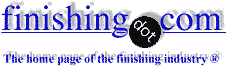
-----
Alumina oxides electroplated on a aluminum fin
Hi.
I am developing a novel technique of adhering desiccant to a fin substrate. I believe the first step is to prepare the surface to have an ability thereafter to adhere a porous desiccant to adhere to its surface by calcination. The first step is I have gamma alumina oxide (desiccant) which I mixed with phosphoric acid and water I pepcidized the slurry and put this in a bucket as an electrolyte. I then take two fins of aluminum one I define a a cathode and the second as an anode. I then applied dc voltage to it. I am hoping to create a purification of salt and simultaneously adhere it through the electrolyte process to the fin. The question is what are the factors which I have to consider?
- Texas
2006
2006
Hi Gerry,
I think it's quite difficult to electrodeposit gamma (or any other) alumina. Aluminum oxide dissolves in phosphoric acid to form aluminum phosphate (as sludge).
Check out this method for 'electroplating alumina' onto metal ù actually decomposition of an aluminum nitrate-alcohol solution at the cathode: ','
US Patent 4094750.
Similar: 'Cathodic electrosynthesis of alumina thin films and powders' by T. S. N. Sankara Narayanan and S. K. Seshadri, Journal of Materials Science letters, Volume 19, No. 19 (October 2000).
Hydrothermal treatment (boiling in DI water) forms boehmite (which can be dehydrated to gamma alumina) on aluminum. Used in Sanchem's SafeGard CC coating. For more info and additional methods, see pages
233-239 in
The Surface Treatment and Finishing of Aluminum and Its Alloys, 6th Edn. Not very thick coatings, but perhaps treat an entire coil of aluminum (embossed landscape edging, perhaps?) for greater surface area. Or, partially sinter coarse aluminum powder into the desired shape, then hydrothermally treat.
- Goleta, California

Rest in peace, Ken. Thank you for your hard work which the finishing world, and we at finishing.com, continue to benefit from.
2006
Well you are right , it is difficult to adhere desiccant alumina to a fin. I hit a process which I do not understand in part. Here is the explanation
First I dipped the alumina into a phosphoric acid removing all AlO3. Then I installed this fin into a water and phosphoric acid as the anode and got a consistent porous anodized film. If I add acid concentration then the pore get closer I go to about 15 % acid 20 volt for 20 minutes at 25 c
After I put this into a desiccant slurry 100g pre-cooked alumina desiccant known to giving a gamma alumina once calcinated to 450 °C/ 150 g of h2o and 350 g of phosphoric acid 85 % in concentration. I blend this slurry together with a high speed blender adding slowly the acid as the last ingredient in a fin spray. Then I put the aluminum anode back into this new slurry and keep it as the anode. I apply a 4 volt dc current to it as a electrolyte.
It seems that the acid works the fin with time, but in a pattern like arrangement reacting also to the desiccant salt content /and that the
4 volt longitates the salt in a magnitized arrangement and that the slurry creates pure salt simultaneously. I am hopping to get kind of a microscopic solid needle attached on a fin. Then I will calcinate it
and then after once calcinated I will add through a simple dipping process, a porous slurry type of alumina to complete the fin
I am not electrodepositing/ I believe that the 4 volts creates just a magnetic potential to give both / the salt purification and the alignment of the salt attached to the fin.
Am I making any sense or I am just viewing a mistake by interpretation
Thanks
- Texas
2006
You are perhaps doing e-coating (electrophoretic painting). The voltage causes anions (created in the gamma-alumina-phosphoric acid slurry) to adhere to the pre-anodized aluminum anode. A limitation is that only a monolayer of particles can attach to the surface. It may be difficult to rinse off the phosphoric acid w/o losing the coating.
Calcine, check the adhesion and test the desiccant efficacy. If promising, identify the crystalline product by x-ray diffraction.
- Goleta, California

Rest in peace, Ken. Thank you for your hard work which the finishing world, and we at finishing.com, continue to benefit from.
2006
Hi
I believe you are right on the e-coating but the fact that the cathode was previously anodized as a pre-treatment
the e-coating was done after with the alumina/phosphoric/water gel or slurry.
Could this have created another type of reaction? per say the reaction of oxygen from the anodized aluminum increased the thickness and arrangement of the attached alumina cation particles
Also permitting a needle like pattern. It looks to me like a granular needle pattern and about .002 to
.0015 inch thickness to much for anodizing or e-coating
I just wonder if I was just able to increase the thickness buy using a pre-anodized cathode. I am e-coating alumina on alumina oxide but do to the phosphoric acid does the oxidized alumina have a reverse reaction to the e-coating permitting an added pattern of needle like particles
the alumina oxide will expand at a different rate from the aluminum and destroy my future objective when I calcinate it
should I also try this with pre-calcinated gamma alumina in the slurry?
- Texas
2006
Possibly, the needles are crystal growth from a supersaturated solution -- hydrated aluminum phosphate, bayerite, boehmite...?
Calcination seems necessary for 1) long-term adhesion of electrostatically attracted particles to the substrate, 2) removal of water to restore the desiccant functionality, and 3) conversion of aluminum hydrates to gamma-alumina. Some testing seems necessary. Good luck.
- Goleta, California

Rest in peace, Ken. Thank you for your hard work which the finishing world, and we at finishing.com, continue to benefit from.
Q, A, or Comment on THIS thread -or- Start a NEW Thread