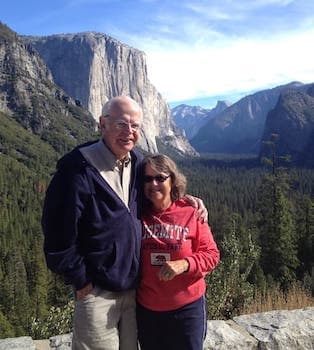
Curated with aloha by
Ted Mooney, P.E. RET
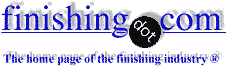
The authoritative public forum
for Metal Finishing 1989-2025
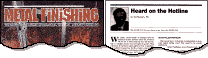
-----
Comparison between galvanizing and powder coating
2006
Dear Sir,
We are a leading company in Dubai, and we have a project in which we have to do a mild steel balustrade laying 2 meters above the see level. The Arabian Gulf are is a high-humidity area, and so, the corrosion issue is the priority number one for us. The consultant is asking us to apply the powder coating, but we can't do that since we can't make any kind of welding after the powder coating, plus another difficulties and that shall make the powder coating process too hard to be used. We proposed to galvanize the material and then to apply a wet coat. Is it acceptable? and how can I proof that to the consultant?
Thanks and Regards
- Dubai, United Arab Emirates
2006
Hi,
I would like to suggest you to use powder coated aluminium extrusions for balustrade (especially done by some QUALICOAT certified Powdercoater).
If you want to use mild steel then you can contact your local powder manufacturer who has all the answer for you.
Good luck.
- Dubai, U.A.E.
2006
Galvanized balcony railings near the sea will last longer than painted, but will still corrode. Galvanizing protects by the zinc corroding in preference to the steel, but when its all gone, then the steel rusts.
Marine environments are one of the most aggressive, so you should be not considering either / or, but both.
Hot Dip galvanizing to ISO 1461 followed by powdercoating, or perhaps solvent based paint. But either of these two top coats needs a competent pretreatment to ensure adhesion of the galvanizing.
This duplex coating should give 15+ years even in this environment. A factory based application would be far better than a site applied coating.
Welding after coating is to be avoided. It will destroy any coating. You should fabricate to avoid welding. Use bolted connections. If making to fit an existing site, then measure well and make to fit. Don't weld coated steel.
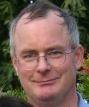
Geoff Crowley
Crithwood Ltd.
Westfield, Scotland, UK
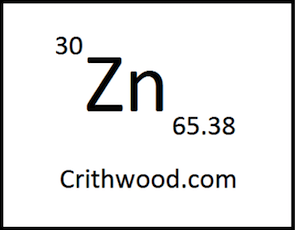

Q, A, or Comment on THIS thread -or- Start a NEW Thread