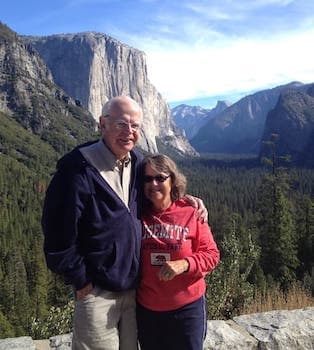
Curated with aloha by
Ted Mooney, P.E. RET
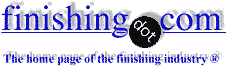
The authoritative public forum
for Metal Finishing 1989-2025
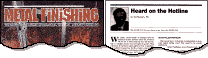
-----
Optimal length of a plating cells in a continuous application
I plate continuous flat stock coils of many widths, gauges, and base materials continuously on about an 80 ft. plating line. Most of my finish requirements are copper as an underplate with tin(matte, bright, alloy) as an overplate. The lines I have were built prior to my arrival, and are very different line to line. Some of the plating cells are 36" in length, while some go up to 70" in length. Nobody can seem to tell me the purpose of this. My understanding, and opinion is that 36" is probably better, as you are keeping the plating closer to the contacts between the plating cells. At 70" how much plating can really be taking place at the middle of these cells so far away from the contacts? As I am in the process of expanding my lines, and modifying them at the same time, any input into this issue will be greatly appreciated.
Michael C. BerrierIndustrial Continuous Plater - Addison, Illinois, United States of America
2006
First of two simultaneous responses --
The material needs to spend a given amount of time in each process tank and each rinse tank (and they are NOT the same times). Since the material has to run at a constant speed, the only way for more time is to have a greater amount of material in the tank which is done by having a longer or deeper tank.
James Watts- Navarre, Florida
2006
Second of two simultaneous responses --
Hi Michael,
The length of a plating cell is predetermined with factors in mind such as surface area to be plated, plating thickness required, current density applied, line speed, and the efficiency of the plating solution. In continuous plating machines I've worked with the cathode contacts are in constant connection with the parts through the entire length of each plating cell. As long as there is sufficient anode area within the cell, you will get plating until the part exits the respective plating cell. A good possible reason for the 70" plating cell is that a customer at one time required higher plating thickness and your company did not want to sacrifice line speed, or the plating solution was not providing the Cu or Sn thickness in the 36" cell. Another reason for the longer cell is that your company may have plated another metal at one time that required the longer cell. If you are going to revamp your lines it would be a good idea to have a plating consultant with a strong background in continuous plating help you, or a reputable supplier that sells both the plating chemistry and the machinery. Good Luck!
Process Engineer - Syracuse, New York
2006
I understand the need for dwell time in the plating cells. My question pertains to whether or not I am losing efficiency toward the middle of the longer plating cells, as the contact is only being made on either side of the plating cells. In other words, is more cells at a shorter length better than fewer cells at a longer length?
Michael Berrier- Addison, Illinois, USA
2006
Well, you are correct that more contacts are better in terms of voltage drop, but this perhaps needs to be balanced against the cost, complexity, and extra maintenance required to provide additional contact points. It is possible to model the current density. For this you would need to know the material so you know it's conductivity, and you would need to know the thickness of the material so that you can estimate the available plating voltage left after the voltage drop due to the resistance. It would be a difficult modeling job but it could be done. What might be more practical would be to use a current density probe at the middle of the strip (I don't know enough about your installation to know the safety and practicality of that, but such devices are available from Industrial Instruments Inc. and others).
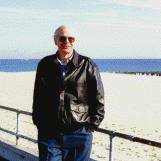
Ted Mooney, P.E.
Striving to live Aloha
finishing.com - Pine Beach, New Jersey
2006
So here is the ultimate question. What would be better, as far as speed and efficiency is concerned? Four (4) 36" cells, with contact points before the first cell, in between each of the cells, and after the last cell, or two (2) 72" cells with contact points before the first cell, in between the two cells, and after the second cell? Or is there no difference at all? Note that the total plating area available in the two options is the same.
Michael Berrier- Addison, Illinois, USA
2006
All things being equal (and they rarely are), multiple 36" cells is a better approach. I worked for a mfgr. of continuous reel-to-reel plating equipment for nearly 6 years, and our general rule of thumb was not to go over 36" unless we absolutely had to, for the same concerns you've already mentioned. We did a little 3D modeling of these plating cells and the results seemed to indicate that longer cells result in less plating at the center of the strip. However, I have no quantitative data to back that up.
Mark Thede- Chandler, Arizona, USA
2006
Thank you all, you have been most helpful, I am now in the process of designing some prototype 36" cells for experimental purposes.
Michael Berrier- Addison, Illinois, USA
2006
Q, A, or Comment on THIS thread -or- Start a NEW Thread