickel concentration in the nickel sulphate bath and will affect my calculation of the nickel plating efficiency.
Do you all have any ideas to the problems?
Besides, May I know more regarding to the membrane used in the modern electrowinning? I found that there are different kind of membrane, e.g.: nafion membrane ,polymer electrolyte membrane... which kind is more suitable? and also can the membrane act as the anode bag ,so that the hydrogen ions can be trapped in the bag?
HF Ang [returning]Chemist - Malaysia
2007
A. By using a pH adjusting tank that overflows into the nickel tank, you can use air agitation or mechanical agitation very well or a combination of both.
ammonia forms a nickel complex, so it will affect your plating in a negative manner.
Membrane technology is probably the better way to go. This is way beyond analytical chemistry, so you need to find a company that will sell you the correct product and not try to go the cheap route by designing your own.
- Navarre, Florida
2007
A. About the membrane, alternatively you can use a flow through diaphragm (fine mesh cloth that slowly allows solution to pass). You then need to setup your cell so that the cathode chamber solution is higher than your anode chamber solution. This will minimize acid generated at the anode from getting to the cathode. You will need to pump solution out of the anode chamber.
James Vaughan- Brisbane, QLD Australia
February 24, 2009
Q. We are a recycling company dealing with heavy metal containing scheduled wastes namely from water treatment plants. Usually the sludges have high content of Aluminium. But those from industry generally have high Nickel content -- around 500-500 thousand ppm of Nickel. I would like to know how electrowinning can effectively and selectively remove Nickel.
shri prasanthi- Pahang, Malaysia
January 2, 2009
Hi, We started nickel electrowinning recently.
The electrolyte prepared after removal of impurities by solvent extraction using d2ehpa (P-based solvents), then NiSO4 solution treated with activated carbon.
We are using following conditions for electrowinning bath pH 5, Temperature 54 to 60° C., Ni 80 g/l, sodium acetate 75 g/l, sodium sulphate 75 g/l, Magnesium sulphate 10 g/l, current density 300 amp/m2, Cathode SS, Anode Insoluble Pb. After 1 hour plating, the Nickel plate is stripped out from SS cathode. Ni plate obtained is highly brittle in nature, but we require highly ductile nickel plate.
Can anybody help me to solve this problem and obtain a Ni plate with brightness and high ductility.
Thanks & Regards,
Karthick kumar
product designer - COIMBATORE, Tamil Nadu, India
August 10, 2011
Q. We have NiCad battery scrap 200 mesh in powder.
Our two questions are as below:
We are interested in obtaining nickel and also interested in obtaining cadmium
Please inform us we can use electrowinning or electrolytic
amp / volts/ mol chemical/ ratio, etc., and also inform us anode and cathode material metals to use.
thanks
- Lahore, Pakistan
September 13, 2011
Q. Dear sir, I tried to electrodeposit nickel from its sulphate solution and bath condition was 27 gpl Ni; 110 gpl sodium sulphate ; pH 3; using nickel carbonate as adjusting pH agent and current density of 180 a/m2, after addition of 10 gpl boric acid the deposited cathode became very brittle! What is the problem?
M. Taghizadeh- Tehran, Iran
January 30, 2017
A. Hi M. I am a bit confused that you are worried about the cathode material being brittle because you don't seem to be describing ideal conditions for electrowinning nickel.
Are you using membranes as suggested by Chris Owen? Please take a moment to introduce yourself and explain why you are trying to electrodeposit from this solution so we have some more clues. Thanks!
Regards,
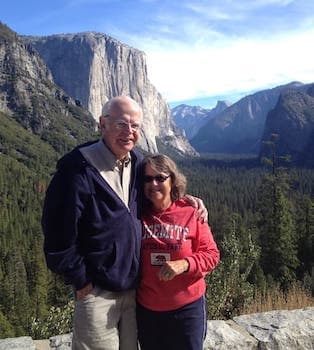
Ted Mooney, P.E. RET
Striving to live Aloha
finishing.com - Pine Beach, New Jersey
January 2017
![]() |
Q. Dear Mr. Mooney - Tehran, Iran January 30, 2017 A. Three things that you should consider. Consultant - Cleveland Heights, Ohio January 30, 2017 |
Q. Hello sir. I have a question: why do you use nickel carbonate for adjusting the pH, and why don't you use nickel hydroxide?
What's the difference between NaOH and NaCO3 in precipitating the nickel?
- tehran,ran
August 1, 2017
A. Hi cousin Reza. Just to be sure, you are still talking about electrowinning of nickel from a nickel sulphate solution -- you have not shifted to a discussion of nickel electroplating? ... because we have several long threads focused on NaOH vs. NaCO3 for pH adjustment of nickel plating solutions. Are you using membrane technology in your electrowinning efforts? This seems to be a central pivot point in the discussion.
Mr. Owen and Mr. Ang described the problems they had when they tried to use NaOH. Please try to avoid steering the thread into abstract issues, but tell us who you are, what you have been trying to do, what successes you've achieved, and what difficulties have arisen. Thanks!
Regards,
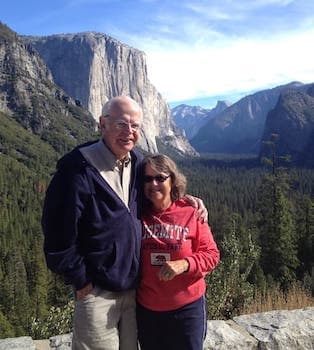
Ted Mooney, P.E. RET
Striving to live Aloha
finishing.com - Pine Beach, New Jersey
August 2017
Q. Hi Ted. I'm trying to electrowin nickel from a sulphate solution that has 70-80 gr/lit Ni, 10 gr/lit boric acid and a little saccharin. I have used a membrane and the acid of my anolyte has 40-50 gr/lit sulfuric acid. I don't have the pH problem for catholyte.
I use the anolyte for leaching. I want to know which one is better for increasing the pH of PLS to precipitate Fe between NaOH , NaCO3 or CaCO3?.
I used saccharin for additive and I have a smooth and bright nickel cathode, but it has little ductility. Is it important? What do you think about saccharin?
Thanks for your attention.
- tehran,iran
August 3, 2017
9th Edition, Vol. 5
"Surface Cleaning, Finishing & Coating"
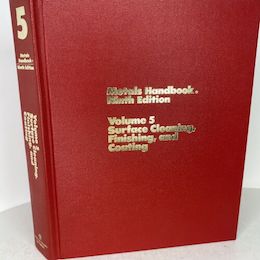
on AbeBooks
or eBay or
Amazon
(affil links)
A. Hello again Reza. I curate these discussions and I like to think that I know what is needed to keep the discussions moving forward. But I don't remember ever having even seen a commercial nickel electrowinning installation :-)
Saccharin is probably okay for your purposes, and is a stress reducer. Trevor Crichton offers some good info about how much to use in letter 16892. The ASM Metals Handbook vol. 5 .
talks quite a bit about brighteners, carriers, secondary brighteners, etc., but is directed towards bright nickel electroplating from a Watts bath rather than electrowinning from a sulphate bath. If you put "nickel electrowinning" into the custom search engine you will find a number of interesting discussions on the topic. Good luck.
Regards,
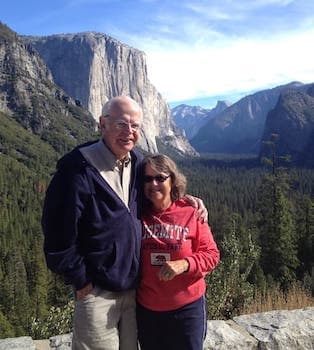
Ted Mooney, P.E. RET
Striving to live Aloha
finishing.com - Pine Beach, New Jersey
August 2017
August 2, 2017
A. Reza,
It's been 30 years since I ran that big nickel electrowinning tank and I can't remember some of the details. I can't recall why we used nickel carbonate instead of nickel hydroxide. Both would be totally consumed and nothing would build up and cause problems, like the use of NaOH or Na2CO3 would. We probably used the carbonate because it was safer to work with than the hydroxide or, maybe we had a ready supply of Na2CO3 in stock.
I'm thinking we also ran constant filtration and dummied the solution every so often. The solution was made up as a standard watts bath, and we used saccharine as a leveler and I'm thinking we also used a non-pitter. The anodes were carbon and the cathodes were passivated stainless sheet with plater's tape wrapped around the edges to make it easier to remove the nickel. That way, the nickel wouldn't plate around the edges. I'm thinking we just flexed the cathode a bit and the nickel popped off in large pieces.
We probably had 15-20 long anode bags filled with nickel carbonate hanging on the bars. With inert anodes, the pH could drop pretty fast but the nickel carbonate kept the pH up at a reasonable level, right around 4, if I recall. It also, of course, replenished the nickel in the solution. The dissolving of nickel carbonate was pretty much self-regulating, since its dissolution rate decreased as the pH increased.
I do remember experimenting with the use of ammonia for pH control and, like Mr. Ang, I found that this wouldn't work because crystals of nickel ammonium sulphate very soon started forming in the solution.
- Benton, Arkansas , USA
Q, A, or Comment on THIS thread -or- Start a NEW Thread