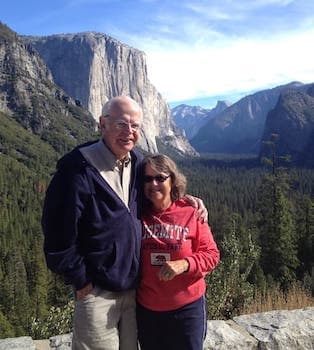
Curated with aloha by
Ted Mooney, P.E. RET
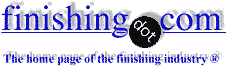
The authoritative public forum
for Metal Finishing 1989-2025
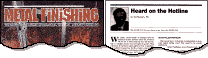
-----
Anodising problems
I am working in anodising plant as supervisor.plant located at Chennai. we are using a 20% sulfuric acid at 20deg for anodising . we are having an Al alloy 5%Cu,12%Si. We are facing a problem in finish. FInished material having greenish in some area. I feel that cu is also oxidised. I thought alloy was etched during process. Another one is roughness. which is best method const current or voltage.
M.Ramasami- Chennai, INDIA
2006
What casting & cleaning processes?
This alloy (a bit more alloyed than 384) isn't expected to give a good anodized appearance. Avoid caustic etching -- use only as necessary to hide scratches, etc. Caustic preferentially attacks the aluminum, increasing the surface Si & Cu content. Use a fluoride-containing deox/desmut.
Constant anodizing current is preferable.
I've heard that burnishing can homogenize the surface to enable a good anodize appearance. Anyone know more about this?
- Goleta, California

Rest in peace, Ken. Thank you for your hard work which the finishing world, and we at finishing.com, continue to benefit from.
2006
Q, A, or Comment on THIS thread -or- Start a NEW Thread