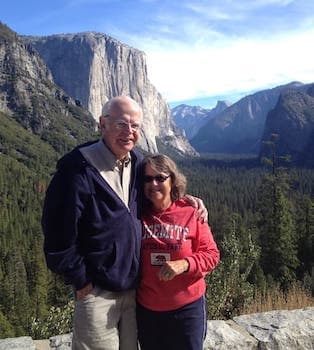
Curated with aloha by
Ted Mooney, P.E. RET
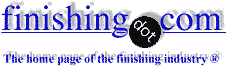
The authoritative public forum
for Metal Finishing 1989-2025
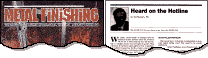
-----
Laminated peel-off problem in nickel plating
Q. I AM MANAGER OF A LARGE PLATING SHOP. WE DO TRI-NICKEL PLATING ON TWO WHEELER PARTS. WE SOMETIMES FIND PEEL-OFF PROBLEM (FEW PIECES ONLY) IN WHOLE DAY OF PRODUCTION. THE PEEL-OFF IS BETWEEN LAYERS. WE ARE NOT SURE FROM semi-bright OR FROM TRI-NICKEL.
RATTAN SHARMA- INDIA
2006
A. Please check the activation of plating layers.
Manish Jain- Delhi, India
2006
A. Dear Rattan Sharma saheb,
Check transfer time between the two nickels. It should be only a few seconds, otherwise the first semi-bright nickel will passivate and product will land into peel off after bright nickel.
Regards,
- Ajman, UAE
2006
2007
A. Dear Mr. Sharma,
Pleased to assist you for this kind of problem, based on my experience I would like to say that in the tri-layer nickel plating peel of and not all parts, you can sure that this was not from the solution.
So, in this case I would like to say that you got lose contact for even only 1/million second it can cause problem.
So firstly, you have to find out which racks that produced the peeling off.
You have to mark the rack and using the same rack and do normal plating from pretreatment up to nickel chrome if the problem occur again that means the jigs has malfunction, change the old rack and use new one and try again as above.
This might be due to loosen contact between the racks tip and the parts.
Might be the contact full of Nickel deposit, and never clean the rack tip and the contact point become loosen.
Secondly might be cause by the dirty busbar or loosen contact between jig hook to busbar.
Normally because of the hook become wider and the contact point become less, and the parts will get current interruption or discontinue current during plating or cause bi-polarity effect in the nickel plating, this also can cause peeling of in the nickel plating because the nickel layer become passive.
Both problem also can cause bi-polarity effect since the current discontinue is harmful for nickel plating ( thick layer or multiple layer ), and will cause laminating nickel and then become peel off
Suggestion:
1. Clean all the contact point no more big flower of nickel deposit, make sure the parts sitting firmly on the tip of racks - no moving
2. Tighten the hook of the rack to busbar, no loosen contact / current
Hope that I have given some hint to solve your problem.
Good luck Mr. Sharma.
Best regards,
- Jakarta, Indonesia
Q. We are in to plating on ABS Plastics. We are under peculiar problem, we are getting laminated deposit in the semi bright nickel layer. This problem observed in 1 or 2 baths in a day's production. We have verified all electrical connections, racks, anode busbars, cathode bars, bath parameters and all are in good condition. Kindly suggest us how to solve the above problem.
Thanking you,
T N Rajesh
- Bangalore, India
July 30, 2012
Q. We are in to Electroplating on ABS Plastics. We are in deep trouble as we are getting lamination layer in semi bright nickel layer. We have observed that the pieces getting rejected are in High Current Density Areas only. We are getting this type of defect in 1 or 2 batches in a day and also the parts getting rejected are opposite parts in a rack. We have verified all Electrical connections, Bath parameters, Anode level in the bath, Brightener content in the bath, TOC and all the parameters are intact. Please suggest us the root cause for this problem.
RAJESH TN- Bangalore, India
August 7, 2012
Q, A, or Comment on THIS thread -or- Start a NEW Thread