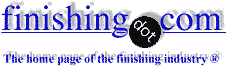
-----
Electroless Nickel Plating Versus Nickel Electroplating
One of our components we make is electroless nickel plated per
MIL-C-26074
[⇦ this spec on DLA], CLASS I. The plating thickness is about 0.0003" to 0.0005". The plating solution is ALLIED-KELITE SOLUTION # 794. The part we plate has a square surface area of about 0.5" x 0.5" and a thickness of 0.10" with a small flange of about 0.006" thick. This part resembles lid of a cup.
Currently, we LASER WELD this component to a "cup" of about 0.013" wall thickness (Material: 30% Cu 70% Ni Alloy). During laser welding, we noticed some "sparks" coming out from the welded joint (like a
"fire comet" somebody mentioned in this panel discussion). This spark is traditionally attributed to some contamination. Some laser welding experts believe that the contamination could be coming from the plating. Which process has less impurity: Electroless Nickel plating or Nickel Electroplating. If Electroplating is the answer, then, Could electroplating meet our plating thickness requirements.
I would appreciate your answer. I beg your apology for my lack of knowledge on plating technology.
communications-electrodynamics - Chicago, ILLINOIS, USA
2006
As far as contamination, there is no definite answer. Both processes may have some degree of contaminants. But keep in mind that EN is a nickel alloy, most frequently with 6-10% phosphorous depending on bath formulation, whereas electronickel is essentially +99% pure nickel and minute traces of gasses, other metals or salts. It is also well known that EN is not a good substrate to weld on due to its phosphorous content. Whether this is causing your problem I don't know.
Guillermo MarrufoMonterrey, NL, Mexico
2006
Provide plating bath not contaminate with organic and/or metallic impurities, then nickel electroplating should give a higher purity of Ni deposit (99.9% or above Ni) than electroless Ni. Electroless Ni deposit usually contains phosphorous between 3-12% by wt.
You can apply electroplating nickel to get various nickel thickness by adjust current density and plating time. However, a disadvantage of electroplating compare to electroless is uneven thickness distribution affect by different current density locate at different area of your plating part.
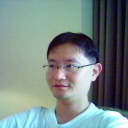
David Shiu
- Singapore
2006
The phosphorous (6-9 wt% P in Niklad 794) in the EN makes the fireworks. Metallic phosphorous is used in incendiaries. Very dangerous, so modern matches use phosphorus sesquisulfide, P4S3.
Ken Vlach [deceased]- Goleta, California

Rest in peace, Ken. Thank you for your hard work which the finishing world, and we at finishing.com, continue to benefit from.
2006
Q, A, or Comment on THIS thread -or- Start a NEW Thread