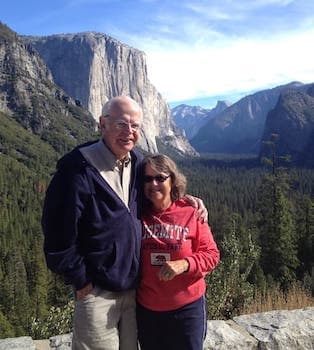
Curated with aloha by
Ted Mooney, P.E. RET
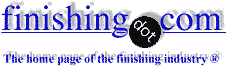
The authoritative public forum
for Metal Finishing 1989-2025
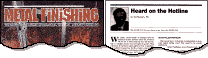
-----
Surface conductivity of zinc pre-plated steels with organic sealers applied
I am a mechanical engineer at Hewlett-Packard company. Prior to the RoHS initiatives, we have standardly used sheet steels for our electronic enclosures with pre-plate zinc (hot-dip or EG) and a hexavalent chromium passivation layer (clear chromate). Surface conductivity for these pre-plates has been consistently low and hence these preplates have been good choices for electronic enclosures that utilize fabric-over-foam EMC gaskets, since they can electrically seal seams and cracks in the enclosures with minimal forces and biting contact.
The sheet-steel manufacturers are shifting away from the hex-chromium passivations now that RoHS is in effect. Replacement of the hex-chromium passivation is ongoing at the moment as new methods and materials are invented, but it appears that most manufacturers are now using organic sealants (aqueous lacquer) and may also use a thick-trivalent-chromium passivation layer before the sealant is applied (ie: Surtec's trade name is Chromiting). With this new finish on pre-plate steels, the surface conductivity tends to vary wildly, and I am looking for possible alternatives that will provide adequate corrosion resistance (fingerprinting and high humidity rust) along with a consistently low surface conductivity. The steel manufacturers are not very forthcoming with the details and compositions of their platings since there is a lot of competitive maneuvering between vendors and the new RoHS-compliant technologies have a good bit of intellectual property involved.
What are your suggestions? If we were to use the Surtec Chromite passivation (trivalent chromium) without a clear organic sealer, will we have adequate fingerprint and rust protection? I understand that the plated steel would have a green iridescent color to it if no organic sealer is applied, but that may be ok if it provides the consistently low surface conductivity we are looking for. Are their other alternative that might work that we could partner with a steel mill to implement? Most of the steel mills tend to cater to the automotive industry, which prefers to maximize corrosion resistance and doesn't care much about surface conductivity.
Thanks,
Hewlett Packard Co - Fort Collins, Colorado, USA
2006
First I would strongly suggest you get coupons from vendors and perform tests to get actual numbers. Other than that I would presume that the conductivity of trivalent chromated zinc surfaces with a sealer will be lower than you found for hexavalent since most sealers are silicate based.
Gene Packmanprocess supplier - Great Neck, New York
2006
Q, A, or Comment on THIS thread -or- Start a NEW Thread