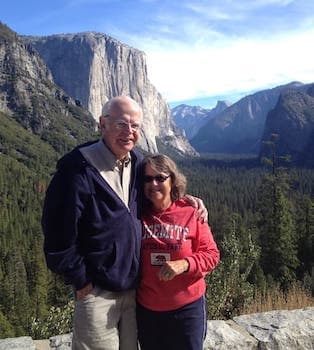
Curated with aloha by
Ted Mooney, P.E. RET
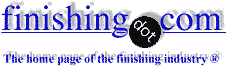
The authoritative public forum
for Metal Finishing 1989-2025
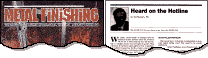
-----
Comparison between hot dip galvanizing and zinc metal spraying
Q. Sir,
I am working in a metallizing works as a marketing executive. We are in field of sandblasting, spray galvanizing and aluminizing.
I wants detailed comparison between hot dip galvanizing and spray galvanizing.
I hope I will get best answer from your site.
metallizing works - Bangalore, Karnataka, India
2006
A. Firstly there is no such thing as "spray galvanizing".
There is zinc metal spraying, where a stream of molten zinc is blown onto the surface or a substrate.
There is galvanizing, where steel (or iron) articles are immersed in molten zinc.
In the first case, the adhesion is mechanical, and depends greatly on the roughness of the steel. The adhesion fails often. The system has the advantage that it can be applied on a site, not in a factory.
Metal spraying is usually porous, and the underneath metal (substrate) can be exposed through the holes. It usually needs sealing with an organic coating. There is no practical limit to the size of item to be coated. A bridge could be done in situ.
In Galvanizing the adhesion is by alloying the zinc to the steel. The system has the disadvantage that it is a factory only process, but it lasts longer, adheres better, and is smoother. It is not porous, and needs no sealing coat.
Generally, per area unit, this is a lower cost process, but only limited size items can be coated. Biggest items perhaps 28 meters long x 1.5 m x 3 m, but more typically 15 x 1.5 x 3 m.
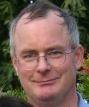
Geoff Crowley
Crithwood Ltd.
Westfield, Scotland, UK
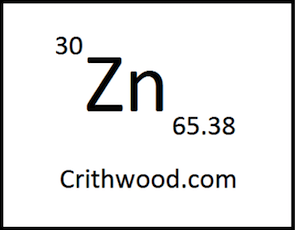
2006
by NACE
[only rarely available]
on AbeBooks
or eBay or
Amazon
(affil links)
Q. Hello,
Is there a definite visual difference between HDG and zinc metal spray finish? Does all HDG result in the 'spangle' finish, or are more uniform finishes achievable?
Our competitors claim to HDG their product, but I am not convinced.
- Surrey, United Kingdom
April 17, 2010
A. Hi, Paul. What process do you do, zinc metal spray? What appearance do you get?
I don't think all hot dipped surfaces get a spangle finish. If you don't know what your competitor does, it may be flame spray, or mechanical galvanizing, or sherardizing, or electroplating with zinc -- but it's hard to know the process from the appearance. Whether he is entitled to call his process "HDG" is sort of a moot question because people will always use terms to their advantage, and if you forbid him from using that term, then he'll just call it "galvanized", as when people invented the term "electro-galvanized", perhaps so they could substitute cheaper zinc electroplating for more expensive hot dipped galvanizing :-)
Can you demonstrate that your product is superior to your competitor's, in some way, or can they demonstrate that theirs is superior to yours? I think that's the important point. Good luck with it.
Regards,
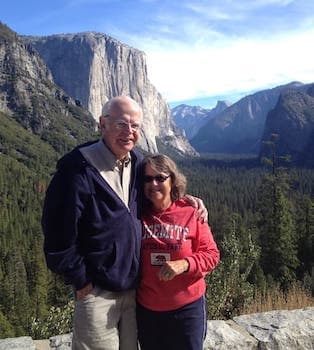
Ted Mooney, P.E. RET
Striving to live Aloha
finishing.com - Pine Beach, New Jersey
April 18, 2010
Q. Sir, I wanted to know if hot zinc spray is a cheaper process as compared to hot dip process, and does it give same result as hot dip?
Sachin Uttekar- Thane, Maharastra, India
July 17, 2013
A. Hi Sachin. I'm sure you already know that any time you see the widespread application of competing technologies, both are good & viable, and neither is objectively "better", because an inferior process would have quickly died out. Which process you should select will depend upon an evaluation of some specific individual elements of your parts and their application.
Despite us all realizing that, you'll still find many articles out there that try to present the issue in those terms. One such article claims that hot zinc spray performed better in corrosion testing; but as implied by Geoff's reply, a tester with an axe to grind may have been ultra careful, taking forever and a day to get a thick even coating with minimal porosity, which may not be at all representative of what production sprayers actually do :-)
So it would be best if you could find a shop which offers both services because their recommendation after looking at your parts is likely to be fairly objective.
In addition to everything else you read, and Geoff's informative comments, I would suggest that if you are going to paint the parts, that's one more element that suggests hot zinc spray; whereas if the zinc is the final layer, that's an element that leans towards hot dip galvanizing. Good luck!
Regards,
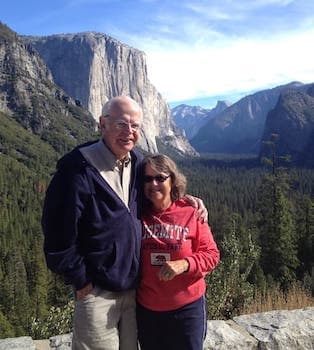
Ted Mooney, P.E. RET
Striving to live Aloha
finishing.com - Pine Beach, New Jersey
July 17, 2013
Q. What is purpose of HDG and zinc spray?
Mohammed shajid- Dammam saudi Arabia
October 2, 2015
A. Hi Mohammed. The principal use is to sacrificially protect steel from corrosion. Zinc is anodic to steel and will galvanically protect it; plus in normal atmospheric conditions the zinc forms stable glassy corrosion products (complex carbonates and oxides) that tend to seal the zinc away from the environment and greatly slow its corrosion.
Regards,
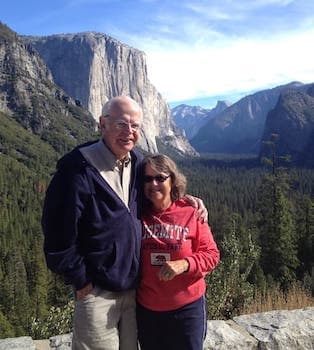
Ted Mooney, P.E. RET
Striving to live Aloha
finishing.com - Pine Beach, New Jersey
October 2015
ACRONYMS:
"C5M" = Very high corrosion risk, coastal and offshore areas with high salinity per ISO 9223
Q. Hi, we are transformer manufacturers. We'd like to go for Hot zinc spray setup in our factory. Suitable for C5M environment.
When I refer to suppliers, there are various methods, like Arc Spray, Flame spray, Plasma spray, etc.
Which one we have to prefer?
What are the main features to be checked?
Surface finish should be smooth.
Your reply will be highly appreciated.
- KUWAIT
November 2, 2015

Q, A, or Comment on THIS thread -or- Start a NEW Thread