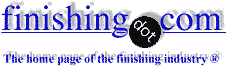
-----
Corrosion of surface condenser in seawater
2006
Hi,
I am looking for suitable material for surface condenser at sea water
.The material of existing surface condenser is Cu-Ni (70-30).BECAUSE THIS MATERIAL IS NOT RESISTANCE AGAINST CORROSION .
composition of sea water is ;
tem.=35(c) press.=3.6(barg) PH=4.7~7.1 SO4=4300 (PPM) NA=14600~15900
(PPM)
HCO3=370 (PPM) CL=36500 AS CACO3 CA=1440 (PPM) AS CACO3 TH=8660(PPM) AS CACO3
MA=220(PPM) AS CACO3 SALINITY =4000(PPM)
THANK YOU
- Tehran, Iran
The 70-30 Cu-Ni alloy is normally very resistant to seawater at low-to-moderate flow rates (1.2 m/s) but the protective oxide film is eroded at high flows. Also, seawater usually has pH 8; low pH is a problem.
Please confirm pH value & give flow rate. Describe the corrosion
is it worse in bends?
- Goleta, California

Rest in peace, Ken. Thank you for your hard work which the finishing world, and we at finishing.com, continue to benefit from.
2006
2006
Your problem my be a reaction between different metal. Water box, tubes, tube sheet, etc. I have applied ceramic filled epoxy to
"insulate" the tube sheet.
Regards,
- Concord, California, USA
2006
1- the supplement of sea water is installed closed to the ammonia
⇦ on
eBay or
Amazon [affil links] plant. therefor , the effect of ammonia the sea water is probable
.
2- refer to the data given before, the new data about water and analysis will be given to complete the information for your suggestion.
PH=5~8.5 , SO4(-2)=3.8~6 mg/l , TFe=0.05~0.7 mg/l , NH4+=0.48~6 mg/l water rate=2,500,000 kg/h and steam rate=45,000 kg/h .
3- the main corrosion will happen inside the tubes .
please , what is your recommendation for the type of material instead of copper nickel (70-30) alloy.
best regards
- Tehran, Iran
2006
Please give the linear flow rate of seawater through the tubes this is a crucial parameter.
Is the alloy actually 70-30 or instead, an alloy containing 0.4-1% Fe
(UNS C71500, BS CN 107, ISO CuNi30Mn1Fe)? The Fe increases the resistance of the oxide film against erosion, allowing higher flow rates. For seawater in C71500 condensers, usual flow limits are 0.3 m/s minimum (avoids sedimentation) and 4-4.5 m/s maximum (avoids erosion). The Cu-Ni-Cr alloy C72200 can be used for flow rates to 9 m/s. -- p. 141,
ASM Metals Handbook Vol. 13 'CORROSION'
⇦[this on
Amazon affil links].
I am not convinced 6 ppm ammonia is the cause; C71500 & other Cu-Ni alloys are more resistant than is Cu. Please describe the corrosion: general or localized, any corrosion products, bare metal & thinning, porosity, metal discoloration, etc. Any sand or fouling? How are the tubes cleaned? Any biocide used & if so, what concentration? Any contact with other metals which may have galvanic effect, as mentioned by Jim Wood?
To initiate formation of a protective oxide film on new tubes, leave fresh water containing 5 ppm ferrous sulfate
⇦ on
eBay or
Amazon [affil links] in the system for 1 day.
-- p. 658,
Handbook of Corrosion Engineering. Are you perhaps adding ferrous sulfate
⇦ on
eBay or
Amazon [affil links] to your system?
- Goleta, California

Rest in peace, Ken. Thank you for your hard work which the finishing world, and we at finishing.com, continue to benefit from.
Q, A, or Comment on THIS thread -or- Start a NEW Thread