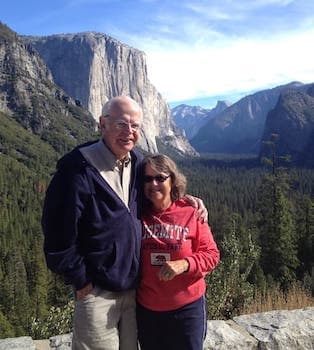
Curated with aloha by
Ted Mooney, P.E. RET
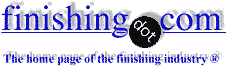
The authoritative public forum
for Metal Finishing 1989-2025
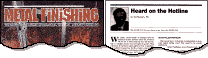
-----
Chem-film colors: are gold and yellow the same?
June 26, 2021
Q. I am a spray painter , I got a job to make and paint 200 pieces of wall mount name plates.
Plates will be made from 4mm thick Aluminum sheet (any grade can be used).
Client wants a mirror gold finish, initial idea was to use chrome spray paint, it is not available here and very expensive to import.
I saw this method on youtube using Alodine 1201
⇦ this on
eBay
or
Amazon [affil links] , along with 2-part clear coat ...
Will it give good gold like finish? Will it last long?
- Hubli, Karnataka, India
A. Hi Anurag. Alodine & Iridite are brand names for chem-film processes for aluminum. MIL-DTL-5541 [⇦ this spec on DLA] is a generic specification you can use.
I would expect gold colored hexavalent chrome chem-film to look generally as you see in the video (when applied to a buffed component), and to be quite robust and corrosion resistant. However, there are several provisos here ...
First, dry it at moderate temperature (140 °F is the maximum); then let it cure for at least 24 hours.
Second, most paint (probably including two-component clearcoat) is usually applied over very thin and transparent chem-film. As you get thicker, for a more saturated color, the propensity to be 'shearable' such that the clearcoat and half the chem-film peels off will increase. I would have one nameplate done immediately and see how it holds up as you proceed with the rest of the project.
Third, chem film is a 'functional' finish, not a 'decorative' one. The video shows a uniform finish, but over a small, geometrically simple area. Your nameplates might be larger, but hopefully don't have corners, welding or rivets, pockets, etc., working against that consistency.
What you wish to do is probably do-able but will require close & consistent attention, and sample boards. And whether the tone will satisfy a third party who is looking for a gold look is hard to predict :-)
Luck & Regards,
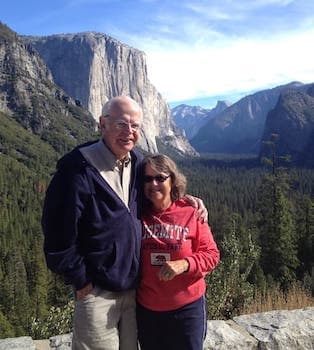
Ted Mooney, P.E. RET
Striving to live Aloha
finishing.com - Pine Beach, New Jersey
June 2021
June 28, 2021
Q. Thank you Ted for your concise answer.
This project has put me in a bad situation.
Gold shades one of the anodizing company gave is not acceptable by the client, it was quitte dullish.
Another company had the right shade but they want very large quantity.
I talked to a PVD coating company they said they can do only in stainless steel. Stainless steel adds quite a bit of weight to the part; also local fabricating shop can't engrave on it.
From finishing.com itself I have learned gold plating is an option, but my experience with gold plated ornaments is too bad it fades off easily.
Is there any other methods which will give good fade and scratch resistance?
Also what is the process used on mobile phones for creating high gloss scratch resistance finishes?
Spray Painter - Hubli, Karnataka, India
A. Hi again Anurag. I don't know the cost sensitivity of your project, but the ideal answer is nickel plating, followed by gold plating, followed by clear coating. It obviously would look the most like gold because it is, and with the nickel underlayer it will be shiny and will not fade :-)
I think anodizing plus gold-tone dye will be aesthetically more consistent than chem-filming because the purpose of dye is to impart a specific color, whereas the purpose of chem-filming is corrosion-resistance, and a truly consistent color is not part of the usual intent or requirement. And, yes, smart phones are often anodized.
But anodizing will not impart shine; the best that you can hope for is that it not detract much from shine. Buff a part to a good shine and then anodize and dye it ... but while I can offer some technical suggestions, I cannot help with logistics half a world away of shops that want higher volume than you have, shops which have one shade of yellow dye when you need another, etc.
Luck & Regards,
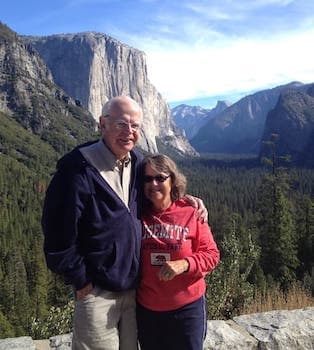
Ted Mooney, P.E. RET
Striving to live Aloha
finishing.com - Pine Beach, New Jersey
June 2021
⇩ Related postings, oldest first ⇩
Q. Does "Yellow" and "Gold " Alodine mean the same thing?
Juline Rodriguezelectronics - Lathrop, California
2006
![]() |
A. First, Alodine is a registered trade name and should not be used in a generic manner. Chem film is a more appropriate name. Chromate conversion coating is not a good name for aluminum either as most consider that to be for plated material. - Navarre, Florida 2006 A. Yes :-) Bill GraysonMetal Finishing - San Jose, California 2006 A. Yes, but neither one means nearly as much as you'd think it does.
"Alodine" is a brand name of conversion coating chemicals - any number of which result in a yellow/gold-ish coloring. However, there are also competitors whose products do the same, and most people in the industry consider the following terms to be virtually synonymous:
Iridite / Alodine / chem-film... Compton, California, USA 2006 |
Q. So if a engineer calls out GOLD Alodine on the print without the MIL-C-5541 standards, then the color is the same as requesting "yellow" on the print correct?
J in Calif
Juline Rodriguez [returning]- Modesto, California
2007
? Juline, can you please tell us your own actual situation so you can get more meaningful answers? Thanks! Your 9-word abstract question resulted in 3 skilled practitioners trying to answer your question, only to have you essentially repeat it, with us still not even knowing whether you are the supplier or the buyer, and thus being able to advise how to proceed.
A. If you are the supplier and provided a finish that the buyer now says is "too yellow", you are probably in a defensible position; the terms 'gold' and 'yellow' are more or less interchangeable. But if the brand name was specified and you did not use the proper product, or if the buyer provided color chips you didn't match, we're back to your company being in the wrong again (if it was your company that provided the coating service). If you are the buyer, and you implement a color chip system in your P.O., the supplier must comply; if not, they have a lot of latitude in color. But buyers generally should not issue such a loose requirement as 'Gold Alodine' with no spec number.
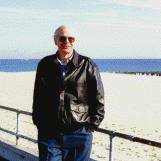
Ted Mooney, P.E.
Striving to live Aloha
finishing.com - Pine Beach, New Jersey
2007
Q. What is the difference between gold Alodine and yellow chromating? Both of them call out the same spec with Mil-C-5541. Are these 2 processes same type finishing but called out with a different name?
Tan Teng Cheang- Penang, Malaysia
2007
Q. What is the difference between Mil-C-5541 and DTL-5541 both class 3
William Stamm- Medford, New Jersey
2007
A. I know part of the answer, William. DTL is an abbreviation for "detail" and is meant to indicate that this is a detail spec (telling you how to process parts) as opposed to a PRF (performance) spec. I believe we went from MIL-C-5541 rev. E to MIL-DTL-5541 F.
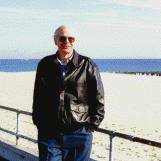
Ted Mooney, P.E.
Striving to live Aloha
finishing.com - Pine Beach, New Jersey
2007
A. For those who still are wondering the difference between MIL-C-5541 and MIL-DTL-5541 I found a link that may help. It answered my questions.
www.engineeringtalk.com/news/mzv/mzv109.html
- Mukwonago, Wisconsin
2007
----
Ed. note, June 2021: Sorry, readers, that link has broken. Please try to include an article's title or author rather than a bare link so we can find things again and update links when possible. Finishing.com has been 'on the air' for 33 years, and 99% of links work for less than a tenth that long :-)
A. The military started changing specifications from the old MIL-C-5541 type nomenclature to either DTL (Detail) or PRF (Performance) specs. The move will eventually eliminate military specs all together as industry specification come up to speed. DTL specs provide exact instructions and requirements. PRF specs give a performance minimum and let the vendor/supplier/user figure out how to get there, e.g. paint must be blue and provide 5000 hrs salt fog protection. MIL-DTL-5541F (revision F) is the latest military spec for chromate conversion coatings on aluminum replacing MIL-C-5541E. The spec is free for download - search for "Assist Quick Search" to get the government site. (Actually it's not "Free". Taxpayers already paid the DoD to develop and maintain it!) Unless you need electrical conductivity through the coating, use class 1a which is thicker than class 3 . The yellow or gold color is caused by the Type I hexavalent chromate which is yellow. The thicker the coating, the more chromate the more yellow the coating. Thin coatings may seem more gold over aluminum - same stuff. Thicker the coating, better the corrosion protection. If you want more corrosion protection, paint it too. MIL-DTL-5541 is a good base for primer and paint. If you want to powder coat, probably should use class 3 to get good adhesion of the powder to the part.
Allan LangMaterials Engineer - Ft. Walton Beach, Florida
June 23, 2008
Q. What is the difference gold and clear Chem Film (Mil-C-5541), Do the different colors serve a different purpose.
Shawn Reilly- Valencia, California
2007
A. Hi, Shawn. The gold or yellow color is the inherent color of hexavalent chromium so, traditionally, the yellow color implied more chrome and more corrosion protection. In these days of RoHS, most chromate conversion coating is actually trivalent, and any yellow color is just dye.
Regards,
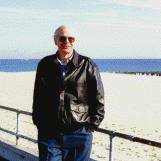
Ted Mooney, P.E.
Striving to live Aloha
finishing.com - Pine Beach, New Jersey
April 18, 2011
Q. What would cause / give Alodine a blue tint as it dries?
Thomas BlackA&P Mechanic - Clearwater, Florida
December 29, 2008
A. Hi, Thomas. Some of the Alodines are supposed to be blue. Are you unsuccessfully trying to get a blue, or are you unsuccessfully trying to hold a clear or yellow or black color? Which Alodine are you using? Are you working with aluminum or with zinc plating?
Regards,
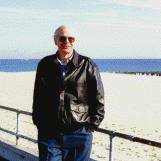
Ted Mooney, P.E.
Striving to live Aloha
finishing.com - Pine Beach, New Jersey
December 29, 2008
Q. When using the MIL-DTL-5541F is there a Type and Class as in Anodizing?
thanks
- Huntsville, Alabama
February 19, 2009
A. Yes, James. MIL-DTL-5541 [⇦ this spec on DLA] is free, and is a short & rather readable spec, so get a copy!
Regards,
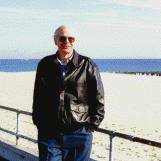
Ted Mooney, P.E.
Striving to live Aloha
finishing.com - Pine Beach, New Jersey
February 2009
Q. We've 'inherited' several drawings from a company that went out of business. They call for Gold Chromate per Mil-C1-5544.
Everybody here has always assumed Yellow and Gold were the same thing, interchangeable terms, but so far, through research, I can't substantiate that fact. Can you help?
Quality Tech - Warwick, Rhode Island, USA
April 14, 2011
A. Hi Brad. That spec number looks pretty fractured, but double check if it isn't Mil-C-5541. There is no chemical distinction between "gold" and "yellow", so now you're down to appearance. The buyer certainly can "extend" the spec, adding additional requirements if they wish; but when it comes to appearance and subtle differences (if any) in color, sample boards /color chips (as briefly mentioned in section 6.8 of Mil-DTL-5541) would presumably become their obligation: "These are examples of acceptable 'gold' color / These are examples of unacceptable 'yellow' color". Good luck.
Regards,
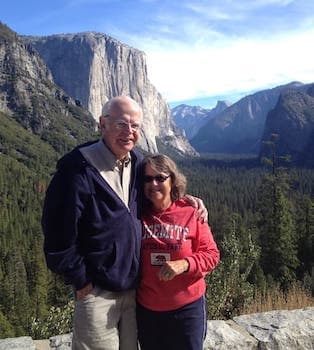
Ted Mooney, P.E. RET
Striving to live Aloha
finishing.com - Pine Beach, New Jersey
Color variations in Chem film MIL-DTL-5541 class 1A gold
Q. Good day. I would like some advice on the wide range of colors gold chem film can go from. So far I am seeing a really light gold to a dark mustard brown. Are there any outside forces that can change the color of the finish? Is chemfilm a cosmetic finish? I keep telling my supervisor we cannot reject parts with the proper Certification of plating. Yet they want to return to vendor due to color variations from light to dark.
James Dee- Fremont California
February 20, 2018
A. Hello James. See section 6.8 of MIL-DTL-5541. It implies that you are correct that such variations are acceptable. But it also says that you as buyer can establish a color chip system if you wish -- which of course is actually obvious; a customer can buy or not buy whatever they want. But if you do establish a sample board (which many professionals pooh-pooh) you presumably will have to pay more because your supplier will be rejecting parts internally, and they will probably want to negotiate what to do with rejected parts. Best of luck.
Regards,
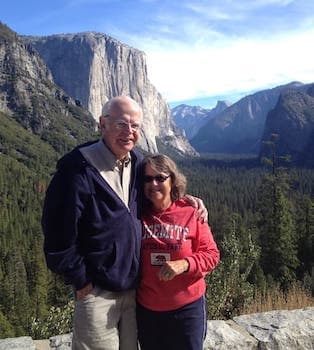
Ted Mooney, P.E. RET
Striving to live Aloha
finishing.com - Pine Beach, New Jersey
February 2018
A. Although Chem Film can be extraordinarily beautiful on some substrates, it is not intended to be cosmetic, as outlined in the spec that Ted referenced. To certify, the spec requires that it pass certain tests (salt fog, electrical resistivity, adhesion). A uniform, pleasing appearance is not among them.
I can speak from the Vendor's side here, having gone through explaining this to customers in the past. If the customer PO requests parts certified to the spec, and the parts conform to the spec, the PO has been fulfilled. Any aesthetic requirements need to be spelled out clearly in the original RFQ because, as Ted points out, many FUNCTIONAL coaters will balk at the requirement.
Variables impacting color include, but are not limited to; bath pH vs. bath concentration, bath temperature, vigor of bath mixing (how fast does solution flow across the part- part geometry also comes into play here), substrate finish, and both temperature of, and immersion time in, the rinse after processing.
I think the question a customer should ask himself in advance when considering adding an aesthetic requirement to the RFQ is, "How much are we willing to pay for PRETTY?" In many cases, Chem Film is being applied as an adhesion enhancer and protective pre-coating for a later paint application, and if it works... well, it works. :)
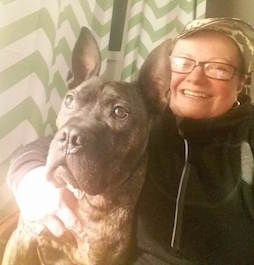
Rachel Mackintosh
lab rat - Greenfield, Vermont
February 21, 2018
April 25, 2018
Q. I have been asked how to reconcile or show consistency with the MIL-DTL-5541F and ASTM B449 -93 specifications for color associated with Class of the chromate through the use of any Type 1 Chromate product.
Can you shed any light on this question? Thank You for any help in answering this question.
MIL-DTL-5541 [⇦ this spec on DLA]
a. When several alloys are processed with the same conversion chemical, color may vary from alloy to alloy.
b. Due to the high level of impurities and oxidation on the surfaces of aluminum welds and castings, color may not be as uniform as that obtained by treating wrought alloys.
c. Dark spots may result from dripping or rundown of the conversion chemicals when the parts are lifted out of the treatment tank. A small amount of spotting does not result in coating degradation but must be minimized by quickly rinsing the parts after treatment, and use of proper racking techniques.
Visual examination does not reveal if the protective value of the coating has been impaired by contamination or by overheating during drying. If a clear coating is required, inspection difficulties may arise because visual inspection does not reveal the presence of a coating. For type I materials, existence of a coating can be verified by using a simple spot test specified in ASTM B449. For type II materials, existence of a coating should be verified per the manufacturer's recommendation.
Table from Page 2 of ASTM B449 (2010)
Class A Appearance,
Coating Mass per Unit Area, g/m2
Corrosion Protection
Class 1
yellow to brown, 0.4 to 2 maximum corrosion resistance generally used as final finish
Class 2
colorless to yellow, 0.1 to 0.4
moderate corrosion resistance, used as a paint base and for bonding to rubber
Class 3
colorless,<0.1
decorative, slight corrosion resistance, low electrical contact resistance
Class 4
light green to green, 0.2 to 5
moderate corrosion resistance, used as a paint base and for bonding to rubber
No relationship exists between class numbers and degree of corrosion resistance. Class numbers have been assigned on the basis of traditional usage and for compatibility with national standards.
Kurt Krueger
- Lexington, Massachusetts
Q, A, or Comment on THIS thread -or- Start a NEW Thread