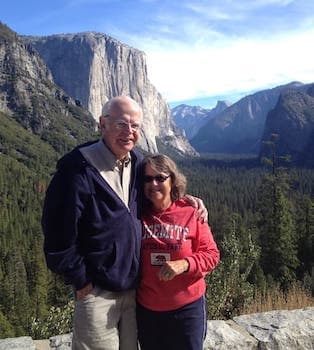
Curated with aloha by
Ted Mooney, P.E. RET
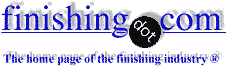
The authoritative public forum
for Metal Finishing 1989-2025
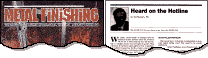
-----
Zinc Whiskers in a Data Center - Pregalvanized, Hot-dipped Galvanized, Electroplated Zinc?
Looking for a resource(s) to clarify fact versus fiction regarding the formation of zinc whiskers. What is the optimal finish when deploying cable basket in a Data Center environment, i.e. pregalvanized, hot-galvanized, or electroplated zinc?
Robert Steeleconsulting - Columbus, Ohio
2006
I don't know where to find the resource, but I believe the answer is hot dipped galvanize :-)
Electroplating, whether it is called plating or whether it is called electrogalvanizing, does introduce stresses that serve as the energy source to power the formation of whiskers. Pregalvanized is probably okay except that you need to be clear that it was hot-dipped not electroplated.
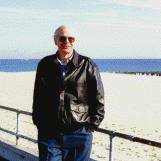
Ted Mooney, P.E.
Striving to live Aloha
finishing.com - Pine Beach, New Jersey
2006
August 6, 2012
That's a fine hypothesis - that HDG finishes are whisker free and that whiskers are caused by electroplating "stress".
Except the rocket scientists at NASA have a VIDEO of whiskers on HDG coated steel here:
http://nepp.nasa.gov/whisker/video/Zn-whiskers-HDG-electrostatic-bend.wmv
And according to those same rocket scientists, we aren't quite sure what causes the whiskers other than having (in the case of zinc whiskers anyway) a zinc coating.
Sadly, there is a HUGE amount of misleading information on whiskers on the web. Various companies' marketing groups have published all sort of unsubstantiated claims about how their products are whisker free because ________ (fill in the blank). But the ONLY sure way of being whisker free (again in the case of zinc whiskers) is being zinc free.
I STRONGLY encourage anyone interested in UNBIASED fact to visit NASA at the link above.
Additionally, if you have trouble viewing the video linked in my last post here, here's a great powerpoint type presentation in pdf format from our UNBIASED sources at NASA showing zinc whiskers growing on hot dipped galvanized steel pipe.
http://nepp.nasa.gov/whisker/photos/hdg-pipe/HDG-zinc-whiskers-pipe-panashchenko.pdf
Clearly, the ONLY way to avoid zinc whiskers is to AVOID ZINC!!!
- Coral Springs, Florida, USA
A. Hi Greg. Thanks for the update! The realization that zinc whiskers can be a problem is relatively new, probably growing in importance over time due to increased miniturization. We all knew about tin whiskers for many decades because they shorted out circuit boards. As things got smaller, whiskers from their zinc plated enclosures and computer room floors eventually became a failure mode. My understanding is that a patient on a heart apnea monitor died, it was blamed on zinc whiskers -- and that made them the next big thing.
Some (perhaps not all) of what you interpret as "BIAS" (your caps) is simply the normal process of discovery. I, for example, am from the electroplating industry, and when I promoted galvanizing over electroplating for the given application back in 2006, it was because that was my understanding -- certainly not 'BIAS', which would have leaned me the opposite way.
I do know that acres of zinc plated computer room flooring were removed and replaced with galvanized. But by 2009, I believe that people were less sure about that course of action being a total solution (letter 6243)
Both references that you supplied are from Jay Brusse, who wrote on our site in letter 17008 in 2004 that:
"While the empirical information that can be found 'publicly' states overwhelming that zinc whiskers are limited to finishes applied via 'electroplating' and that 'hot dip galvanized zinc coatings' are immune, we have heard some rare reports of zinc whiskers forming on 'hot dip galvanized' surfaces as well."
It isn't clear to me from your references whether Jay still considers zinc whiskers from galvanizing "rare" or now feels they are common.
Regards,
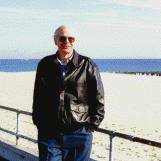
Ted Mooney, P.E.
Striving to live Aloha
finishing.com - Pine Beach, New Jersey
August 7, 2012
A. @Ted
I find a very large number of companies building products for data centers claiming "zinc whisker free" products due to hot dip galvanizing or "pre-galvanizing" (which we know is typically hot dip type process). I then find a great many people who have read the marketing of said companies and then subscribed to their statements as true.
Mr. Brusse I have found to be a tremendous resource to anyone seeking information on this topic. I believe he was the author of both the video and pdf to which I linked earlier.
I was not accusing you (Ted) of making false claims regarding zinc whiskers, but at most of being victim to the false claims made by others. Google around a little and you will quickly see what I mean and why I suspect the original poster wanted an unbiased opinion.
I would think that any evidence of zinc whisker formation would be enough for me to avoid use of that product in a data center. With site recommendations from ASHRAE co-authored by AMD, Cisco, Cray, Dell, EMC, Hitachi, HP, IBM, Intel, Seagate, SGI, and Sun (http://www.eni.com/green-data-center/it_IT/static/pdf/ASHRAE_2.pdf) warning against zinc whisker contamination in the DC, and newer still ASHRAE recommendations reiterating the position (http://www.ashrae.org/File%20Library/docLib/Publications/Errata/2011-Gaseous-and-Particulate-Contamination-Guidelines-For-Data-Centers.pdf), I would avoid all potential sources. Period. If there is a proven source, avoid it. What does it cost if a $100,000 switch fails and the manufacturer invalidates my warranty over the finish on my floor system?
Is there any reason to choose a zinc hot dip galvanized finish over a powder coated finish in a data center when the powder is in most cases less expensive? Knowing an alternate finish which contains zero zinc exists and exists at equal or lower cost, why even consider taking the risk?
And virtually everything in a DC which is available with a zinc coating is also available with powder coat. Conduit, strut, cable tray, etc. The only place costs rise is in hardware such as nuts/bolts where nickel or stainless steel finishes do cost more than zinc. Also note there is evidence that cadmium finishes will also whisker.
- Coral Springs, Florida, USA
Hi again. As we've emphasized hundreds of times in this forum, finishes are never picked on the basis of how well they match one given parameter, but which finish is the overall best fit for the given situation. If zinc whiskers in data centers are being found to be caused by a given finish, it becomes a serious requirement that the finish should be avoided, and that may override other issues like nickel allergy. If it's one-in-a-million hypothetical situation, that's something else.
There seems to be very little question that zinc electroplated flooring was a major issue. My question is, with all the acres of zinc plated flooring that were replaced with galvanized flooring, whether there are any case histories or other data at all showing that any galvanized floor has been an actual problem in a data center? I'm not implying that they aren't -- I just haven't heard that they are, so I'm asking.
Regards,
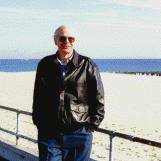
Ted Mooney, P.E.
Striving to live Aloha
finishing.com - Pine Beach, New Jersey
August 9, 2012
A. Sirs:
In forty years working with HDG I have never heard of or seen zinc whiskers. From Google using: zinc whiskers hot dip galvanizing you can see the video of zinc whiskers inside a HDG tube. I e-mailed Jay Brusse at NASA and he sent an article:
Journal of Applied Surface Finishing, 2 (1), 15-19 (2007).
In this article the authors state for HDG:
"The dull areas grew long whiskers but the bright areas did not."
"...surface corrosion by chlorides favor whisker growth...."
"HDG filaments are rough and contain iron and thus are brittle and prone to breakage."
"To grow whiskers, the specimens were placed in an oven for 24 hours at a temperature of 170 °C."
For HDG the filaments contain between 0.29% and 0.50% iron.
In the pit area (base of filaments) the EDX shows zinc, carbon, oxygen, aluminum, silicon, sulfur, chloride, and potassium. The aluminum is likely in the zinc. The silicon and sulfur are likely in the steel. The potassium and chloride are likely in the flux.
It has been suggested that zinc whiskers can be "grown" faster by heating the galvanized sample at 170 °C for 24 hours. In freshman chemistry one is taught that every 10 °C higher temperature approximately doubles the rate of a reaction. Thus at 170 ° C the rate of whisker formation will double 15 times. Mathematically this is 2 raised to the 15th power which is: 32,768 (times faster). In other words 24 hours at 170 ° C is the same as 32,768 days at 20 ° C. 32,768/365 = 89.8 years. I certainly do want to try to "grow" zinc whiskers. Nearly all researchers working on whiskers agree that there is NO reliable test to predict when whiskers may appear. There is a chemical problem in using 170 ° C, which is: At 170 ° C this may be above the Ea (activation energy) of the chemical reaction which indeed may not even occur (ever) at 20 deg. C.
A few days ago I e-mailed Jay Brusse (NASA) and he promptly replied. He indicated that the HDG pipe sample in the youtube video is 20 or more years old. Thus it takes time (or perhaps heat) to form zinc whiskers. He also said that he found about 2% to 3% of 2 inch diameter galvanized pipes in a hardware store having zinc whiskers. This morning I went to the local hardware store and in 2 inch elbows, I found (maybe) one or two that perhaps had one or two very small areas of a few whiskers (or lint). Perhaps the two inch size is more likely to have whiskers because they are stored in the hardware for a long time.
All of the straight electrical "HDG" conduit was "flow coated" on the outside and zinc rich painted on the inside.
It is known in electroplated zinc steel that whiskers do NOT form if a chemical brightener is not used. Thus it is likely that there may be a way to prevent whiskers in HDG if this is a problem. Naturally even one case of computer or electronic failure is one case too many.
There is a company that specializes in fixing the whisker problem. This company needs to be contacted to determine how bad a problem it may be in HDG.
Regards,
Galvanizing Consultant - Hot Springs, South Dakota, USA
Q, A, or Comment on THIS thread -or- Start a NEW Thread