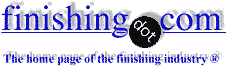
-----
Trying to get a good surface rms finish on the o.d. on a 3 1/4" 6061 aluminum round
Hi, I am getting a great RMS finish on the front of the part, Grooves look like a record. But when trying to get the same on the O.D., not even close, seems to almost look zig zagged. What am I doing wrong? Is there a special carbide insert for this? Like a threading grind? I am getting a chrome look finish, granted, but it picks up fingerprints, the front of the part doesn't. Any suggestions appreciated. Thanks, Dale
DALE SKOWRONSKIENTREPRENUER - SOUTH BEND, IndiaNA, USA
2006
Assuming a proper feed and speed and depth of cut, I will guess that you need to use a steady rest on it.
James Watts- Navarre, Florida
2006
What are the actual RMS requirements? typically the best surface finish you can achieve with 6061 is about 3 to 5 nanometers RA. This would have to be done on a diamond turning machine with air bearing spindles or hydrostatic spindles. If you have some further information it would help
Dwayne Salisbury- McIndoe Falls, Vermont, USA
2006
It is normal to hold a part stiffer when facing to avoid vibration, either with rests closer to the end or directly with the chuck jaws close to the machining surface. When turning lengths it is not so obvious. So, assuming all your machining parameters are the same, I would guess it's a matter of set-up (machine and/or part rigidity).
Guillermo MarrufoMonterrey, NL, Mexico
2006
Q, A, or Comment on THIS thread -or- Start a NEW Thread