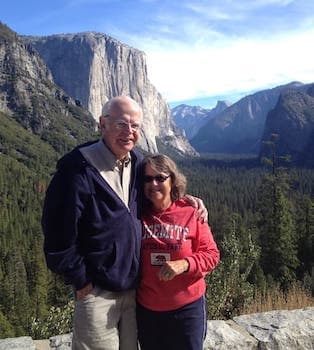
Curated with aloha by
Ted Mooney, P.E. RET
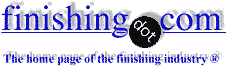
The authoritative public forum
for Metal Finishing 1989-2025
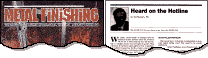
-----
Replacement coatings for cadmium, and hexavalent chrome?
Q. Hi folks,
I have a situation where a customer is using electroplated cadmium on ASTM A193 B7 bolts (AISI 4140) in an application operating at 600 °F. My examination of four of the 50 fractures reported shows cadmium on the fracture surfaces and along the grain boundaries of branches of the fractures. My assessment is LME of the steel by the cadmium. When I look through the literature, it appears that cadmium plating on stressed parts should not be used if the parts operated at over about 450 °F.
The customer says he has been using this combination for several years with no problems at 600 °F. My thinking is that this might be a lucky result of lower applied stress. For LME to occur three things need to be operating: a bad liquid/solid combination, operating temperatures that come at least close to the melting point of the lower-melting metal, and stress above a threshold. Perhaps the other installations do not have high stress? Any thoughts? I could use some feedback, since the customer is having some trouble believing that LME is his problem.
Thanks!
Senior Failure Analyst - Lansing, New York, USA
December 6, 2010
A. Hi Dave,
Based on your description, it sounds like a textbook case of LME. I'm assuming one of the references you consulted was the ASM Handbook Volume 1 section on embrittlement? As long as you are confident in detecting Cd on the fracture surfaces and the branched cracks, it sounds like the right conclusion. Your supposition about bolt stress is a good avenue for the customer to pursue, as other joint details like time at temperature, geometry variations, etc. Another area to investigate: prior austenite grain size and composition (S, P, As, Sb, Pb, etc.). Are the latest fasteners different in either aspect? Anything that reduces fracture toughness will make LME more likely, and ASTM A193 B7 can allow for relatively high levels of embrittling elements.
Automotive module & component supplier - Michigan, USA
December 6, 2010
Max temperature for Cadmium Plating
Q. Hey guys, I know cadmium plating is most often used in the aeronautics and marine industry however I think I have another use for it. I'm wondering at what temperature Cadmium is melted off of its component. Can it withstand temporary temperatures in excess of 800 °F for relatively short periods of time? For about an hour or two? Or will it melt/dust off? The properties of cadmium (corrosion resistance, namely) is not important during the heating process.
Thanks for any and all info!
- Austin, Texas
April 23, 2015
Hi John. It doesn't sound promising to me at all. We appended your inquiry to an earlier thread to offer you some insights into possible issues, but unless you say something about the intended application, it isn't possible to offer suggestions for alternatives.
You could perhaps consider nickel-cadmium diffusion coatings for their higher temperature resistance, but not having any idea what you plan, I can already hear the future screaming back at me: "What idiot suggested nickel-cadmium plating for that?!"
Good luck, and regards,
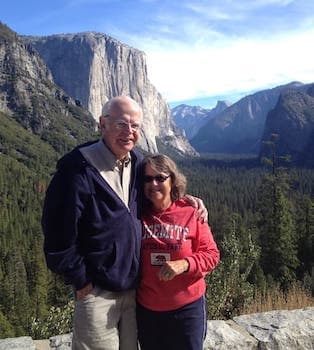
Ted Mooney, P.E. RET
Striving to live Aloha
finishing.com - Pine Beach, New Jersey
April 2015
Q. Hi!
It will be a mariner style coating for firearms. Its corrosion prevention, lubricity and low cost is what's drawn me in.
Thanks!
- Austin, Texas
April 24, 2015
A. Hi again. There are so many good firearm coatings from parkerizing to Tennifer (salt bath nitrding) to electroless nickel to hard chrome to molybdenum-based dri-lubes to ceramics, that to pick a toxic, biocumulative, RoHS proscribed, poor temperature resistance coating doesn't sound like a good way to go :-(
Luck &Regards,
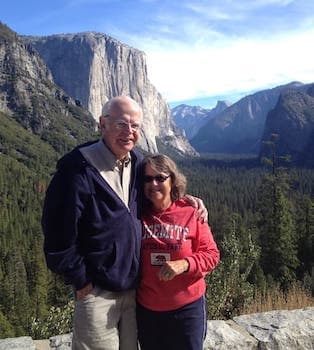
Ted Mooney, P.E. RET
Striving to live Aloha
finishing.com - Pine Beach, New Jersey
April 2015
Q, A, or Comment on THIS thread -or- Start a NEW Thread