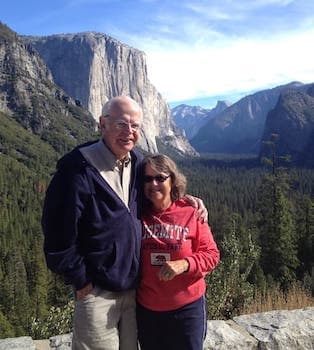
Curated with aloha by
Ted Mooney, P.E. RET
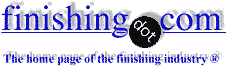
The authoritative public forum
for Metal Finishing 1989-2025
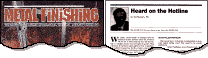
-----
Getting fine control of hard anodize thickness
Q. I have some parts in 6061-T6 aluminum that I would like to have hard anodized to resist corrosion in sea water. However on the "inside" of the parts (where there is no sea water exposure) there are some tight tolerance holes for bearing seats (diametrical tolerances of about ± .00025") that need to remain tightly toleranced after anodizing. I would like to be able to anodize the entire part without masking these bores, for simplicity, but in my experience (not a lot) it has been hard to achieve repeatable anodizing thicknesses from batch to batch.
So, the question is, how can you control the anodize thickness to within ± .0005 or better, and maintain consistency of this thickness from batch to batch? Or more specifically, what specific things can I tell my anodizer to help us get these results?
Larry Cheng- Mountain View, California
2000
A. The key will be process controls for the tank concentrations, the temperatures but most importantly have them run the loads by current density, (Amps per Square Foot) versus voltage, which is what I am assuming based upon the lot to lot variability you describe. Another key item is making sure the electrical current carrying capacity(racks and bussing) is sufficient for the current used. Proper racking is critical as is the placement of the cathodes and the anode(work) to cathode ratio.
Ward Barcafer, CEFaerospace - Wichita, Kansas
2000
A. Most hard anodize specifications call for a coating thickness of 0.0020", with a maximum variation of ±0.0005". Some specs allow as little variation as ±0.0002". The aluminum alloy 6061-T6 is normally regarded as a "good" alloy for hardcoating. With good processing techniques, (see Ward Barcafer's comments) it should be possible to meet your dimensional requirements.
Chris Jurey, Past-President IHAALuke Engineering & Mfg. Co. Inc.

Wadsworth, Ohio
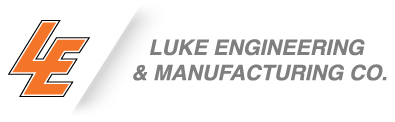
2000
A. Certainly the hardcoater has to control his process, as Ward says, to reproduce a consistent hardcoat. One could write a book on the number of things that could go wrong that the hardcoater couldn't reproduce a consistent finish.
But there are some other factors to be considered that you may need to consider. Some of those factors are hard to address without more specifics about the parts' dimensions, particularly the "inside" where there is a problem..You don't say what coating thickness you are expecting, but MIL-A-8625 / MIL-PRF-8625 [⇦ this spec on DLA]F calls for reproducibility for Class III of ± 20% of the nominal thickness. For a 2-mil coating, that is ± .0004". In my 16 years working for anodizers, though, we hardcoated many parts per blueprints that specified coating thicknesses of .002 ± .0002". With 6061 that shouldn't be a problem, unless you are looking for thicknesses higher than .002", where hardcoat voltages for 6061 go out of sight (assuming hardcoating is per constant current density), and inconsistencies can easily happen. I'm sure you realize by now that a .002" coating will shrink the I.D. by about .002". All this addresses exposed surfaces where circulation is optimum. If those holes are blind holes, inconsistencies might easily be expected, depending on the depth and the I.D.
How are you checking the coating thickness in these holes? If you are measuring the I.D. of the holes by micrometer, remember that the hardcoater isn't likely to improve on the tolerances that your machinists are going by. If the machinist holds the diameter to ± .00025", and the hardcoater holds the coating thickness to ± .00025", the total variation in the I.D.will be ±.0005". That is about as close as you can expect, that is, with a 2-mil hardcoat. Again, if these bores are blind, it may be difficult or impossible to hold these tolerances, especially if the depth is much more than twice the diameter. An auxiliary cathode could be used, but that could increase racking costs for the hardcoater dramatically. If you had to have anodize on these surfaces, I might recommend honing the coating to the proper I.D., but if you don't need anodize there, it might be cheaper to plug the holes. Of course, if you plug the holes, you need to bore the holes to a different dimension.
Phil Johnson
- Madison Heights, Michigan
2000
A. Please note a radial increase of .002 would give a diametral change of .004. But because anodizing is a conversion process, rather than a plating, half the anodize thickness goes above the original surface and half goes below. If you can live without the anodize in the bore, plugging the holes is safest, or you must hone out after anodizing.
Barrie Sawbridge- Montreal, Quebec, Canada
2001
Q. Dear friends,
Is the geometry of the part an important factor with respect to thickness of anodizing (hard anodizing)? We have different design of parts, we run the process with constant parameters for every cycle, but some of the parts get more thickness, so what could be the reason?
- Abu dhabi, UAE
November 11, 2014

Q, A, or Comment on THIS thread -or- Start a NEW Thread