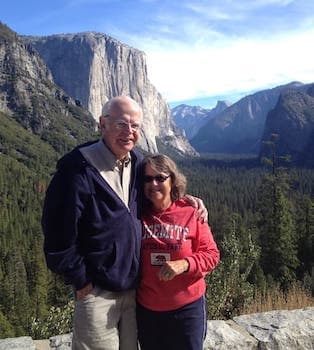
Curated with aloha by
Ted Mooney, P.E. RET
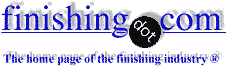
The authoritative public forum
for Metal Finishing 1989-2025
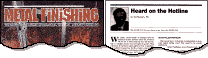
-----
Hard anodizing to a matte black finish
Q. We are getting an aluminum shaft hard anodized. The alloy is ADC6 and we need a jet black color with minimum 25 microns thickness. What particular alloying elements and what % can cause/not cause it to be black enough? Currently we are getting a black color but slightly grey-ish not jet black. Cu is 0.1%. Please help.
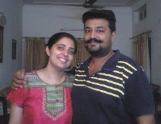
Vikram Dogra
Irusha India - Chandigarh, India
2004
QUICKSTART:
To clarify a semantics issue in order to not confuse readers who may be using these dialogs as a learning tool:
Some people consider "hard anodized" / "hardcoated" to involve/imply a thickness of about 50 microns (0.002"). Still, "hard anodized" is just a two-word piece of commonly used language, it is not a specification, so exactly what it means is open to a bit of interpretation. As you see here, Vikram considers his finish to be "hard anodized" even though the thickness is only 25 microns (0.001").
Hard anodized coatings are not usually dyed or sealed because that may soften them; but, because only the aluminum portion of an aluminum alloy anodizes to relatively transparent aluminum oxide, alloys which contain other materials may turn gray or charcoal or black depending on the alloy and the thickness of the anodizing. Marc is suggesting that dyeing is the most reliable path to black, but increasing the thickness or doing other tweaks may enhance the natural darkness.
A. At such a low thickness, I doubt you'll get a "jet black" color. I would suggest 50 microns, or go ahead and have your work dyed black (the latter being the better of the 2 options for a nice black color) Other factors in hardcoat color are current density and bath temperature and, of course, the base alloy.
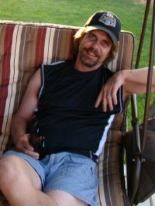
Marc Green
anodizer - Boise, Idaho
2004
Q. I WOULD LIKE TO KNOW CORRECT ALLOY FOR MAKING HARD ANODIZED PRODUCTS OF ALUMINIUM AND CONTROLLING ELEMENTS OF THE ALLOY TO GET JET BLACK COLOUR AFTER ANODIZING, PREFERABLY MIN. TO MAX. OF THE ELEMENT.
JITENDRA SHAH- Mumbai, MAH, INDIA
2004
Q. I am a manufacturer and build mostly small gun parts for military/ tactical applications out of 7075-T6 aluminum. I am trying to achieve a matte or dull hard black anodize finish but haven't been able to achieve it with repeated success. I have tried bead blasting with glass, sand, and aluminum oxide with different intensities and in one rack of parts some are perfect while others are lighter shades of grey to dark black. If no blasting is done and the parts are only tumbled to remove burrs the color is very nice and consistent, but the parts look polished and glossy. If the parts are etched too long graining occurs and the surface finish just doesn't look good. Is there anything I can try that will give me a dull finish or am I stuck with what I have? I have seen other parts out of 7075 that have the exact surface finish that I am looking for so I know it can be done. Other anodize shops say to blast the parts with glass beads, send them and they can do it. I don't want to ruin another run of parts (300+) but I need to get them to customers. Any recommendations on this process would be greatly appreciated.
Thank you,
- Lewiston, Idaho
2006
A. You cannot manually blast (whether bead, glass,sand or other) and get a uniform surface. It looks good as is to the naked eye, but after you anodize you magnify the different surface finishes as a function of where and when the manual wand was held nano-seconds longer in some places than other places.
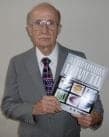
Robert H Probert
Robert H Probert Technical Services

Garner, North Carolina
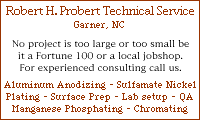
2006
A. We currently do upper and lower frames, glass bead and hard black anodize. We have not had a problem in some time. It's all in the blasting technique. It needs a painter's touch.
Edward Nygaardwet process eng. - Phx, Arizona
2006
A. Glen...I had the same problem when anodize on sand blasted surface (6063 material). Some parts are ok but some have dark patchy area.Try anodize at much lower current and use a deoxidizer instead of nitric acid for your desmutter.
Cheahsinkooi- Penang, Malaysia
2006
A. Try this method, it has worked for me very well. Glass Bead blast the parts. Pre-clean and start in the hardcoat. As soon as the ramp is complete, shut off the rectifier and remove the parts. Strip, desmut and hardcoat as usual. you will remove the inconsistencies in the blasting.
Joel A. Lipof- Paterson, New Jersey
2006
Hard Anodizing Process - To achieve Deep Black
January 6, 2015 Q. Hi
I Really Appreciate the Wonderful Efforts you put in for the Queries been Posted here. Let me come to the Point Straight Away. I run a Hard Anodising Plant where we HardCoat Al 3003. We are Operating with 12 % sulfuric Acid and Temp -5 to 0 Deg. Al content 3 g/l + Thickness up to 55 Micron. Please suggest us how to Deepen My black as customer Expects More Deeper Black Colour.
Thanks, regards,
Yours sincerely,
- Chennai,tamilnadu, India.
A. A brief (5 min) 5%-10% (vol) HNO3 dip prior to dyeing should help. Obviously rinse well prior to dyeing after the dip.
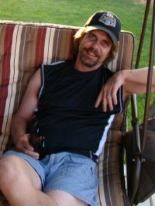
Marc Green
anodizer - Boise, Idaho
January 9, 2015
Deep black is not easy with hardcoat. It's usually gray to dark gray. You *could* try dying after anodize, but as one supplier of room temp blackening once told me: "There are many colors of black". LOL!
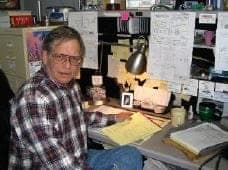
Jeffrey Holmes, CEF
Spartanburg, South Carolina
January 9, 2015
Thanks Jeffrey. Yes, there is only one true black; no shine, no red tint, no blue tint -- as if there was a hole in the universe where the object is. I think some of the low emissivity black paints come close in the human visual range :-)
Regards,
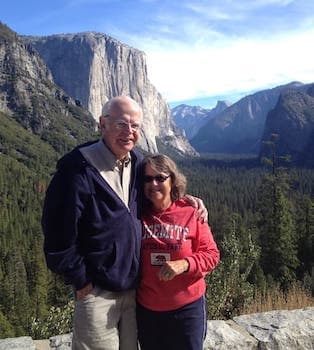
Ted Mooney, P.E. RET
Striving to live Aloha
finishing.com - Pine Beach, New Jersey
Q. Hi
I manufacture hard anodized cookware products.
I usually get greyish color not black. What do I have to do to get perfect black color?
- Rajkot gujarat India
April 3, 2017
A. Hi cousin Raju. Many people already addressed that subject before you, and several already offered their suggestions -- so you probably need to pose your questions in terms of those suggestions and/or add significant detail before further progress will be possible...
But a couple of things do come to mind. You say you "usually" get greyish color. What have you learned about the factors that controlled how light or how dark your finish was when it varied? Have you attempted to reverse engineer your competitors' "perfect black color"? Thanks!
Regards,
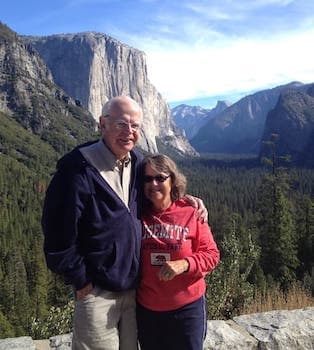
Ted Mooney, P.E. RET
Striving to live Aloha
finishing.com - Pine Beach, New Jersey
April 2017
July 20, 2017
Q. Hello.
I am an anodization newbie and have run into some issues/
We have two parts machined from 6061 aluminum. Both parts have a finish note: "Matte Black Anodize per MIL-A-8625 / MIL-PRF-8625
[⇦ this spec on DLA], Type III Class 2 with a nickel acetate seal"
In our initial samples, we received two different appearances. The first was a true matte black finish, while the second was glossy. Apparently the matte finish was due to a batch of parts being rejected, stripped, and re-anodized. The stripping process altered the aluminum surface to produce a perfect matte.
I was told that the stripping process would not work on the raw aluminum parts as it only affects the anodized coating. Instead, we should use a chemical etch for one minute. One sample was run using this method. The part was still glossy and now had texturing on the surface.
I have now been told that a satin mask and glass bead blasting would be the best route to achieve a matte finish. I was already concerned about the consistency of a glass bead blast and more so after reading some of the comments above.
Could anyone provide any recommendations as to how we can achieve a consistent matte finish? We originally expected that the 8625 spec was going to keep us safe, but this appears to be far from the truth.
Thanks
- Hartford, Connecticut USA
A. Hi Jeff,
Personal experience suggests either a 15-20 second dip in a 10% caustic solution (not for very close tolerance parts) or wet abrasive blasting immediately prior to anodizing. You may also consider rotary finishing.
Aerospace - Yeovil, Somerset, UK
July 24, 2017
Graphics:
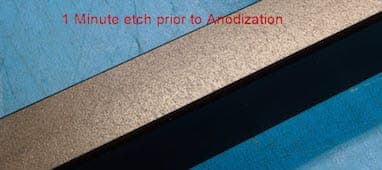
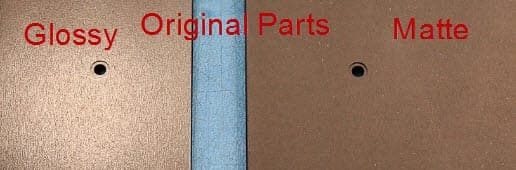
A. Chemical etching with a caustic solution does actually produce a very nice matte finish on 6061. Is it possible that your glossy sample was simply not etched for long enough to produce a matte finish? I have found that the longer the part sits in the caustic etch, the more matte it becomes. However, this does affect the tolerances on the parts as the etch will eat away some of the aluminum surface, so be wary.
I would suggest having some sample parts ran for a longer duration (or a bit hotter) in the caustic etch and seeing what the results are. You might find letting them sit a bit longer in etch will work well to produce a matte finish!
- Bozeman, Montana, USA
November 20, 2017
Q, A, or Comment on THIS thread -or- Start a NEW Thread