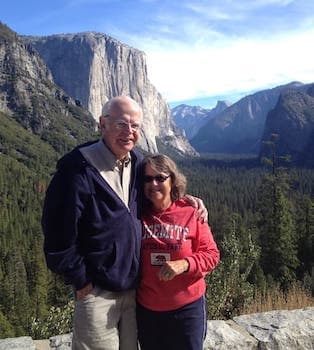
Curated with aloha by
Ted Mooney, P.E. RET
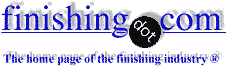
The authoritative public forum
for Metal Finishing 1989-2025
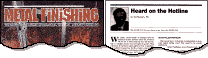
-----
Electrical difference between Nickel Flash and Silver Flash
I need to have copper bus bar finished to prevent corrosion. The bars carry a very high DC current load. Is there an appriciable difference between Nickel and Silver Flashing.
Michael Riceelectronics - Brookfield, Connecticut
2006
Hi Michael,
Silver is a better conductor, but is not corrosion resistant. In flash or strike plating thicknesses the copper will migrate through the silver in no time, especially with high voltage loads. Have you considered electroless Ni or Ni sulphamate plating. You will have higher electrical contact resistance, but much better corrosion resistance with Ni. Good Luck!
Process Engineer - Syracuse, New York
2006
The term "flash" is used in the (costume)jewelry industry to indicate a coating that is thick enough to colour the part but has practically no measurable thickness. Alternatively it is a very thin coating applied to ensure adhesion of the main coat as in strike plating. It has no place in specifying an engineering coating and would offer no corrosion protection.You will need a reasonable thickness of whatever you choose say 10 microns minimum.
For your application, corrosion resistance depends on what the corroding atmosphere is. Neither coating has any measurable effect on the main conductor which is dependent on the cross section area of the copper busbar. If you need good contact resistance, silver may be marginally 'better' but with good contact pressure, I doubt you will detect a difference.
In view of the cost of silver, you would need a very good reason to choose it.
If you have the option, electroless nickel has very good corrosion properties in many environments.
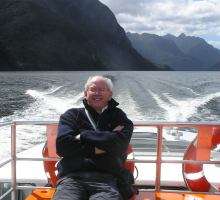
Geoff Smith
Hampshire, England
2006
Q, A, or Comment on THIS thread -or- Start a NEW Thread