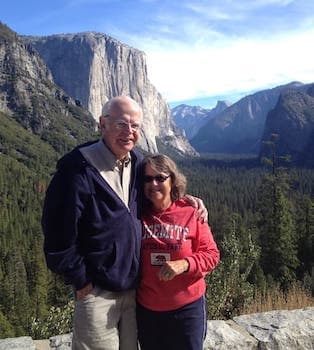
Curated with aloha by
Ted Mooney, P.E. RET
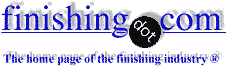
The authoritative public forum
for Metal Finishing 1989-2025
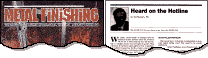
-----
Why do zinc coatings, why not other metals
Q. Dear All
I am working in continuous galvanizing line since 3 years. I want to know about how zinc coating works on sheet? Why we are using only Zn ? Why not use any other element?
Why we are applying chromic and oil on surface of GP sheet?
Give complete detail about ammonia
⇦ this on
eBay or
Amazon [affil links] cracker? And tell me the furnace inert atmosphere?
STEEL - GUJARAT, India
2006
A. Can it be that there is no-one in your company that knows why you do what you have done for at least 3 years?
Zinc is available, and common. It gives sacrificial protection to steel.
You put chromic on it to stop white rust.
Oil to lubricate and prevent initial oxidation.
Your furnace conditions could be quite different to those of others, so best ask at work.
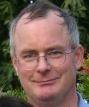
Geoff Crowley
Crithwood Ltd.
Westfield, Scotland, UK
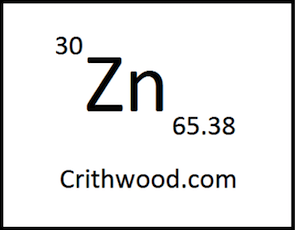
2006
September 2013
Hi cousin Amit. Here's a brief tutorial on the general topic of why we coat steel with zinc --
Most metals (all but the precious metals like gold) corrode. Usually we cannot afford to make things out of gold, and often the mechanical properties of gold don't meet the needs anyway, so we must make things of something else and coat them so we get the mechanical properties we need, and still get some corrosion resistance.
Steel is the most common metal to make things from because it is cheap and has great mechanical properties, but steel readily rusts. When it does rust, the corrosion product (rust) is loose, poorly adherent, and hydroscopic -- so the rust just continues. Some other materials like aluminum and zinc readily corrode initially like steel does, but under good conditions the corrosion products can be tight and adherent, and form an enveloping skin that can slow or deter ongoing corrosion.
Coatings on steel can be of two general types: barrier layer coatings and sacrificial coatings. Barrier layer coatings, like paint and powder coatings, simply seal the steel away from the environment. But when the barrier layer is scratched, wears away in one spot, or has porosity or pinholes, the steel will rust. Sacrificial coatings like zinc protect the steel not just with a barrier, but electrochemically. They are less "noble" than steel: so when corrosive effects try to steal electrons from the steel, which would cause that atom of steel to ionize to a positively charged ion and dissolve, the steel is able to take electrons from the zinc, causing the zinc to corrode instead of the steel -- and as previously mentioned, the corrosion products of zinc have at least some "sealing capacity" to protect the material from ongoing corrosion.
Actually there is an additional type of coating: a barrier layer coating of a metal like gold or nickel-chrome which is more "noble" than the steel. In this case, once the barrier is compromised, the steel attempts to sacrificially protect the coating. You may have seen nickel-chrome bumpers on very old cars or trucks where nothing is left but curls of the nickel chrome plating as all the steel eventually corroded trying to protect the nickel-chrome plating.
So, zinc coating is common because zinc is one of the few metals that is sacrificial to steel, and it is inexpensive, and it is relatively easy to apply, and it is non toxic. Cadmium plating meets some of those requirements but it is very toxic. Aluminum meets some of those requirements, but it is not as easy to apply (you cannot electrodeposit aluminum onto steel easily like you can electrodeposit zinc onto steel).
Regards,
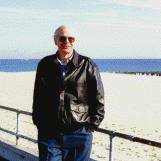
Ted Mooney, P.E.
Striving to live Aloha
finishing.com - Pine Beach, New Jersey

Q, A, or Comment on THIS thread -or- Start a NEW Thread