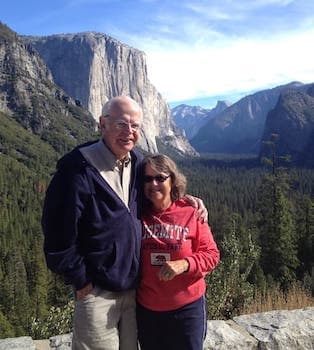
Curated with aloha by
Ted Mooney, P.E. RET
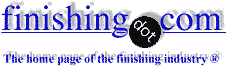
The authoritative public forum
for Metal Finishing 1989-2025
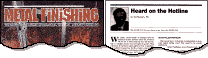
-----
Anodize ASTM B580 Inspection for defects under 500-600X magnification
Material is 6061-T6.The customer is rejecting parts that show signs of pitting, cracks, and non-bonded regions of the anodize coating. The part is machined to a 16 surface finish and then tumbled for burr removal prior to plating. Is the use of high magnification (500-600X )appropriate for plating evaluation?
Paul WalshContract Manufacturing - Topsfield, Massachusetts
2006
2006
A. Anodizing, like etching & electropolishing, reveals defects smeared over by mechanical finishing. If the customer is willing to pay for quality parts for a critical application, the requirement is achievable for a 6000 series alloy in T6 condition. Pre-anodizing inspection (after any etching and deox/desmut) may be useful in identifying material & machining problems.
Of course, crazing of hard anodizing may require negotiation and/or modified procedures. Use an additive that allows higher anodizing temperature, and avoid hot water rinses!
- Goleta, California

Rest in peace, Ken. Thank you for your hard work which the finishing world, and we at finishing.com, continue to benefit from.
Q. Could tumbling for burr removal work harden the surface leading to pitting, cracks, and what appears to be non-bonding of the anodize when viewed at 500-600X mag?
Paul Walsh [returning]Contract Manufacturing - Topsfield, Massachusetts
2006
A. I personally hated tumbled parts because the manufacturer of those parts rarely rinsed properly, resulting in adherent material that was very very difficult to remove.
James Watts- Navarre, Florida
2006
2006
A. Paul, the problems are due to foreign material (e.g., lubricant, burnt or dirty surfaces of folded over burs, abrasive fines) embedded into the aluminum. Anodizing can act as QC in revealing these defects (see DEF STAN 03-24 (3) Chromic Acid Anodising).
Do a systematic examination after machining, cleaning, and tumbling steps. Examine parts both with and w/o etching. Liquid penetrant inspection may help, especially after a little etching to remove smearing.
Possible remedy: Machine to a lower Ra, degrease, then lightly etch. This removes contamination and weaken burs prior to tumbling. Avoid alumina or silica tumbling media, as fines of these materials easily embed into aluminum. A light, post-tumbling etch should also help.
Work hardening shouldn't be a problem except perhaps secondarily, by causing high residual stress in folded-over burs.
- Goleta, California

Rest in peace, Ken. Thank you for your hard work which the finishing world, and we at finishing.com, continue to benefit from.
A. Paul
In response to your initial post, do the parts that exhibit the pitting, cracks, and non-bonded regions of anodize pass performance or process control testing, i.e. salt spray?
- Colorado Springs, Colorado
2007
Q. Parts conformed ASTM B117 336 Hour salt spray testing.
Paul Walsh- Topsfield, Massachusetts
2007
A. Paul
I do not have the ASTM B580 spec but I would think that if the anodize truly had pits, cracks and areas of non-bonded anodize, your coupons would not pass the SS test. Unless the specification or your PO/contract specifies to inspect at that level, I would think your parts should be acceptable.
Bottom line- do your parts meet the criteria specified by the PO/contract?
- Colorado Springs, Colorado
2007
Q. Willie:
Yes the part's meet all stated purchase order requirements. Thank you for asking the question "did the parts past salt spray testing?" Unfortunately, the customer still wants the parts remade. I guess this comes under, the customer is always right clause. We are going to eliminate the tumbling operation to improve the appearance of the plating.
Thank you,
- Topsfield, Massachusetts
2007
A. Paul,
It would have to be a very, very good customer to remake the parts or even rework the parts IF they met the contract language.
Examination at 500 X is virtually unheard of and should have been reflected in the PO since ist is so grossly unusual. 40 X is the max that I have ever heard of with 3X check the most common if any X was used.
- Navarre, Florida
2007
Q, A, or Comment on THIS thread -or- Start a NEW Thread