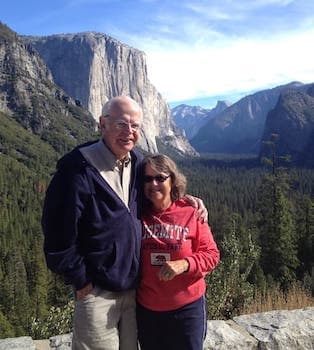
Curated with aloha by
Ted Mooney, P.E. RET
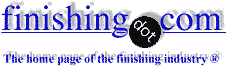
The authoritative public forum
for Metal Finishing 1989-2025
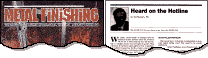
-----
Relationship between thickness of oxide layer and time/ voltage for anodizing Al-Alloys
Q. I need the graph of the relationship between thickness and time/voltage for anodizing Al-Alloys.
Muhammad BashirGIKI - Topi Swabi, Pakistan
2006
A. The graph is dependent on alloy as well, and is available in the "Surface Finishing and Treatment of Aluminum and Its Alloys" book noted in the recommended books section of the homepage of this site.
I don't have an electronic version (and, I'm sure its copyrighted anyway), sorry.
You don't need the most recent version, by the way, the second to last version has the graph also (and possibly earlier versions as well) and can be bought used for significantly less money.
Good luck!
Compton, California, USA
2006
2006
A. Thickness vs. time at constant current density, electrolyte concentration and temperature is usually reported.
From 'Anodizing Characteristics of Commercial Aluminum Alloys in Sulfuric Acid,' G. H. Kissin et al., pages 13-31 in
The Finishing of Aluminum (1963):
The anodizing rate for wrought alloys 1099, 1100, 3003, 5005, 5052, 5357, 6061, 6063, & 7072 is ~0.405 micron/minute (15 wt% H2SO4, 12 Amps/sq. ft., 20 °C) for anodizing times to ~90 minutes. Slightly lower rates for longer anodizing times (>60 minutes) and higher temperature (25°C).
Slightly higher rates (0.41 micron/minute) for Al 4043 & 4343.
Rates for 2014, 2024 & 7075 are lower, especially at the higher temperature (25 °C) and longer times (>40 minutes).
The voltage necessary to maintain the current density of 12 Amps/sq. ft. is shown as a function of time for the above alloys (at 15 wt% H2SO4, 25°C). The voltage increases roughly 5% over the anodizing time of 5 to 60 minutes. Lowest voltages (13-14 V) required for 7072, 5052, 6063 & 7075. Highest voltage (18-19 V) for 2014.
'Effect of Voltage During Anodizing of Aluminum,' by W. C. Cochran and F. Keller, pages 104-126 in the same book may be of interest. Voltage, sulfuric acid concentration and anodizing temperature were varied. Coating weight, abrasion resistance and clarity are reported for Al (99.99%) and bright anodizing alloys including 5357, 5557 & 6463.
Please post any measurements on-line.
- Goleta, California

Rest in peace, Ken. Thank you for your hard work which the finishing world, and we at finishing.com, continue to benefit from.
Aluminium vs. titanium anodizing racks
Q. Dear sir,
When rack a part made up of 7 series aluminium alloy with aluminium wire; the amps it takes up to 13-15A (constant Voltage method) and the coating thickness was 27-30 microns and dyed for 2 minutes but the dye particles wiped off by hand. Because of our requirements, i.e., 2-25 micron, we reduced our anodising time and dyed for 2 minutes but the dye stuff could not be wiped off and achieved the thickness and this time the amps takes up to 9-10A.
And if we rack in titanium on a same component it only takes up to 5-6A, dye stuff could not be wiped off and the coating thickness was 14-16 microns but galvanic corrosion happened.
For the above cases we did the process without de-oxidizing. And also we took the same parts for another trial, which is racked the same component with aluminium wire, deoxidation for 2-4 minutes and anodised, this time the amps for a single part takes up to 19-20A and dyed for 2 minutes but dye stuff wiped off and the thickness was 27-30 micron. Why is this happening? Could the deoxidation of the part accelerate the coating thickness compared to the part processed without deoxidation.
Due to galvanic corrosion we have faced pitting on the component when we rack the aluminium with titanium, so that we have switched over to aluminium wire. Now we have overcome galvanic corrosion, but we are facing the above problem.
Kindly help us.
- Chennai,Tamil Nadu and India/Indian
April 2, 2019
A. Hi Umaraj. I may be wrong, but I think your attempt to answer your questions and solve your problems becomes hopelessly complicated when you mix racking materials of aluminum & titanium, the dye sticking or not sticking, different anodizing thicknesses, galvanic corrosion or no galvanic corrosion, various anodizing voltages & currents, and de-oxidizing vs. not de-oxidizing all into one grand unified question.
Sorry, but I can't even follow what the question is, let alone the various partial data points you are trying to provide :-(
Please ask one non-compound question and we can hopefully comment on whether you have provided the necessary data to try to address it. Thanks!
Regards,
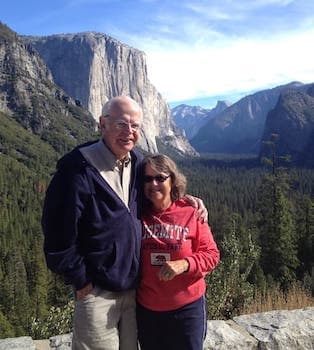
Ted Mooney, P.E. RET
Striving to live Aloha
finishing.com - Pine Beach, New Jersey
April 2019
Q, A, or Comment on THIS thread -or- Start a NEW Thread