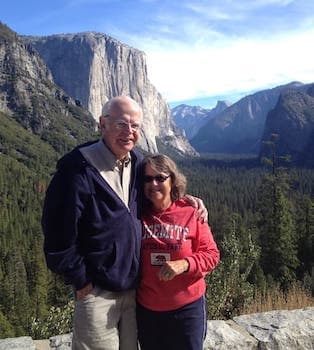
Curated with aloha by
Ted Mooney, P.E. RET
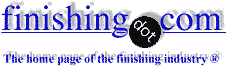
The authoritative public forum
for Metal Finishing 1989-2025
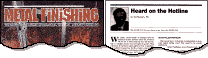
-----
Hard anodizing testing methods and surface characterization
Q. I need some information about (hard) anodized aluminum layers, especially testing methods, layer characterisation (mechanical properties, morphology etc.)
Kerstin Baldus- Kaiserslautern, Germany
2000
A. Aluminum anodizing is an electrochemical conversion of the surface metal into a crystalline aluminum oxide. In Hardcoat anodizing, the processing parameters are adjusted to create a thicker and denser coating than commercial anodize. The thickness is easily measured with eddy current devices. Hardcoat is typically 40 to 60 µm thick verses 2 to 15um for conventional anodize. The density determines the wear resistance or "hardness" of a coating. Commercial anodize is normally not wear tested. American hardcoat standards, MIL-A-8625 / MIL-PRF-8625 [⇦ this spec on DLA] Type III and AMS2469, use a Taber Abraser to measure the coating weight lost in a standardized wear test. European hardcoat standards, ISO 10074 and BS 5599, use an abrasive wheel or Suga tester as the primary test to measure coating weight and/or thickness loss. This test is much less standardized as many of the test parameters are left to to discretion of the tester. All these specifications set minimum wear resistance standards for hardcoat anodize. Due to limitations of these wear tests, Vickers microhardness testing is occasionally substituted. Typical hardness values are 300 to 600HV.
Chris Jurey, Past-President IHAALuke Engineering & Mfg. Co. Inc.

Wadsworth, Ohio
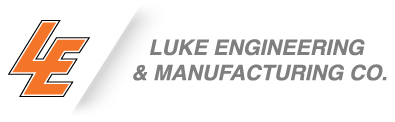
Q. We build rowing shells & accessories. A subcontractor hard anodizes our aluminium alloy 'riggers'. We're at the top end of our market but the anodizing has become a problem:- Our riggers are made by connecting seamed 5251 & drawn 6082 tubes with spigoted LM4 (Al Si5 Cu3) castings (resin-bonded joints). The anodizer receives them clean & Scotchbrite abraded. Most anodizing over some years has been good, but variability has increased of late: some batches have pale, fragile film on the tubes which fails the tape-peel test! The subcontractor blames the metal, esp. the 5251, but has had good & bad results from identical tube batches. We think that his QC is failing. But what, in reality, is happening? We're going up the wall & would welcome expert comments, please!
Thank you,
Carl DouglasCarl Douglas Racing Shells - Staines, Surrey, UK
Q. During hard anodizing of kitchen utensils deep drawn from AA3003 alloy the colour goes from dark grey to light grey on the same parts. What should be done to obtain the colour just dark grey during hard anodizing.
Yasar BayraktarEti Aluminium - Seydisehir, Konya, Turkey
2003
Q. Hello!
Firstly, my English is not so good, sorry. I have already finished chemist department in Cukurova University in Turkey and I am going to go on with my education to a masters degree.
I am going to investigate about hard anodizing and in this subject you can help to me the best.
If you can help me about this subject, in fact I will very happy and successful .
thanks I will wait your help
Cukurova University - ADANA, TURKEY
2005
A. Buy some good books like ASM Metals Handbook Volume 5 including surface finishing of aluminum ⇦ this on eBay, Amazon, AbeBooks [affil links] and others. They can be found on line.
Guillermo MarrufoMonterrey, NL, Mexico
2005
Q, A, or Comment on THIS thread -or- Start a NEW Thread