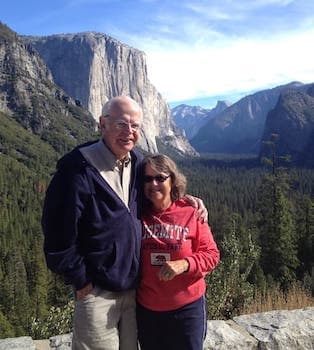
Curated with aloha by
Ted Mooney, P.E. RET
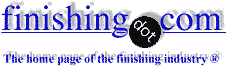
The authoritative public forum
for Metal Finishing 1989-2025
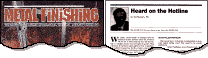
-----
Roughness problem in acid zinc plating
Q. Good Day
I operate a 25 gal acid zinc bath. Plating results have been great up until recently. After 4 days idling I have suddenly developed an issue where i am getting a very fine "powder like grit" texture on the parts, some parts more than others in both rack and barrel.
I run constant pp filtration and agitation, titanium basket is full, temp is 30 °C, pH 5.6. parts are cleaned very well.
Things I have noticed for quite a while now but still with great results are the bath is rather cloudy and when mixing carrier with solution prior to adding to bath it turns white and leaves behind a sticky white sludge in the mixing container; I also notice a lot of boric crystallization.
I have tried treatment and adjustment using hull cell, carbon filter, potassium permanganate, hydrogen peroxide, addition of carrier and brightener, same results.
interestingly there are some parts that the problem is not produced.
thank you
- Miami Florida
February 7, 2024
Ed. note: We appended your inquiry to a very informative thread on the subject. Please address the problem as suggested and get back to us with remaining questions.
⇩ Related postings, oldest first ⇩
Q. I am in charge of an electroplating facility that provides zinc electroplating (acid chloride) service to our customers. One of our customers recently rejected our components due to roughness of the surface. We are suspecting that poor filtration or a high boric acid might be responsible for causing this roughness. We are still getting components with roughness and looking for ways to resolve it. Any comments will be highly useful.
Prabha SamuelElectroplater - Chennai, Tamilnadu, India
2004
for Shops, Specifiers & Engineers
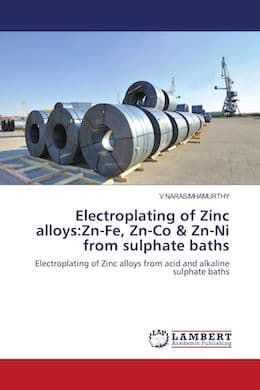
from eBay, AbeBooks, or Amazon
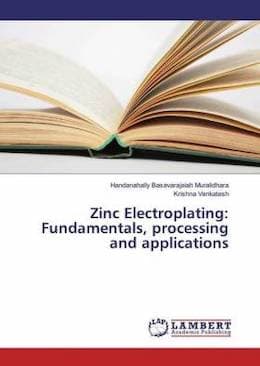
from eBay, AbeBooks, or Amazon
"Alkaline non-cyanide zinc plating with reuse of recovered chemicals" by Jacqueline M. Peden (1994)
from (U.S. EPA)
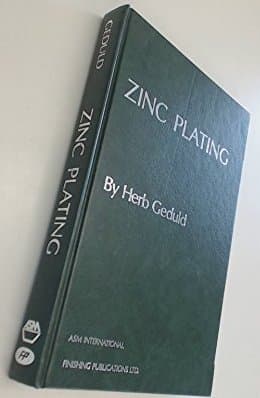
from eBay, AbeBooks, or Amazon
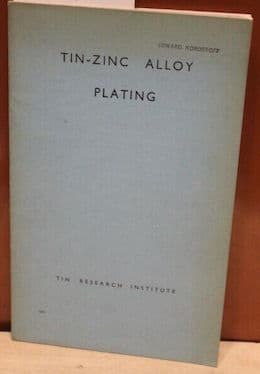
from eBay, or AbeBooks
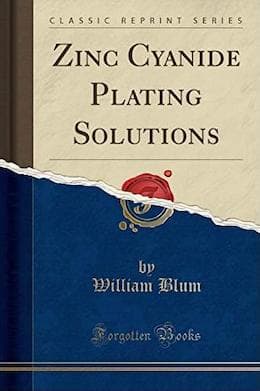
from eBay, AbeBooks, or Amazon
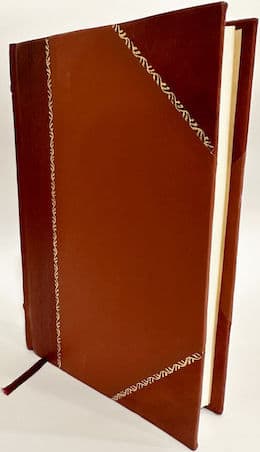
from eBay, AbeBooks, or Amazon
(as an Amazon Associate & eBay Partner, we earn from qualifying purchases)
A. If you have more roughness on the top, (as plated) it is definitely a filtration problem. A simple analysis will tell you if you have a boric acid problem or any other chemical imbalance. You might have magnetic parts holding some very fine particles to the part. Fix the problems one at a time and you will find out which one was the cause of your rejects.
James Watts- Navarre, Florida
A. Ms Samuel,
Continuous Filtration is necessity number one for acid zinc Plating. You need to check that pH is not higher than recommended. Older systems run well at 4.4 - 4.6 pH. The new Generation systems accept air agitation and work really well at 5.4 pH. The roughness experienced must be attended to with a filter.
Regards,
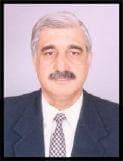
Asif Nurie [deceased] [deceased]
- New Delhi, India
With deep sadness we acknowledge the passing of Asif on Jan 24, 2016
A. Ms. Samuel,
Indeed, you have a filtration problem. Check the filter, first, your boric acid pH second.
- McAllen, Texas
A. PRACTICALLY I HAVE NOTICED THIS TYPE OF PROBLEM,
COVER ZINC ANODE WITH P.P BAGS
USE GOOD QUALITY PADS IN FILTER
USE GOOD CHEMISTRY
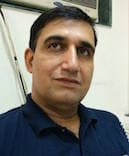
Ajay Raina
Ludhiana, Punjab, India
Q. Dear Sir/Madam,
My name is Kevin Chamberlain. The problem we have is that the work we are plating on our acid zinc vat line is coming off with a rough feel to it and an iridescent look to it before passivating.
We are running the pH at around 5.2, although it was quite low previously (4.5-4.9). We had high brightener content but have added the necessary wetter to balance this out. We have also added ammonia
⇦ this on
eBay or
Amazon [affil links] and permanganate to achieve the pH level, which is currently stable. We are at a loss as to what else we can do, even after several chemists looking at it. I hope I have explained this well enough and sincerely hope you can help. Thank you for your time spent on this matter.
kind regards,
- Birmingham, W.Mids, England
2006
A. Adding wetting agent is not going to offset a high brightener content as it is still there. Did you filter the solution after the permanganate add? If not or if not a long enough time, the roughness is probably coming from the particulates oxidized by the permanganate and the manganese oxide breakdown material. If it were mine, I would do a carbon treatment and then tweak the brightener and wetting agents by lab test results, correct the pH and do some hull cell plates. If that works, I would restart production. Shipping marginal parts is long term worse than late parts in most cases.
James Watts- Navarre, Florida
A. Hello Kevin Chamberlain,
I can't quite picture the high pH that you have been trying to achieve, normally 4.5 works just fine. The water topping up is generally good enough to raise pH levels.
Please bring it back to 4.5-4.8.
Reduce Metal and Boric Acid content to about 20 - 22 grams per liter and ensure your chloride is around 125.
Stop adding all additives for about 5000 Amp-Hours and you should be fine.
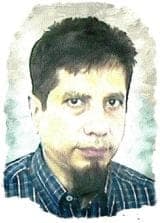
Khozem Vahaanwala
Saify Ind

Bengaluru, Karnataka, India
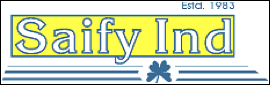
A. Is your bath an Acid Chloride Bath? If it is, I would not be using ammonia or permanganate for adjusting pH. Try using Hydrochloric acid to lower and sodium hydroxide to raise ph. You may be getting that effect from the reaction of iron and ammonia, co-deposition. The permanganate will precipitate your iron out of the bath. The roughness would be caused by either high boric or the tops of your anode bags are lower than solution level. Hope this helps a little.
JEFF W LENTZPlating Co. - Lancaster, Pennsylvania
A. Hello Kevin
Your priority should be to remove roughness. Try these:
1. Remove all anodes/bags; clean, change torn anode bags
2. Look for excessive sludge which comes up during air agitation -- idle the tank for 1 hour and decant
3. Clean filter and put in fresh filter paper and restart.
4. Reduce air at/near anode/anode bags.
5. Clean bus bars
6. Try plating on a plain MS sheet for 10 minutes (not corrugated). Ignore mild roughness. Start plating.
You will solve your problem of roughness.
Do not add permanganate in the bath unless it is very essential. And never to adjust the pH! Permanganate is added to remove iron. Hydrogen peroxide also does the same job and is much safer as continuous addition of permanganate leaves undesirable manganese in the bath and interferes in the deposit properties of plated items. For pH adjustment, use dilute Hydrochloric acid only.
Do not bother about excess brightener since you do not face any problems with receptivity of passivations or pitting. But As Mr. Vahanwala said, and as you know, there is excess brightener for sure. Why do you not stop adding for one or two lots!
A carbon pack in the filter and run it for 3 hrs and clean and re-start without carbon will bring back your bath to normal.
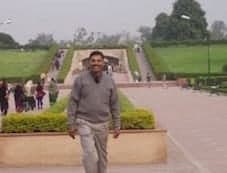
T.K. Mohan
plating process supplier - Mumbai, India
A. You have seen many good suggestions, some I agree with and some not. Firstly, the matter of adding more wetter to make up for high brightener. The wetter may be only that or in some systems it is really a carrier. In two-part brightener systems for chloride zinc there is generally a component called Starter, Carrier, Make Up or Wetter (nomenclature depends on vendor) and brightener or maintenance. Some systems actually have a surfactant additive called wetter which is truly one. If yours fits the earlier category, then yes, adding more will help with high brightener because the brightener is not water soluble and the solubilizer is contained in the wetter. The problem with this is that you reach a point where you are high in total organics and drag over an oily film. The cure for this is peroxide or preferably permanganate treatment in a holding tank although lighter treatments may be done in the plating tank with filtration. When solution is clear, then carbon filter. You can also get some roughness from low levels of chromium contamination. Your supplier should be able to check this for you.
From a mechanical standpoint, the most frequently overlooked area is the low pressure air blower (you should not be using air from a compressor!). This blower should have a filter on the air intake as well as one in line. Check to see if these are there and in good condition. If not you can keep cleaning the tank but the air line will keep adding particulates.
Follow what the others said but you also might want to look at your work after electrocleaning. Sometimes small metal fines may be adhering to the parts and are then exaggerated in the plating process as roughness
process supplier - Great Neck, New York
A. Kevin Chamberlain,
The pH of the bath is very high. Please bring the same to pH 4.5 to 4.7.
Metal and Chloride ratio should be maintained 1: 4.5 to 5 ratio.
The roughness can be caused because of High brightener content.
Anode dissociation is more. Please check the anode condition.
High Current density can cause the problem. Please maintain 10 to 20 ASF.
To reduce the pH use HCl - LR Grade.
Thanking you.
- Bangalore, Karnataka, India
February 20, 2014
Q. I have been having a problem with roughness in an acid zinc chloride bath. I had to use an electron microscope to figure out the roughness being deposited on the parts was 100% zinc.
The parts coming out of the plating bath are having little white rough spots being deposited on the part. I change filters everyday, have carbon filtered the bath, and have anode bags.
I can add some of my supplier's starter to the bath and it seems to minimize the problem.
The odd thing is that I am only getting this problem on 2 out 5 plating baths that use the same inputs.
I have been thinking that since I plate zinc die cast parts in the baths that have a rough deposit that these parts could be the culprit.
Does anyone have any ideas on what I could do to solve this issue.
- Houston, Texas, USA
November 10, 2013
A. Change the anode, use always high purity anodes. Remove existing metal contamination with oxidation and reduction treatment using potassium permanganate ⇦ this on eBay or Amazon [affil links] and zinc dust ⇦ this on eBay or Amazon [affil links] .
pandian sakthi- madurai, Tamil Nadu, India
Operating a ZnCl2 plating bath without HCl
Q. I want to lower the pH to an acid bath for Zn (ZnCl2) electroplating (from 6 to 5.5). Since the use of HCl is not allowed due to government regulations (Drugs problem), I want to know an option to HCl; I tried H3BO3 but it does not work very well (the pH change just a little 0.01 units around), HBr (is so expensive).
I really appreciate it if someone can help me.
- Gutta, India
September 25, 2020
A. Hi Jamal. You must either be misunderstanding the regulations or have failed to obtain necessary permits because the idea of operating a plating shop without HCl is preposterous :-)
Luck & Regards,
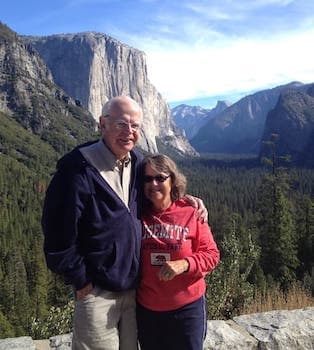
Ted Mooney, P.E. RET
Striving to live Aloha
finishing.com - Pine Beach, New Jersey
Q. Hello,
I am Tudor Sibianu, and I provide technical support to the clients for the company I work for. At a client which uses weak acid zinc plating, some parts exhibited rough deposits on their surface.
Upon closer inspection, I noticed that the most probable reason would be the nature of the substrate because it is rougher than other parts. Some operators, claimed that it would be the fact that they do not add zinc chloride to the solution. Personally I do not see the point of adding zinc chloride since the concentration of zinc is maintained by the anode dissolution and the chloride concentration by adding potassium chloride.
My question would be:
Can the lack of addition of zinc chloride cause rough defects?
Can the lack of addition of zinc chloride have any unwanted side effects to the plating bath?
- Bucharest, Romania
January 11, 2021
A. Hi Tudor. You could certainly be right that the cause of roughness after plating is roughness before plating, although it's difficult to assess what may be wrong from a single symptom. And you are certainly welcome to solicit answers to your questions about zinc chloride additions, but some people do make ZnCl2 additions, and I don't think your questions are precisely the best questions for the situation :-)
Firstly, what needs to be known is the condition/concentrations of the plating tank, rather than whether or not zinc chloride was added in place of sodium chloride. Secondly, the best way to determine the need for additions and how to make them is to follow the Technical Data Sheet from the process vendor.
What I'd actually suggest if you are considering the plating process to be a possible cause of the roughness is running a Hull Cell panel. If you see HCD roughness extending too far from the edge, various things like low zinc concentration could be causing burning. It's also possible that the roughness is from particulates, such that you might want to determine where on the part and where on the rack the most and least roughness occurs.
One thing that wasn't mentioned is bailing out the contents. Acid zinc baths usually grow in volume, so partial contents must sometimes be bailed out. You might want to investigate what condition signals the need for bail out and what other operations/adjustments go along with this periodic bailing and if they contribute to the problem.
Best of luck permanently fixing it if the operators remain convinced that zinc chloride additions are needed, and you remain convinced that that they're not :-)
Luck & Regards,
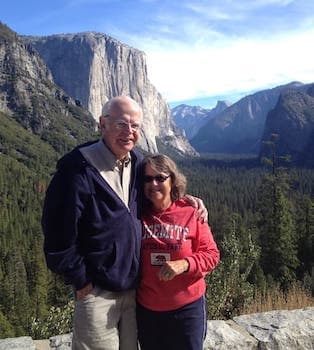
Ted Mooney, P.E. RET
Striving to live Aloha
finishing.com - Pine Beach, New Jersey
Multiple threads merged: please forgive chronology errors and repetition 🙂
Q. Hi there!, guys our company is about to open an acid zinc electroplating plant so here we are trying to get information about the system. The question is how important is a filter system to clean out zinc bath, what is more important, salt precipitates or organic traces? Do we really need activated carbon filter or it could damage the action of the organic brighteners?
Thank you all!
- Sinaloa, México
September 29, 2021
A. Hi Jorge.
Yes, filtration is essential to remove metal fines, salt precipitates, shop dirt, iron, precipitated boric acid, kicked-out carrier/wetter, etc.
As for carbon filtration and organics, primarily you should rely on what your supplier says because, although carbon filtration can remove brightener breakdown products, some addition agents can be inadvertently removed by carbon filtration. Further, simple continuous carbon filtration may be insufficient to remove a build-up of undesired organics, and you will probably need periodic permanganate oxidation and batch carbon filtration.
Please search the site for "acid zinc filter" for a number of good discussions on the topic (Google prohibits us from 'preloading' search terms into the search engine for you).
Luck & Regards,
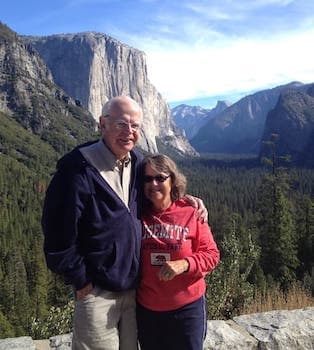
Ted Mooney, P.E. RET
Striving to live Aloha
finishing.com - Pine Beach, New Jersey
Q, A, or Comment on THIS thread -or- Start a NEW Thread