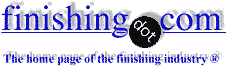
-----
Plating to make aluminum magnetic
Q. I need to obtain a magnetic coating on aluminum. That coating has to be radio-opaque.
I have heard of gold plating aluminum using a nickel substrate. That is a magnetic material.
I want to know how I can obtain a magnetic coating on aluminum (What technique I have to imply?)
Thanks,
- Bucaramanga, Santader, Colombia
2006
A. You might look into how hard disks are manufactured, Andrea, since they sound very similar to what you're looking for. They have been done at least three ways, iron oxide applied to the aluminum platter, electroplated magnetic coatings, and sputtered magnetic thin films.
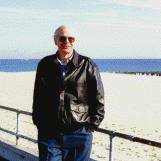
Ted Mooney, P.E.
Striving to live Aloha
finishing.com - Pine Beach, New Jersey
2006
Q. Dear Ted:
Thanks for answering.
That give me an idea but I have still some doubts.
I was trying to deposit iron oxide by colored immersion with ammonium ferrioxale, and I do it but the part didn't get a magnetic property. I don't know if there are any specific conditions to do it.
Do you know something about it?
My best regards,
- Bucaramanfa, Santander, Colombia
2006
A. Sorry, I have no knowledge of that process, Andrea, but I think you should be able to find some info on how the magnetic tape used in VCR recorders, voice recorders, and the magnetic strip on the back of credit cards is made.
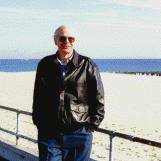
Ted Mooney, P.E.
Striving to live Aloha
finishing.com - Pine Beach, New Jersey
2006
A. Try plating the aluminium with nickel or cobalt. You will need to do a zincate pretreatment first, otherwise it won't adhere. Both nickel and cobalt are magnetic, but not as magnetic as iron. Alternatively, try vacuum deposition of iron, nickel or cobalt etc.
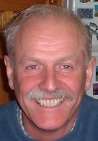
Trevor Crichton
R&D practical scientist
Chesham, Bucks, UK
2006
2006
Q. Dear Trevor:
I have been studying a lot of about this Project.
And Right know I consider that is better and easier to reach for me by plating than other techniques.
I discover that not only I have to obtain a magnetic surface but also a radio-opaque surface.
For this reason I have been considering making a plating process.
First, I am going to do a zincate pretreatment, because I know that it is necessary to obtain good adherence.
Then, I am going to plating, probably with cobalt or Neodymium, and I suppose that in this way I am going to obtain a magnetic surface.
Finally, I am going to plate with gold, and I suppose that in this way I am going to obtain a radio-opaque surface.
I would like to know if in this sequence I can obtain a magnetic and radio-opaque surface.
And I would like to know if you know more specific information about these techniques.
Thanks a lot
Sincerely,
- Bucaramanga, Santader, Colombia
A. Andrea, firstly, make sure the aluminium is suitable for electroplating - some alloys do not bond well to any electrodeposit.
Secondly, I would strongly recommend you get a proprietary zincate solution and follow the suppliers instructions on how to prepare the aluminium for the zincate treatment. Failure of the zincate process will certainly result in electroplating failure, so make sure you get this right. The pretreatment will include etching and desmutting, but be determined by the type of aluminium you are using. It will need etching and desmutting, but the process details will be determined by the alloy.
Once zincated, you can put down the nickel or cobalt. I would suggest you use nickel, because it is cheaper and much better known. There are numerous reports that say cobalt plating is the same as nickel plating and I would strongly disagree with this; cobalt plating is much more complex and difficult to achieve. If you do use nickel, you can either use a high sulphate nickel, a Watts nickel or a sulphamate nickel. The best two options are Watts and sulphamate, but if you use Watts, substitute the nickel chloride with nickel bromide. This is because aluminium is very susceptible to chloride attack and bromide is much more benign, but still does the job in helping anodic polarisation. If you use sulphamate, you don't need chloride in the solution, as you should use sulfur depolarised nickel anodes.
Once nickel plated, the aluminium artifact will be magnetic. Since you want to plate the nickel with gold, make sure there are no organic brighteners and levelers in the nickel solution, as this can cause adhesion problems for the gold. If you must use additives, you will need to give the nickel a very short etch before gold plating, otherwise the gold may suffer from poor adhesion. I have no experience of neodymium plating so cannot comment on it.
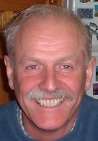
Trevor Crichton
R&D practical scientist
Chesham, Bucks, UK
2006
2006
Dear Trevor:
Q. I really appreciate your answer. It has been very useful to develop my Project. Let me tell you, I finally decided plating aluminum in the next sequence:
1- Pre treatment (Etching, Desmutting)
2- Pre zincated
3- Nickel plating
4- Gold plating.
The alloy that I have used is AlMgSi 6063:
Al The rest
Mg 0.45 - 0.90
Si 0.20-0.60
The zincate solution that I have used is known as Watts.
Right know I have a big trouble and this is that when I am making nickel plating process the work piece takes a black color.
I would like to know if there is any treatment to apply to the nickel anode.
Moreover, I would like to know your opinion about this problem.
I am going to attend to your soon answer.
Sincerely.
- Bucaramanga, Santander, Colombia
Q, A, or Comment on THIS thread -or- Start a NEW Thread