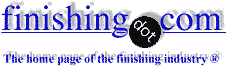
-----
Hard surfacing for abrasive wear resistance
2000
We are looking for a process that will economically improve the wear resistance of mower blades. The process needs to be economic for production quantities. Material Science, heat treating and coatings are not my specialty. Therefore I seek your advice.
The blades are currently 5150 or 10B38 steel heat treated (austempered) to RC 40-45. The processes I have investigated so far are: Boriding, ZrN, Tungsten Carbide brazing, and Hard chrome.
We want to end up with a blade that has the same structural properties as the current blade (provided by the substrate), improved abrasive wear resistance, and the ability to accept localize damage due to a strike without failure a larger area of the coating.
I am concerned about adhesion of the hardened layers with ZrN, Tungsten Carbide braze, and Hard chrome. I almost want to rule out Hard chrome due to hydrogen embrittlement. I have yet to see a plated part that can consistently avoid this issue on a production basis, and the results of a fatigue fracture on this type of part could be "very bad"
Boridizing sounds appealing, especially Borochromizing. Do you know any drawbacks to this outside of the processing issues? Do you have any contacts for Borochromizing?
Any suggestions for processes that I have not mentioned, issues with pre or post process heat treating that I need to be aware of, etc.?
Thanks for any input or suggestions you may have.
Mark
Mark Atterbury- Beatrice Nebraska
![]() |
We've been having great success increasing the life of metal cutting tools and threading dies by metal ion implantation. Basically, rather than coat the surface we use a beam of nickel and titanium ions to micro-peen it. The result is a very significant increase in the surface toughness that results in much greater wear resistance. Most of the treated parts last two to three times longer. The process is conducted at very low temperatures -- under 200 F -- and takes around thirty minutes, so there is no thermal distortion. As it is not a coating process, there is no adhesion problem and no change in tolerances. Sharp edges remain sharp. Hydrogen embrittlement is also not possible. ![]() Jim Treglio - scwineryreview.com PVD Consultant & Wine Lover San Diego, California 2000
My research into the use of coatings indicates that they are not a good candidate for your application. They are usually quite thin, and the mode of failure is that the metal under the coating deforms or cracks out. Try cryogenically processing the blades. This should increase the abrasion resistance of the blade considerably, an will increase the fatigue life as well. It will make the blade more tolerant to damage due to accidental strikes. F. J. Diekman- Streamwood, Illinois 2000 |
Thank you for your information. I have done some investigation into the cryogenic process, and this looks promising with regards to cost. The coating processes fall in at roughly $6-$20 per blade, where cryogenics are in the $2-$3 range. I may get in touch with you Jim if the cryogenic route does not pan out. Once again thank you for your information.
Mark Atterbury- Beatrice Nebraska
2000
Mark: When you try cryogenics, be sure that you get a true cryogenic process, not just the cold treatment that you can get from heat treaters. Get the blades down to -300 F slowly, hold at -300 F for a long time, and bring them back up slowly. Then be sure to temper them afterwards.
There are a lot of companies out there who do not do cryogenics correctly, and they are giving the process a bad name. I suggest that you contact the Cryogenic Society of America or ASM for information on companies.
Good luck.
Frederick Diekman- Streamwood, Illinois
2000
Dear Mark:
We suggest you look closer at hard chrome plating and its many benefits including abrasive wear protection. Hard chrome is cost effective on production quantities and a simple bake @ 375 F for a minimum of 3 hours will eliminate any hydrogen concerns.
Regards,
Steve Ward- Toronto
2000
Mark, Look into D-gun coatings. They have been used for a long time for commercial cutting blades.
Donald M. MattoxSociety of Vacuum Coaters
Albuquerque, New Mexico
"Handbook of Physical Vapor Deposition (PVD) Processing" (2010) [on AbeBooks or eBay or Amazon affil links]
and "The Foundations of Vacuum Coating Technology" (2018) on AbeBooks or eBay or Amazon affil links]
We currently heat treat blades made of 10B38 using a Austemper heat treating process. This process is one of the cheapest and robust processes. Depending on the size, the cost is less than $1.00.
Rich Ross- Wellington, Ohio
May 9, 2010
Q, A, or Comment on THIS thread -or- Start a NEW Thread