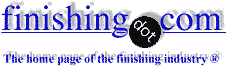
-----
Stainless steel corrosion
We produce 302 stainless steel rivets by cold-forming (from wire). The rivet is dipped in a liquid friction reducer at final stage of production,and then air dried with a heated fan.
A customer recently did a salt spray test (at 1000 hours) and found some parts with bad corrosion. Question:
1. Is it possible the friction reducer is causing corrosion ?
2. Would 302 stainless corrode at 1000 hours regardless ?
3. We have heard the suggestion that we should be passivating the parts, but we have not done this for the past 20 years !
Do we have a raw material problem, a coating problem, and how would it be best to eliminate the various possibilities ?
Rivet producer - Kiryat Malachi, Israel
2006
First of two simultaneous responses --
It could be from the wire and only salt spray test on a rather large sample would prove or disprove that. In my mind, it is probably coming from the cutting or the heading operation smearing a microscopic amount of iron on the rivet or from the die that is holding it. If you have to pass 1000 hours, you probably are going to have to passivate the parts.
James Watts- Navarre, Florida
2006
Second of two simultaneous responses --
May be you need a stress release after a cold work , or your drying fan is not heating enough .
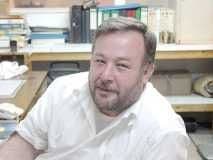
Khair Shishani
aircraft maintenance - Al Ain, UAE
2006
Q, A, or Comment on THIS thread -or- Start a NEW Thread