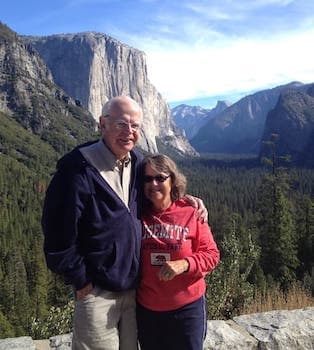
Curated with aloha by
Ted Mooney, P.E. RET
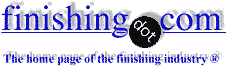
The authoritative public forum
for Metal Finishing 1989-2025
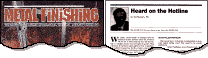
-----
Prevent corrosion of Aluminum in salt water
Q. I am doing maintenance on boats made out of aluminium. Have experienced corrosion pitting on bottom plating, etc. Boat is working in salt water. This is more serious on the inside of the plating. Need some solution to this problem. The boats are about 12 years old.
Suresh kapur- Hilton Head South Carolina USA
2000
A. Hi. You do a Xylan/Teflon/Dykor/Greblon, etc., fluoropolymer based coatings on your aluminium boat. That protects from salt water up to 20 Years.
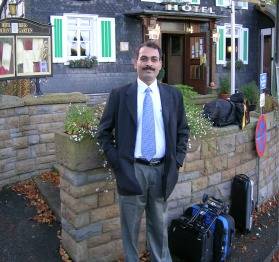
Kalyan Dhakane
Mumbai, India
2000
A. The fluoropolymer is along the right track, for repair of these boats sand blast to white metal, apply the fluoropolymer coating as soon as physically possible. Contrary to popular opinion, Al corrodes almost instantly, the oxides will hurt adhesion. Under new production conditions I'd recommend chemical treatment before paint, but that may not be an option for you.
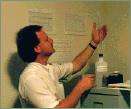
Jeff Watson
- Pearland, Texas
2000
A. Wouldn't hard coat anodizing do a pretty good job of corrosion protection in salt water? If that wouldn't be sufficient I think hardcoat impregnated with a fluoropolymer would be great.
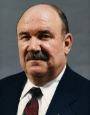
Daryl Spindler, CEF
decorative nickel-chrome plating - Greenbrier, Tennessee
2000
A. Hi. First you do sand/grit blasting, hard anodizing and then fluoropolymer coating. Hard anodizing giving a 60 micron thickness and afterward fluoropolymer coatings obtain up to 200 micron thickness. This system protects your boat minimum 20 years from salt water.
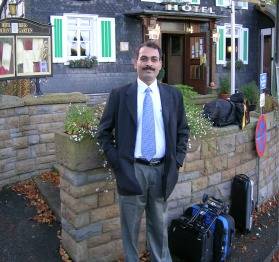
Kalyan Dhakane
Mumbai, India
2000
adv.,
Everbrite Protective Coating is a one part, clear coating that will protect the aluminum and other surfaces from salt water corrosion. It will also protect from U.V. oxidation. You can see more information by following the link to our website.
Everbrite Coatings

Rancho Cordova, California
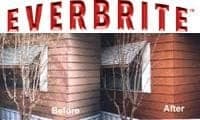
2000
Q. Have a 1997 aluminum 14 l/1 MonArk fishing boat that is developing numerous holes in middle section of hull. Planning to drill holes in floor of boat and fill hull with closed ceil flotation.
Good Or Bad Idea? If good, what to use and where to get. If bad, please explain. Thanks.
Ray Burns- Charlotte Harbor, Florida, USA
2001
Protecting aluminum from saltwater
Q. What kind of primer and paint should I use to protect a cast aluminum fishing reel from saltwater corrosion?
John Segal- Nanaimo, BC, Canada
2002
Aluminum fence on salt water: best finish
Q. Aluminum fencing, which is the best finish for location on salt water?
Holly Ferguson- Miami Beach, Florida
2002
A. The term "powder coating" is so universal now that there is a connotation of "magic" implied. Like most coatings the devil is in the details. Powder coatings are by far the best coating for salt spray conditions, but the chemistry, manufacturer of powder, quality testing at the applicator and the pretreatment process used are the critical elements. The surface preparation is so critical and the most likely item to be abused. I recommend a 5 stage pretreatment with attention to proper cure. The evaluation of the applicator is often done as part of a powder manufacturer certification process. I recommend seeing these documents. Beware. BUT there are 10, 15 and 20 year warranties available. Good Luck.
Buddy Miller- Claxton, Georgia, USA
2005
Aluminium corrosion protection in seawater
November 24, 2015Q. Hi
I created a diving light which will be a lot in sea water and a little bit in fresh water.
Aluminium used is the 5000 series.
I was thinking to anodize it and put power coating.
I want to get it a black finish and keep it during a couple of years.
Any suggestion to get aluminium good with salt water?
thanks
- Canada
A. Hi. You're on the right track, although chromate conversion coating before the powder coating would probably be as good as anodizing, and less expensive, and offer conductivity which you might want ... for example, I think a tiny replaceable zinc anode for salt water would not be a bad idea, although magnesium would be better for fresh water.
Regards,
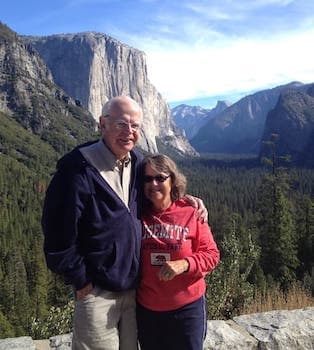
Ted Mooney, P.E. RET
Striving to live Aloha
finishing.com - Pine Beach, New Jersey
November 2015
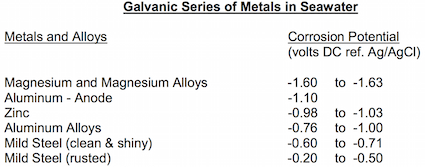
^ from http://www.nordhavn.com/resources/tech/images/Galvanic_Series.pdf ^
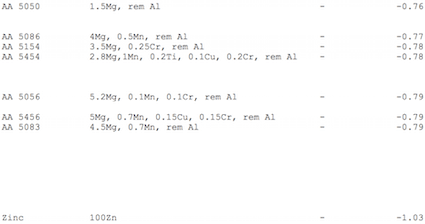
^ from http://esmat.esa.int/Services/bimetallic_data/Bimetaltable/bimetalemf.html ^
Well, I am not sure how a Zn anode could be expected to protect Aluminium, though I am willing to listen and learn.
I would think that the best protection could be to select a marine aluminium as a base, give it a chromate pretreatment and then give it a fusion bonded epoxy finish coat.
Hope this helps,
Regards,
Bill
Trainer - Salamander Bay, Australia
November 29, 2015
Hi William. You're probably right about Zinc anodes offering negligible (<1/4 volt) protection for aluminum alloys. The 5xxx series are the marine grade, so Eric is off to a good start :-)
Regards,
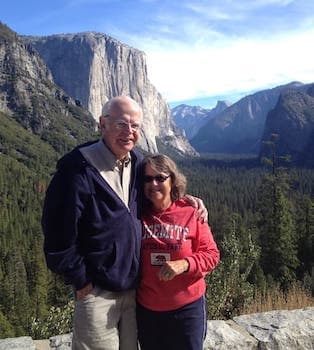
Ted Mooney, P.E. RET
Striving to live Aloha
finishing.com - Pine Beach, New Jersey
November 2015
Plating 6061 Aluminum for sea water submersion
Q. I have a 6061 aluminum parts that will be submerged in sea water. The parts have o-ring grooves that need a 16-32 surface finish to seal properly. I was originally thinking of Electroless Nickel plating to .001 thickness on all surfaces of the parts which also have tapped holes. My thought was that nickel lays an even and smooth surface that would be corrosion resistant and provide good o-ring sealing surfaces.
However, the electrical potential difference between Aluminum and Nickel is 450mV (galvanic corrosion).
And would the threads on the 1/4-20 tapped holes bind due to .001 finish thickness?
My alternate solution for corrosion protection would be to chem film the o-ring surfaces, then mask them and Hard Anodize the remaining surfaces of the parts.
By the way, spec says anodizing tapped holes 1/4-20 and larger is ok.
Does anybody have practical experience with either finish on aluminum submerged in sea water?
buyer - San Diego, California
September 12, 2018
Coating small aluminum parts in bulk for seawater resistance
Q. I have many small aluminum parts and looking for corrosion resistance to sea water. Is there a finishing/sealing process that can be used for baskets of hundreds of small parts (i.e., tumbling to coat and layout to cure)?
John Sundnescompany owner - San Clemente, California
March 13, 2020
A. Hi John,
Any coating, once chipped, will expose the parts to the seawater again so you've got to do something UNDER the paint too.
Chromium conversion coating is not only a good protection against corrosion, it helps the paint adhere better too, and prevents it bubbling and peeling if scratched. As a bonus, it doesn't require electrical contact, so would be possible to basket-process.
The other option is anodizing; the parts would need to be racked appropriately, and this is done by hand and can be time consuming and therefore expensive.
You'd want to weigh one time consuming process against a double process before committing.
Stainless steel isn't an option?
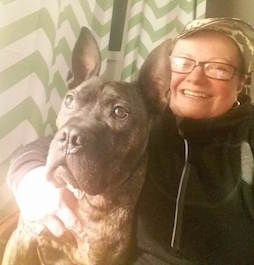
Rachel Mackintosh
lab rat - Greenfield, Vermont
May 11, 2020
Q, A, or Comment on THIS thread -or- Start a NEW Thread