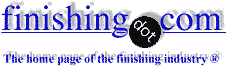
-----
Trouble in plating a penny with nickel by using a cupronickel alloy
Hi, my name is Jayson Miller and I'm performing electroplating for a high school experiment (I am a Junior). I was thinking of trying to use a cupronickel alloy (75%Cu 25%Ni via nickel coin because I can't get pure Nickel) to plate a penny with after extracting the nickel, but I'm not quite sure how to extract the nickel from the alloy. I thought about heating the nickel to 1373K or so to melt the copper and letting the liquid copper sink to the bottom of the crucible it would be melted in, but the extraction of the nickel is the problem with that scenario. I have 3 molar HCl (maximum concentration I can use besides 18 mol HCl since my Chemistry teacher won't mix any 4 or 5 mol HCl) and 3mol H2SO4 at my disposal. I'm just wondering, what's a good way to take advantage of the solubility and electronegativity of Cu and Ni to plate a penny with Ni instead of Cu? Would dissolving the nickel and heating the acid leave NiCl2 and Cu or CuCl2 and Ni? Any help would be greatly appreciated.
Jayson Mstudent - Lenoir, North Carolina
2006
2006
Hi Jayson,
Good news/bad news:
It's possible to do an electrolytic separation by first plating out the copper at a lower voltage (2-3 V) than that at which nickel plates. Nickel platers do so routinely to minimize copper impurity content of their plating solutions.
However, as pointed out in letter #43238, it's very unlikely that a high school will have the expensive equipment necessary to do a proper job. If you can't get pure nickel (too expensive?), try pricing platinum electrodes, a proper power supply, good pH meter, fume hood, magnetic stirrer/hotplate, etc. Also, it's a bit difficult to dissolve Cu-Ni alloys. Analysts use a solution of sulfuric and nitric acids to dissolve the metal, after which remaining nitric is evaporated off by heating.
Wait until about 3rd semester of college chemistry for an opportunity to quantitatively analyze a copper alloy.
The other separation methods proposed have some drawbacks:
Melting won't separate the alloy: Check the Cu-Ni phase diagram. Cu & Ni form continuous solutions in both solid and liquid. Zone refining could be used, as the solid is slightly richer in nickel than is the liquid. But first, fuse together a 2-meter stack of coins into rod form. Then slowly pass through an induction heating coil, repeat about 200 times, and the copper at the initial end should be decreased from 750,000 down to 25 parts per million. Also, use an inert gas atmosphere. Maybe spend $250K to produce $100 worth of pure nickel?!?
One could bubble an argon + 1 ppm oxygen mixture through the molten alloy to selectively oxidize the nickel. The NiO formed is about 25% less dense than the metal, so should be able to skim off the surface. A bit dangerous.
Re NiCl2: Dissolving the coin in hydrochloric acid & evaporating will produce CuCl, CuCl2 and NiCl2. Better to grind the coin to powder (much easier said than done!), react with a limited quantity of dilute HCl, filter out the copper residue and then crystallize the NiCl2 from the liquid. But, only about 96% pure (estimated from the Gibbs free energy of -19.2 kJ/mole at 25 C for the reaction 2 CuCl + Ni = 2 Cu + NiCl2).
For reference: Electrolytic separations are possible since more noble metals can be plated out at lower voltage than the less noble ones; e.g., Cu can be plated from a solution containing Co, Fe, Ni, Pb, Zn. Vogel's
Quantitative Inorganic Analysis
[on
Amazon affil links],
4th Edn., ISBN 0-582-46321-1, Chapter XII Electro-Gravimetry gives a procedure for the analysis of coinage metals and Monel metal.
Quantitative Chemical Analysis
⇦[this on
Amazon affil links],
4th Edn., I. M. Kolthoff et al. (1969), Chapter 64 Analysis of Brass, is also useful.
G. H. Ayres'
Quantitative Chemical Analysis
⇦[this on
Amazon affil links],
2nd Edn., p. 652-654, gives rather more 'cookbook' instructions.
- Goleta, California

Rest in peace, Ken. Thank you for your hard work which the finishing world, and we at finishing.com, continue to benefit from.
Ask Ted for my email address and contact me directly. I very probably can help you out with a small chunk of rolled depolarized nickel anode material (used). This offer is valid for Jayson only!.
James Watts- Navarre, Florida
2006
Your email address was sent to Jayson. Thanks. Jim.
If I were Jayson, I would try to contact a local metal finishing company and request some free nickel anodes. I am sure anyone with a heart will give out some free nickel anodes to a studious guy like Jayson...I am really glad to see his zeal in his project.
thanks to Ken for enlightening us further.
thanks to James Watts for supporting a student.
Hemant
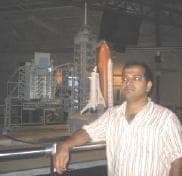
Hemant Kumar
- Florida, USA
2007
Jayson,
Is there a reason that you need to do nickel plating on a penny? Copper plating on a quarter or a brass key is easier, and copper is readily available (electrical wire is very pure copper). Are you trying to achieve something in particular, as opposed to simply demonstrating electroplating?
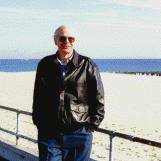
Ted Mooney, P.E.
Striving to live Aloha
finishing.com - Pine Beach, New Jersey
Q. I'm teaching an upper division inorganic laboratory.
I'd like to make nickel and copper sulphate s and ammonium sulphates, and see if we could separate them by solubility or crystallization.
Any suggestions?
- Flagstaff, Arizona
January 15, 2009
Q, A, or Comment on THIS thread -or- Start a NEW Thread