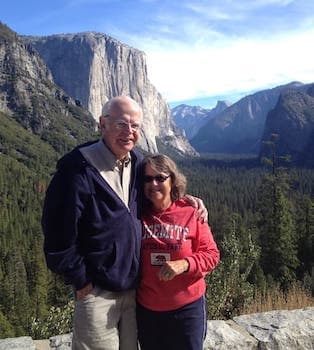
Curated with aloha by
Ted Mooney, P.E. RET
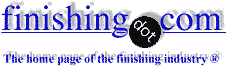
The authoritative public forum
for Metal Finishing 1989-2025
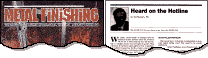
-----
Thermal dissipating/conducting paint for Electric Motors
Q. I am working as an electrical engineer in a steel industry. I have gone through a study on our electric motor (AC motor of more than 5 HP) failure analysis. I found that most of our motors fail due to excessive heat of their winding. As a result winding burns. You may say that heat dissipation rate is less than heat generated by our motor. When I went deep into this matter, I found that the PAINT which we use to paint our motor body is the real culprit as it is of normal type. This normal paint is acting as a blanket over the electric motor and thus restricts the heat dissipation rate, which eventually leads to winding heat up & finally the winding fails.
So I am looking for a thermal conducting paint, which we will use to paint our motor body. This paint must be really conductive so that it does not restrict the heat dissipation from the surface of the motor; as well, it should be able to keep our motor rust free.
steel industry employee - Jamshedpur, Jharkhand, India
2006
A. You fail to say what type of paint or how thick it is, so no one can tell you what might be better (as in better than what?)
If the paint is not excessively thick, changing the paint probably is not going to fix your problem. It sounds more like you are running the motor at less than placarded voltage, at least part of the time.
Also you might need to use a motor with a better cooling fan or less air restriction. You might have to go to a higher rated HP motor as it sounds like you are using this one at close to 5 HP (too close).
You might have to go to a nickel or zinc plated housing. Can you add fins to the motor housing? Even a few would help.
I know, you asked for a thermal conductive paint. Sorry, there are only minor differences. Thickness makes more difference.
- Navarre, Florida
2006
Q. Can we provide some coating/paint on the surface of electric motors which will help faster absorption of heat from inside the motor and dissipate the same efficiently to atmosphere, reducing the surface temperature of motor?
Jayant JoshiEnergy Auditor & Electrical Consultant - Nagpur, India
2006
A. Referring to this query for heat paint, there is paint called climate control coatings which has property of this type of heat dissipation; at the same time it can with stand 400 °C.
Sanjay Nabiraclimate control coatings - Nagpur, India
2007
A. I'm a "Mechatronics" Engineer with 35-years experience designing electric motors. In addition, I teach for the Small Motor Manufacturers Association (SMMA) Motor and Motion College and present two separate tutorials on thermal issues in electric motors, "Continuous, Dynamic, and Intermittent Thermal Operation in Electric Motors" and "How to Improve Electric Motor Power Efficiency". In comments by Mr. Kumar, I'm very curious how he concluded - "the PAINT which we use to paint our motor body is the real culprit as it is of normal type. This normal paint is acting as a blanket over the electric motor and thus restricts the heat dissipation rate, which eventually leads to winding heat up & finally winding fails."
Having conducted numerous thermal experiments on all types of motors (AC induction, Brushless DC, Brush DC, Stepper), I must disagree with this conclusion. Instead, I 100% agree with Mr. Watts that the paint (thermally conductive or not) used on a motor's exposed surface area does not significantly impact heat transfer between the motor and the surrounding ambient environment so long as the paint color is black and the paint thickness less than 0.5 mm thick. If the motor is painted white (often used in the food industry) then a 2-4% reduction in heat transfer occurs, compared to painting same motor black, since radiation is a component of the heat transfer but not as significant as conduction and convection with typical 130-155° C motor temperatures plus the normally occurring ambient air. However, if the motor has been over-painted so many times that paint thickness becomes greater than 1 mm thick then I can understand that low thermal conductivity paint could inhibit heat transfer to the ambient.
Based on actual experiment, what does significantly impact the heat transfer from within the motor is the material used for its housing and the best material is Aluminum since it has higher thermal conductivity compared to a steel housing that's typically used for AC induction motors. Adding cooling fins to the housing plus painting it black is the best possible design. In addition, forcing high velocity cooling air across the housing's exposed surface area provides better heat transfer due to the "wind chill" affect.
Next, I have questions for Mr. Kumar since his application is the steel industry. Are you keeping the motor's case clean from dust, oil, or other foreign material? I don't care what housing material is being used or what color the housing is painted if dust or oil builds up on the case then heat transfer from motor to ambient will be reduced. Second, what is the ambient air temperature surrounding the motor's that are failing? NEMA (National Electrical Manufacturers Association) recommends that all motors specified for industrial application be rated at 40° C ambient temperature, in calm air and with NO attached heat sink. Hence, the 5 HP rating for your motors should be based on these NEMA recommended ambient conditions and you must verify this with the motor manufacturer. If the burnt up motors are rated based on different "ambient conditions" (heat sink, forced air cooling) plus if your ambient temperature is higher than the one specified by the manufacturer, then this is NOT a 5 HP motor in your application and you must use a larger motor as suggested by Mr. Watts.
Next, Mr. Joshi asks - "Can we provide some coating/paint on the surface of electric motors which will help faster absorption of heat from inside the motor"? Again the answer is NO! To improve heat transfer within a motor, one uses Aluminum housing, instead of steel, and this is what I use for all my high performance BLDC servomotor designs. Furthermore, if you want to further improve heat transfer within the motor then you pot the stator winding using a thermally conductive epoxy instead of the traditional "varnish" still used in most AC induction, stepper, and low performance BLDC motors. 15-years ago I began potting BLDC stators using a thermally conductive epoxy and this is becoming standard in high performance BLDC motors since the improvement in heat transfer is 40-50% higher compared to using a varnish! If you want to read more about potting then obtain a copy of my paper I presented at the 2006 SMMA Fall Conference in Saint Louis MO, "How to Increase a Motor's Continuous Torque Output and Power Density by Potting its Stator With Thermally Conductive Epoxy". In addition, I have published companion papers in two different motor industry trade magazines, Sept. 1, 2009 issue of "Energy Efficiency & Technology" .
and Aug 1, 2009 issue of "Motion Systems Design (MSD).
Richard Welch Jr
Consulting Engineer - Oakdale, Minnesota USA
November 28, 2010
February 3, 2012
A. In reference to thermal paint, ingredients are everything.
I am an RF engineer in the US. In my job we often have to paint the housing of electrical components to protect from weather. Often black does not meet city standards, so we often have to use green or tan that is also pretty thick, 2mm.
We use paint with a high aluminum AND silicone content for heat dissipation and resilience.
Paints that are lead plastic ferrite polyurethane or vinyl based only insulate. Water based paints usually have little or no effect on electrical components heat conduction.
Another alternative to painting could also be powder coating. However powder coating can melt if the temp gets too high (normally larger engines though you may want to use one to test and see how it works before trying all of them).
Also, in addition to paint, a conductive wire braid ran to a common ground from the most central location of the non-moving part of the engine that gets the hottest, can help greatly (central to the heat, not the physical geography, this location may change if the motor is rotated or turned).
Finally, the engine core position plays a giant role in heat dissipation. In turbine type engines that spin, place the motor so that the turbine core can spin like a top. This will allow the least thermal resistance physically as all the open spaces are facing up. In combustion type motors place the motor physically so that the combustion chambers have their heads on top so that thermal resistance is also reduced the most.
- California
A. Alok,
To answer your question there are nanostructure coatings that can remove heat up to four times faster than standard paints. Researchers at Oregon State University and the Pacific Northwest National Laboratory have discovered a way to achieve near-optimal heat dissipation by applying a nanostructured coating.
They have reported the coatings produced a "heat transfer coefficient" ten times higher than with the uncoated surfaces, dissipating heat four times faster than previously possible.
Surprisingly, the principles that brought the performance improvement are simple, and consist of covering standard heat conducting materials (such as copper and aluminum) with a thin strate of zinc oxide. The coating develops a multi-textured surface that encourages heat to be transferred via capillary forces.
Hope this helps bhaiya.
- Jay, Florida, USA
March 10, 2012
A. One other item to note is that of the winding insulation of the overheated motor. Are the windings properly coated with the correct designation of wire enamel? Different classes for different operating temperatures. Along with that also goes to the overall condition of the motor. The bearings for example. If the motor is overheating regularly you also might be burning up the bearing grease. If that start disappearing the motor will also increase in temperature due to friction issues, which transfer the heat to the rotor assembly, then to whole interior of the motor. Most likely the motor being used is a TEFC motor. And I would assume that with it being a 5 HP motor there are already fins built into the motor frame, which is most likely cast iron. From the sound of it it seems that there are multiple issues all leading the the one result. So it is hard to determine where to start. But paint, unless improperly used, will be the least possible reason. Most of fault probably lies within the application pushing the motor beyond its intended capability.
Eric Thompson- Fort Wayne, Indiana, USA
April 8, 2015
Q, A, or Comment on THIS thread -or- Start a NEW Thread