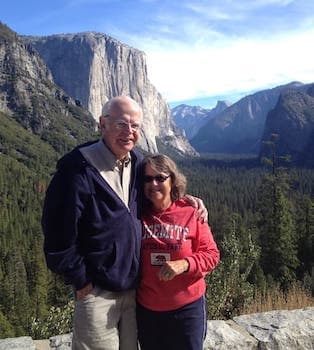
Curated with aloha by
Ted Mooney, P.E. RET
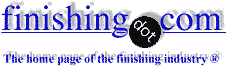
The authoritative public forum
for Metal Finishing 1989-2025
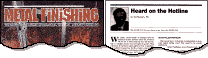
-----
Aluminum Alloy B-535.2 Hard Anodize Surface Treatment (Seawater App)
COTS Cast aluminum structural members have been selected as fixtures for a sub-surface seawater test platform. I am curious about the compatibility of applying hard anodize to these components. The catalog states that they are composed of B-535.2 Aluminum Alloy. This alloy composition is approximately 92% Aluminum. Will this type of alloy gain any benefit from surface treatment with hard anodize?
James Mark HarperMechanical Engineer - Tucson, Arizona, USA
2006
First of two simultaneous responses --
Some of the 535 I have seen did not have the magnesium alloyed, instead the magnesium was separated out in random hunks, some on the surface, and you do not "anodize" magnesium in 15%/wt sulfuric acid. Further the sodium chloride in the sea water will attack and dissolve hydrated aluminum oxide, aluminum oxide, and aluminum !
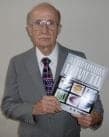
Robert H Probert
Robert H Probert Technical Services

Garner, North Carolina
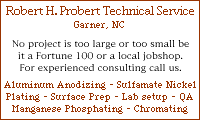
2006
Second of two simultaneous responses -- 2006
This alloy has good corrosion resistance due to very low limits on alloying elements other than Mg; the nasty Cu is 0.05% max. For improved corrosion resistance, conventional anodizing may be better than hard, as the latter often contains microcracks (crazing). Due to the high Mg content, the anodizer should use a nitric acid deoxidizer prior to caustic etching (or even skip the caustic).
Hard anodizing would be beneficial in sand-washed areas. Sealing must be specified for hard anodize, as the default is unsealed.
- Goleta, California

Rest in peace, Ken. Thank you for your hard work which the finishing world, and we at finishing.com, continue to benefit from.
Q, A, or Comment on THIS thread -or- Start a NEW Thread