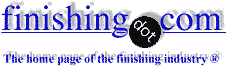
-----
Green residue on 410 stainless bolts
Q. Hi,
My question is regarding green residue identified by a lab as silicon oxide on 410 stainless bolts received from our supplier. I would like to know how this may have happened and if it will be detrimental to the bolts in the field. The parts are used in automobile applications and see road environments.
The process for the bolts is heading from 410 SS wire with an oxalate coating (no copper), oxalate removal, roll threads, heat treat, passivation (probably nitric acid) and bake to relieve hydrogen.
If anyone has seen this happen before or knows the later effects, I would be very interested in your comments.
Thanks,
Automotive Supplier - Chicago, Illinois, USA
2006
A. Silicon Oxide (sand) is not green unless it is mixed with a green nickel compound like nickel nitrate. I suspect the passivator is not rinsing well (especially threaded parts), leaving some nitric acid residue which combines with the nickel on the surface and leaves a green compound. The silicon is probably coming out of the steel but is probably not the source of the "green".
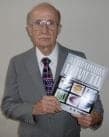
Robert H Probert
Robert H Probert Technical Services

Garner, North Carolina
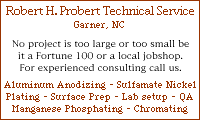
A. Seems like abysmal quality from an unqualified, low ball supplier.
If the parts were properly passivated, there is a problem with the baking. The oven may be contaminated with chlorides or fluorides (salt bath, pickling or brazing flux residue). These combine with moisture in the air to attack the passivation and cause green crystalline Cr2O3. Silica doesn't form on 410 SS unless drastically overheated, e.g., as slag on the liquid metal. Not much nickel in 410, either. Maybe silica from disintegrating oven insulation. Contaminants are prohibited under 'Workmanship and Finish' provisions, e.g., Para. 10 in ASTM F593, which also requires descaling and cleaning per ASTM A380
. And, why not hydrogen bake before passivation?
Oxidation from heat treating threaded parts in air depletes chromium and reduces the amount of metal in the threads, weakening them and reducing corrosion resistance. I advise heat treating in vacuum and using forced gas quenching (helium at 55 psia). Eliminates cleaning off quench oil and pickling of oxide scale; thus, no need for hydrogen bake-out. Tempered parts can be directly passivated Type II (or VIII) per QQ-P-35C (canceled) [link is to free spec at Defense Logistics Agency, dla.mil]C or the equivalent ASTM A967 Nitric 1 (or 4).
"passivation (probably nitric acid)" -- Making jokes or parts? What does the vendor's Shop Traveler show? Was rolling lubricant removed prior to heat treatment? Also check that the austenitization and tempering temperatures are correct for ASTM F593 P or R bolts, if applicable.
Unless the vendor comes up with definitive answers and verifiable Corrective Actions, blacklist them. If not feasible to vacuum heat treat, at least do the hydrogen bake-out after pickling but before passivation. Perhaps eliminate the hydrogen bake by minimizing hydrogen pick-up. E.g., anodic electrocleaning, pickling inhibitors and limited pickling time. Test for hydrogen in wire and bolts: load to 80% yield strength & wait 4 days for possible fracture. Torsion loading is better than simple tension.
- Goleta, California

Rest in peace, Ken. Thank you for your hard work which the finishing world, and we at finishing.com, continue to benefit from.
2006
Thank you both for your insights on this subject. I now have some extra info to push in the pursuit of legitimate corrective action. I also like the idea that there are other ways to process these parts that would be more reliable.
Here is a little more info....
The parts are over 34 HRC at passivation, hence the baking after passivation to relieve hydrogen.
The parts are not vacuum heat treated. The quench is listed as cooling air and natural air rather than an oil or other medium.
Passivation is nitric acid 22.5% by volume (Mil A-A-59105) and 2.6% by weight of sodium bichromate (Mil O-S-595)
We do test each lot for embrittlement features upon receipt.
Thanks,
- Chicago, Illinois, USA
Hi,
We have received a preliminary explanation for the green bolts (silicon dioxide deposit). The heat treater states that the parts are air quenched using NH3. An unknown contaminant was introduced into the process at this point creating the green residue. Of course we are looking for more answers regarding the source of the contaminant.
I am not sure if this makes any sense. Why would NH3 have an impurity that would cause silicon dioxide deposit? How else could it be introduced during the air quench?
If anyone has an idea, please post.
Thanks,
- Chicago, Illinois, USA
2006

this text gets replaced with bannerText
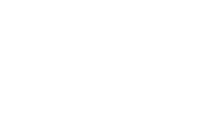
Q, A, or Comment on THIS thread -or- Start a NEW Thread