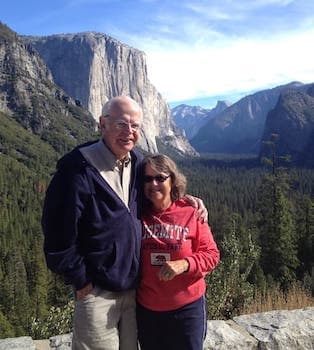
Curated with aloha by
Ted Mooney, P.E. RET
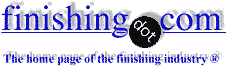
The authoritative public forum
for Metal Finishing 1989-2025
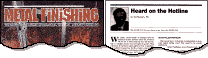
-----
Nickel Underplating Thickness for Gold-Tin Solder Bonding
I am facing a solder wetting/bonding problem. Basically, my part is plated with Gold (60-80 microinches)over a 80-160 microinches of nickel underplate. After some heating process, the gold becomes slightly dull and when a solder (Gold-Tin)is applied over the plated surface, the wetting/bonding is poor. What could be the cause of this? Should I reduce or increase the nickel underplating thickness to promote better solder wetting/bonding?
Any suggestions or help are welcome.
Manufacturing - Singapore
2006
To have a good solder joint, solder must able to form a thick enough intermetallic layer between nickel and solder during soldering. Gold deposit used to protect underlying nickel from oxidation/corrosion which will affect solder joint formation. During soldering, gold will dissolve into solder first before solder can reach nickel to form intermetallic layer. Should gold thickness too high, lots of energy will consume on dissolving gold which in turns hinder nickel-solder intermetallic formation.
For your case, I would suggest you to reduce gold thickness to ~10-20 microinches (if no other concern like gold wire bonding requirement, etc) which is more than enough to protect nickel from oxidation/corrosion. Besides that, you should also verify reflow profile (temp and timing step) and nickel plating (organic/metallic contamination, etc) which could cause de-wetting as well.
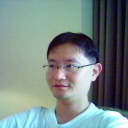
David Shiu
- Singapore
2006
2006
Thanks for your recommendations. Although the surface (at which the Gold-Tin solder is applied to) is not required for wire bonding, the whole gold plating over nickel is done for the whole product as a whole and other surfaces are indeed used for wire bonding. Therefore, is there any recommendation for the thickness of gold plating to cater for both wire bonding and Gold-Tin soldering?
How will the thickness of Nickel underplate affects the soldering? Will a thiner Ni plating aid the soldering or a thicker Ni plating? Please advise.
Thanks.
- Singapore
20-30 microinches gold deposit is good enough for gold wire bonding application. Nickel thickness ~3 microns is optimal for soldering as too thin Ni will result a faster Cu diffusion and too thick Ni will cause a higher internal stress in Ni deposit.
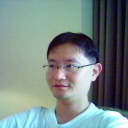
David Shiu
- Singapore
2006
Dear All,
I Am working on the diffusion and reaction mechanism between Gold-tin solders and selected under bump metallization. The UBM can be Nickel,platinum,Cobalt and Tantalum etc.Can any one help me to refer some articles or tell me about the reaction rate constants and diffusion constants for diffusion of these materials in Au-Sn and vice versa?
STUDENT - Goteborg, Sweden
April 14, 2010
Q, A, or Comment on THIS thread -or- Start a NEW Thread