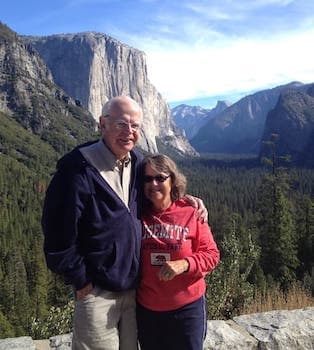
Curated with aloha by
Ted Mooney, P.E. RET
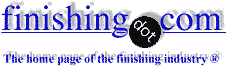
The authoritative public forum
for Metal Finishing 1989-2025
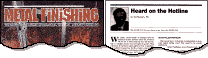
-----
Bare spots on hot tin dip product
Currently I am having problems with bare copper showing after the hot tin dip process. What can I do or look at to ensure I am getting proper coating of the bare copper wire?
Jim Zellmannwire mfgr. - Turners Falls, Massachusetts
2006
I think it's more likely a defect in the preparation (cleaning, descaling, fluxing) than in the hot dip process itself. Manually running a snippet through hot dipping, then fluxing and hot dipping, then cleaning, fluxing, and hot dipping may narrow the area where the problem is occurring.
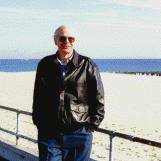
Ted Mooney, P.E.
Striving to live Aloha
finishing.com - Pine Beach, New Jersey
2006
It sounds to me like your problem is either the cleanliness of the copper wire before it goes into the molten tin, or the copper has inclusions in it. Make sure the copper surface is clean of waxes and oils and that there are no impurities in the wire that can cause inclusions.
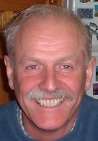
Trevor Crichton
R&D practical scientist
Chesham, Bucks, UK
2006
2006
Dear Jim,
I am just now studying hot dip tin fluxes. I have a client that had many rejects. His base metal is cast iron and his flux is badly contaminated with iron (Fe+2). Also his pH of the flux is too high. In his process he uses caustic to remove soaps and oils and then HCl to pickle. Both of these tanks are too weak because of his wrong titration methods. This client changed out his flux (ironically to a standard (zinc) galvanizing flux) and all his bare spots went away instantly. If we knew more about your process then more comments could be possible.
Galvanizing Consultant - Hot Springs, South Dakota, USA
I want to coat a galvanized steel sheet component 300 mm X 300 mm X 1 mm thick by hot dip tin process.
How do I do the pre treatment the galvanized sheet. Also is any flux available that can used before dipping the sheet in tin.
Pl. helps me out in this matter.
Thanks
Sagar.
- Mumbai, India
April 23, 2010
April 23, 2010
Hi, Sagar. To be clear here, you are trying to make a steel sheet that will have a layer of hot-dipped zinc, followed by a subsequent layer of hot-dipped tin?
Regards,
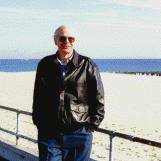
Ted Mooney, P.E.
Striving to live Aloha
finishing.com - Pine Beach, New Jersey
September 7, 2010
I also do have tiny spots (points) on a flat copper wire.
I first go through a galvanic cleaning and rinsing process, then I apply flux (hydrobromic acid), blow it off and pass through a tin bath (temp. 450«F, 60/40 tin lead alloy). After the air wipers the tinned copper wire is cooled.
When I speak of spots I do not speak of the structure which is built (comparable to broken glass) but of tiny holes.
Should I try with another flux?
Wire industry - Altendorf, Bayern, Germany
Q, A, or Comment on THIS thread -or- Start a NEW Thread