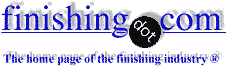
-----
Roughness in Nickel Deposit
Q. Hi I'm jahid from India.
Particles in nickel plated white metal object again & again -- what is the solution
And also can anyone give me an electroplating problems and solutions book?
- Rajkot, Gujarat, India
January 16, 2022
(affil links)
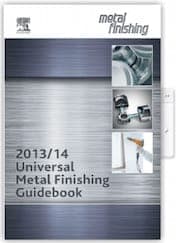
free pdf is currently available from academia.edu
A. Hi Jahid. The Metal finishing Guidebook can be downloaded for free, but I think the best "Problems & Solutions" troubleshooting lists are in The Canning Handbook [on eBay, Amazon, AbeBooks affil links].
Unfortunately, asking why you have particles is a bit like asking a doctor why you have a temperature. There are lots of potential causes from undissolved boric acid, to lack of proper filtration & anode bags, to excessive current density, and probably several others.
Please send good, well-focused photos of the problem, tell us where on the parts and under what conditions you see them, and give us some of your operating parameters. Thanks!
Luck & Regards,
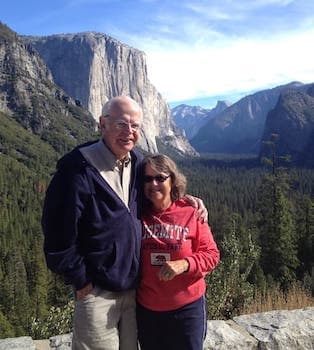
Ted Mooney, P.E. RET
Striving to live Aloha
finishing.com - Pine Beach, New Jersey
January 2022
⇩ Related postings, oldest first ⇩
Q. I am facing roughness problem in my Nickel plant. I plate motorcycle rims in Karachi. A fine brown colored powder is formed in bath that cause roughness on the horizontal surface of the object. Filter unit remove a lot of sludge at the end of day. I believe that sludge is always formed for which filtration is necessary but in my case the formation is high. Please suggest what to do. Please also note that same brighteners are being used at other two places without any problem.
Farhan ShahidElectroplating line - Karachi, Pakistan
2006
A. A brown sludge or precipitate is not normal in Ni electroplating solutions. What kind of water are you adding to the tank? When was the last time an analysis was done to check for metallic contaminants such as Fe or Cu? What is the chloride level? Is it possible someone added something they shouldn't have to the tank? If the bath is that trashed, drum it up, clean the tank and anodes up, and make up a new bath!
Mark BakerProcess Engineer - Syracuse, New York
2006
Q. Dear Mark,
Thanks for your response.
We are adding tap water (from Tube well. Iron content remain around 15-20 mg/liter. However, we give a high PH treatment along with active carbon treatment every three months. The chloride content is around 18g/liter. We are adding HF once in a week to adjust the PH of the tank on the assumption that tap water may have calcium as the impurity. This treatment also did not work.
Please see the matter and let me have your suggestions.
Thanks and regards,
- Lahore, Pakistan
2006
First of two simultaneous responses --
A. Farhan, some basic rules in electroplating are needed here. Firstly, only use pure water - either distilled, reverse osmosis or deionised, never use tap water; if you do, you will be adding unknown contaminations to a process that fundamentally needs careful control and purities. Secondly, ensure your solutions are filtered and free of any unwanted particles as they will co-deposit and cause a rough plated surface - sound familiar? Thirdly, cleanliness is essential in good plating practices, if you cut back on these basics you will only produce rubbish, wasting your time and money as well as wasting a lot of natural products.
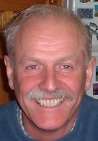
Trevor Crichton
R&D practical scientist
Chesham, Bucks, UK
2006
Second of two simultaneous responses --
A. Farhan,
I suspect your water source. De-ionized water should be added to the tank. The iron concentration in your tap water seems way to high, especially to add to a nickel plating tank. The ph in nickel sulphate baths is controlled using dilute sulfuric to decrease the ph. To raise the ph a slurry of instant nickel carbonate should be used. I've never heard of HF used for ph adjustment in nickel. It sounds like your nickel plating solution supplier needs to spend some time at your plant. Good Luck!
Process Engineer - Syracuse, New York
2006
A. Farhan
It's most likely copper, ask your supplier for the proper treatment.
plating - Windsor, Ontario, Canada
2007
Q. I have repeated roughness and pitting issues in our watts nickel bath at my work. It seems anything that has a larger surface area tends to be rough and pitted only on the top side of the parts and the areas facing the anodes. Anode bags are black from the last carbon treat and nickel chips are rather black and smutty a couple feet down in the baskets,but through the last carbon sample of the bath was taken only one grain of carbon was found the filter sample.
Derek Johnson- Brooklyn Park, Minnesota, United States
May 22, 2008
December 30, 2011
Q. Hello. I'm facing since one year a roughness problem in my 2 bright nickel tanks (volume = 100 L). I'm plating nickel on brass items (surface item = 0,1 dm2, surface rack = 20 dm2). Problem is I find roughness on certain items : for a 200 pieces rack, about 10 pieces have roughness, and by roughness I mean just 1 pick per piece randomly localised on the surface of the piece.
I tried many solutions, without success :
- anodes are double bagged
- bath is on continuous filtration over a 5 microns filter
- activated carbon treatment
- impurities analysis
Operating conditions are :
- NiSO4 = 300 g/L
- NiCl2 = 70 g/L
- H3BO3 = 50 g/L
- pH = 4,2
- T = 60
- DDC = 3 A/dm2
I read an article that explain that in bright nickel baths, chlorine generated at an auxiliary anode that is close to the cathode can react with organic additives to form an insoluble material that is incorporated in the deposit. Can it be the source of my problem ?
Please help me to find solution to that problem.
Best regards.
Plating shop employee - France
A. What is the calcium (impurity) concentration? If present, raise temperature and filter.
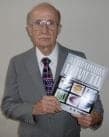
Robert H Probert
Robert H Probert Technical Services

Garner, North Carolina
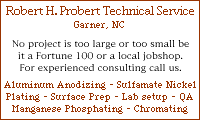
First of three simultaneous responses -- January 5, 2012
A. For Farhan in Karachi
Looks like too much iron, the source? id do not know but, I use to had this problem here, and we do not know exactly the source of it.
1) Using tap water which is too "hard" react with sulfuric acid and forms this sludge I do not know the name of the compound in English, please help.
2) Iron content too high source unknown.
But the main reason for this is that when you add to acid to adjust the pH if there is no good mixing, there is a stratification that means that the bath has a pH level with a value desired in the top but at the bottom the pH is too high.
So at pH higher than 5.2 the iron precipitates forming a sludge, also the same seems to happen with the other compound (I am not completely sure of this).
But what I am sure is that in my case this problem was solved mixing well the acid in to the bath, when added, it also explains why some have the problem and why others don't using the same water.
I have to say that is an possible solution for you, maybe it does not apply to you but if you try you will not lose anything and probably will solve your problem.
For Francois
It is not shelf roughness?
Are anode bag above level of solution?
Is roughness instead of pitting? (Is your part highly buffed before plating? or is a leaded brass? (ask Mr Trevor about that he explained me a lot on this subject))
Try usually suggestions of books (calcium, Iron, etc.) before going more complex (try to keep it simple if you can).
- Bucaramanga, Santander, Colombia
A. WHEN CHLORIDES ARE PRESENT IN THE BATH,THE MOST SUITABLE ANODE MATERIAL ARE CARBON OR PLATINUM.
CALCIUM ABOVE .5 G/L GIVES ROUGHNESS.USE PURIFIED WATER (DM WATER)
IRON ALSO PRODUCES ROUGHNESS.ADD 1-2 ML/L H2O2(30%)
MAINTAIN SOLUTION LEVEL BELOW TOPS OF ANODE BAGS.
DUST/POLISH (FILTER AIR).
USE GOOD QUALITY ANODE BAGS.
IMPROVE FILTRATION.
ALUMINIUM AND SILICONS ALSO GIVES FINE ROUGHNESS.CAN BE REDUCED BY HIGH PH TREATMENT ALONG WITH IRON ETC.,.
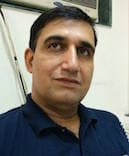
Ajay Raina
Ludhiana, Punjab, India
A. @ Robert H Probert :
I will proceed to new analysis of the baths on monday to check the calcium concentration. I will tell you the concentration as soon as I have the results. But note that I add only reverse osmosis water to the baths (conductivity ~ 0,5 µcm)
@ Daniel Hernandez :
Anodes are double bagged and bags are about 10 cm above the level of the solution. There are no salt on the bags. I have 8 anodes per bath and each week one anode is checked and changed if necessary.
Items are highly buffed before plating and made of leaded brass. What is the correct way to plate these items ?
@ Ajay Raina :
I didn't know that we can use carbon or platinum anodes in nickel bath. I always read that we have to use nickel anodes.
I will check on monday the iron concentration and will give you the results.
Another point : racks are made with steel hooks and brass items are hanged to this hooks. Before we go in the nickel bath, hooks are not plated so we plate directly nickel on these steel hooks with brass items. Can it be the source of the problem ?
Thanks for all your answers.
Best regards.
Francois Pignon
- France
A. I KNOW IN NICKEL PLATING WE USE ONLY NICKEL METAL, AND INCO BRAND IS GOOD AND WIDELY USED.
WHAT I HAVE WRITTEN IS FOR INSOLUBLE ANODES.
THANKS.
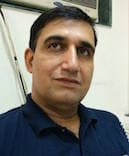
Ajay Raina
Ludhiana, Punjab, India
January 12, 2012
A. If your cathode CD for the components is low and the components are intricate in shape, by the time the surface is fully covered with nickel, some of the material might get dissolved which could give rise to roughness.
Kishore Phadnis- Mumbai, Maha, India
January 13, 2012
A. Remember the plater's rule! Don't panic!!!
Obey the letter of the law
Walk the line
Keep a record
Well, are you sure is roughness instead of pitting?
Roughness arises from insoluble particles as probably you already know.
The source can vary a lot, calcium, bath cold and boric acid become insoluble, iron, nickel particles coming from the baskets, bad cleaning, etc.
Pitting means a different source, which includes bad cleaning, organic contamination, oil contamination, etc.
If leaded it requires an activation process using fluorine ions which can be found using some HF acid which can help; but that is a nasty acid; also there is fluoboric acid which can help, and there is a salt which has fluorine that have common use on plating, but I don't have the name of the compound so I better not say anything about that for now.
Some suggest acetic acid
⇦ on
eBay
or
Amazon [affil links] to activate lead. I tried it with unknown result because it plated perfect but I used other acids at the same time (I was in panic), so I am not sure the effectiveness of it.
In my case I forgot about fluorine and use just hydrochloric and sulfuric acid.
If chlorine is the problem you can use nickel type S to reduce the use of chlorine instead of using insoluble anodes. but I am not sure of the properties of a nickel bath of plain sulphate.
- Bucaramanga, Santander, Colombia
A. Ca va Francois,
may look deeper into the subject of the right material of your hooks. Check them right after the rack with parts get out of the bath.
Regards
- Melbourne, VIC, Australia
January 17, 2012
A. @ Daniel Hernandez : I'm sure it is roughness, not pitting. I checked calcium and iron concentration, both are below 0,1 mg/L so I doubt it can be the source of my problem.
@ Dominik Michalek : I think particles in the bath comes from hooks of the rack due to a bad adhesion of the nickel Watts on the steel hooks. I will try to preplate the hooks with a strike of nickel Woods or KAu(CN)4 acid gold.
Best Regards.
Francois Pignon
- France
A. 50 g/l boric acid is too high. Take into consideration that boric acid has a limited solubility. If it is not completely dissolved it will cause roughness.
As for filtration, it should be with continuous active carbon. The turnover of the bath volume has to be at least 4 times per hour.
I hope that the air pipes are higher than the tank bottom.


Sara Michaeli
Tel-Aviv-Yafo, Israel
Second of two simultaneous responses -- January 18, 2012
A. Firstly, check your pretreatment. You are plating buffed leaded brass. Is your cleaner working effectively. A small particle of compound in your nickel bath can cause roughness.
Also, what acid dip are you using prior to plating? Hydrochloric, sulfuric or sulphate salt acid dips can cause stardusting on leaded brass parts which can also cause roughness in the nickel deposit.
Also, 50 g/L of boric may be a little high, although if you consistently run at 60° it may be just within the acceptable range. Try lowering your boric to 47 or 45 g/L and see if that helps.
- Brisbane, Queensland, Australia
January 26, 2012
A. Regarding Sara's advice, tell us whether the roughness is on a top horizontal shelf or all over. Also check the filter hoses for sucking high pressure air (which is different from your low pressure blower agitation air). Low boric pits on the bottom of the rack, high boric precipitates and settles on flat horizontal surfaces. Are you entering the tank, with the exposed brass and steel while other racks are already in the tank plating - if so, attach a wire and "enter hot".
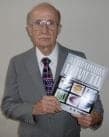
Robert H Probert
Robert H Probert Technical Services

Garner, North Carolina
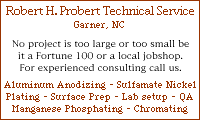
January 27, 2012
A. Francois
I have sometimes the same problem, or looks very similar to mine, well I do not only plate brass but the brass parts I use to plate have mirror look shine and I have to deal with any imperfection on them.
The problem is that these parts require a higher level of "purity " in the solution, in my case the roughness I have is not important on most of the pieces, just in the mirror-like type.
Well just by the time I send an idea of your letter, I start to face a roughness, I spent a lot of time, and of course money (rejects, extra time and etc.) trying to find the reason of it, well finally I put a polypro bag, with water inside with the sludge of the baskets inside and let it on a container to let the water go out of the bag, settle to the other day and, surprise!! There was some material that passed the bag.
I filtered the bath and added 3 layers of a fabric before the bag on each basket and I have no problems until now (one week).
Maybe my bags are not good, you can do the same experiment to check.
Some roughness is fine for some but the same is not for others.
- Bucaramanga, Santander, Colombia
Q. We are getting roughness on the component which we are doing Nickel Chrome Plating (Duplex).
Please suggest the solution as well as if any type of Trouble Shooting chart is available please suggest.
- Aurangabad, Maharashtra, India
June 28, 2012
A. Hi Rajendra.
The Canning Handbook has a very good symptom vs. solution list for nickel plating. Hopefully the thread we appended your question to will give you some food for thought. Otherwise, please supply lots of details and hopefully some pictures, and people may be able to help. Good luck.
Regards,
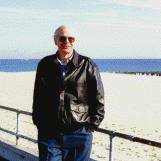
Ted Mooney, P.E.
Striving to live Aloha
finishing.com - Pine Beach, New Jersey
August 29, 2012
A. Filtering a nickel plating solution is a continuous process.
One has to filter the solution ALL the time using carbon and filter aid.
The carbon and filter aid should be replaced once a week.


Sara Michaeli
Tel-Aviv-Yafo, Israel
September 6, 2012
Q. Pitting and roughness in electrolytic nickel plating? I'm plating electrolytic nickel on copper. Need plating thickness of 0.001" or higher. Shall I use high current and less time or low current and more time to avoid pitting and roughness.
Veena Mandlay- Carpinteria, California, USA
March 12, 2013
A. Hi Veena. We appended your inquiry to a thread which will offer food for thought. Current density is very unlikely to be the cause of your problem. I have seen beautiful nickel plating done at 1 ASF and at 40-50 ASF. Good luck.
Regards,
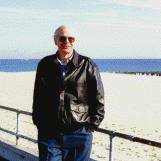
Ted Mooney, P.E.
Striving to live Aloha
finishing.com - Pine Beach, New Jersey
March 13, 2013
A. Hello Veena,
I just wanted to add a few notes that may help you. The Ni anodes should be bagged. You have to have adequate filtration. If the bath is idle for some time dummy plating at low current density is a good idea. Be careful with the use of continuous carbon filtering. Carbon polishing or carbon treatments are only necessary on a periodic basis. Depending on your bath, you could pull out agents of the bath that are vital to good deposits. A chemical analysis of the bath is also vital after carbon polishing / treatment. Your Ni supplier can assist you in adding an anti-pit and / or wetting agents if necessary. Hope this helps.
Process Engineer - Mesa, Arizona, USA
March 16, 2013
Q. We nickel plate thin brass parts (.018 to .040 thick). The material is 260 1/2 hard. We recently changed our process from a manual to automated system. With the change we have not had great success in producing a shiny, smooth finish. The pre-treatment is the same process, and from the tenured operators looks good. The surface of the finished product has a "scratchy look". We are getting good thickness on the finish, but have not got a smooth, normal reflective finish. Any thoughts as to what is causing the loss of quality?
Jim Skankemployee - Titonka, Iowa, USA
March 15, 2019
A. Hi Jim. Step 1, and maybe you've already done it, is to take some solution from the automated plating tank and test it in a Hull Cell
⇦ huh?
. If it's good except in the high current density area, maybe you're burning the nickel in the automated line.
Is this a rack line or barrel line? If it's a barrel line, are the barrels significantly bigger than the ones in the manual line? Bigger barrels can cause abrasion and micro scratching and you may need slower rotation speed or non-conductive media in the barrel. Can you strip a plated part and see what the underlying brass surface looks like.
Some people don't believe in directly nickel plating brass, but feel that a copper interlayer is required. That is addressed in several threads if you search the site.
My knowledge of this topic is mostly book knowledge rather than hands-on, and hopefully someone who actually plates nickel on hard brass will chime in:-)
Regards,
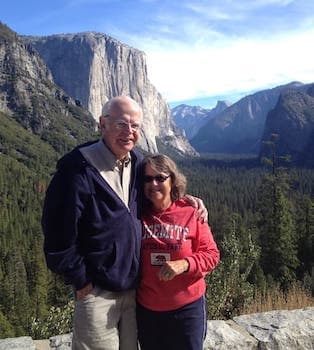
Ted Mooney, P.E. RET
Striving to live Aloha
finishing.com - Pine Beach, New Jersey
March 2019
Q, A, or Comment on THIS thread -or- Start a NEW Thread