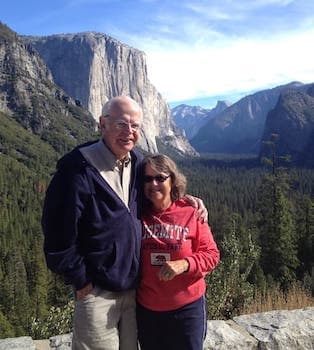
Curated with aloha by
Ted Mooney, P.E. RET
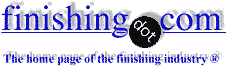
The authoritative public forum
for Metal Finishing 1989-2025
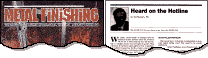
-----
Defects in silver plating: blisters, nodules, and pits
Q. Good day to all.
I am working in a manufacturing industry for cutters. Recently we are required to sub-contract silver plating job to Supplier. I have encountered defects like blistering and nodules (look like pit mark) on the silver plated part. Can anyone please help to explain the root causes of the defect mentioned? What are the ways to prevent the defects?
cutters - Singapore
2006
A. Hello Chua. The short answer is that the plating process is defective (although the plating shop might perhaps validly claim that the material is not suitable for plating). As a customer, though, there is usually only so much you can do to fix the problem, but it starts by simply insisting that the parts are not acceptable if they blister or if they have nodules and pits.
The plating shop presumably has years of experience at this, so realistically you're not going to learn enough from an internet posting to be able to improve their process for them. Your usual option is to tell them they must do better, and then locate another supplier if they don't. But I suppose you could insist that they retain a plating consultant. You could get a few books on electroplating from our "must-have booklist" (if you don't have them already) which probably would help you acquire a deeper understanding of the technical issues causing some of those defects.Good luck.
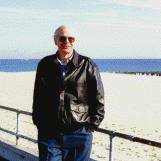
Ted Mooney, P.E.
Striving to live Aloha
finishing.com - Pine Beach, New Jersey
2006
2006
Hi Ted,
Thanks for the reply and pointers.
What you have said is true; it is not possible for a customer to know enough to resolve the problem. I have encountered more problems recently like poor adhesion, peeling off of silver plating, etc.
As a customer, I wish to play my part to support the Supplier in achieving Quality Product. I am even thinking of introducing PMP and FMEA to help Supplier monitor and document processes for improvement.
Q. It has not been easy to locate a good silver plating supplier, especially for our product which requires two different plating areas but with same thickness. Presently rubber masking has been used but leakage occurs. Any good suggestions to prevent leakages? We are supposed to plate two different size internal diameters, with min. plating thickness of 25 micron. Internal diameter have been machined and controlled at tolerance of ±0.012 mm before plating, ±0.017 mm after plating.
Please assist. Thanks.
Regards
cutters - Singapore
A. Hi Chua. As a general rule, plater's tape or stop-off lacquer will provide a more leak-free masking than a rubber seal because they adhere. But I don't know whether those are applicable to your production situation.
Regards,
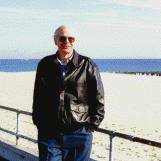
Ted Mooney, P.E.
Striving to live Aloha
finishing.com - Pine Beach, New Jersey
Q. We have observed localized extra deposits of silver on surface of silver plated aluminium casting (9% silicon alloy). We are using cyanide bath (120 - 150 g/l) for silver plating. What could be the cause of defects?!

Hemant Shah
switchgear industry - Vadodara, Gujarat, India
May 11, 2013
A. This defect is usually called "Burning" which is caused by variation in flow of current.You need to set a proper rectifier to minimize current fluctuation.
Rahul Tandel- Vapi,Gujarat, India
February 28, 2015
Porosity in silver plating shows up 3 months after plating
Q. Pores are observed on the silver plated aluminum casting alloy (9% Si). Silver plating defect not observed after heating at 120 °C 1 hour. This is observed after 3 months of silver plating.

Hemant Shah
switchgear industry - Vadodara, Gujarat, India
February 13, 2016
A. Hi Hemant. I'm not sure if you are starting onto a different problem on the same parts here, or clarifying your previous posting, but I would have to agree with Rahul that the previously posted pictures reflect burning (or possibly roughness from unfiltered particles), not porosity.
Assuming this is an additional problem, can you tell us a little about the cleaning, activation, zincating, underplate if any, and silver plating process? Do you do the plating in house?
Regards,
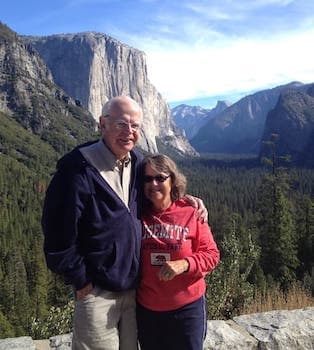
Ted Mooney, P.E. RET
Striving to live Aloha
finishing.com - Pine Beach, New Jersey
February 2016
finishing.com is possible thanks to our supporting advertisers, including:
Q, A, or Comment on THIS thread -or- Start a NEW Thread