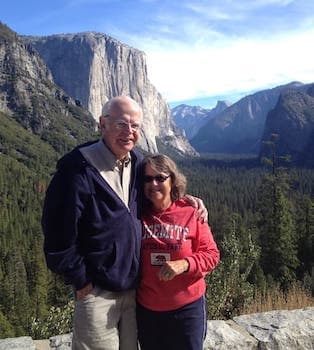
Curated with aloha by
Ted Mooney, P.E. RET
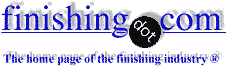
The authoritative public forum
for Metal Finishing 1989-2025
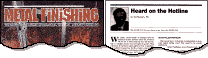
-----
De-magnetizing prior to plating steel
2006
I am the supplier Quality Manager of a OEM. We have been experiencing problems of late with magnetized parts being plated. The parts attract every bit of contamination that is in the plating tank causing an extremely rough and unsatisfactory finish.
Is it standard procedure for platers to demagnetize steel parts prior to plating?
Does it differ with each plating process (ie: Nickel Chrome, Zinc, E-nickel, hard chrome)?
Thanks,
OEM MFG - Mpls, Minnesota
It is common procedure for us to check for magnetism and then demagnetize if necessary on steel and 400-series stainless steel for any plating line.
I might expect adhesion issues with plating magnetized parts.
- Oklahoma City, Oklahoma
2006
You want to use a degaussing coil to randomize the magnetic field in your workpieces. A Gauss meter will come in handy to determine when/whether you need to degauss and how effective your degaussing operation has been. I might suggest contacting some (aerospace) plating shops to see just what equipment they use.
Will make no product recommendation here, but a quick Google search shows Vallon is one brand.....most search results have to do with wiping clean PC hard drives; you'll need to dig a bit deeper to get what you need.
Good luck.
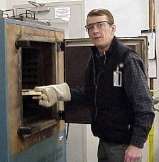
Thomas Hanlon, Materials Engineer
aerospace finishing - East Hartford, Connecticut, USA
2006
March 2, 2010
dear sir,
We have a problem in welding st 52-3 grade material. When welding shell joint (valve body shell, thickness 16 mm) proper fusion was not taking place. Welding joint, as well as place near to it are completely magnetized; as a result of this fusion is not taking place. We tried to demagnetize it by following methods :
1. preheated to approx. 250 °C.
2. with a heavy tack weld on one side & earth clamp away from welding - we did welding towards heavy tack weld
3. increased voltage
But with all this above method we failed to weld the part.
Can you please suggest us how to demagnetize it ( size: inner dia 1100 mm)
ENGINEER - INDIA, PALWAL
Q, A, or Comment on THIS thread -or- Start a NEW Thread