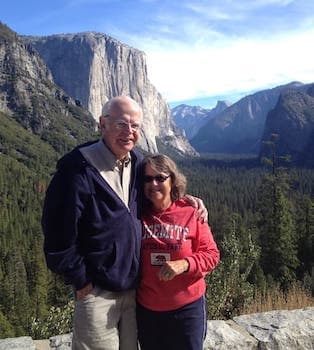
Curated with aloha by
Ted Mooney, P.E. RET
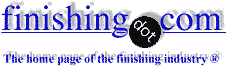
The authoritative public forum
for Metal Finishing 1989-2025
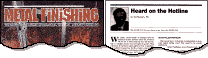
-----
How to electroless-polish / electropolish 316 Stainless Steel tube ID?

Q. Hello. We are facing problem of white patches inside 1" Dia tubes 3 mtr long which are being Electropolished by us. We immerse the tubes vertically in the bath.What are the cause? What are the remedies for removing the patches? Please suggest or guide us. Thanks, Mahesh.
Mahesh Raja- Mumbai, Maharashtra, India
2000
A. Electropolishing requires high current density and fresh solution. It may be possible to electropolish this item with auxiliary cathodes and good solution changeover. But if you are just putting them into an electropolishing tank like any other work and are expecting the insides to polish up, then I think your expectations are probably unrealistic. Good luck.
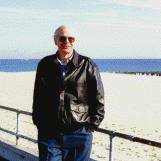
Ted Mooney, P.E.
Striving to live Aloha
finishing.com - Pine Beach, New Jersey
2000
A. The white patches appearing on the ID of your tubes could be a residue from your electrolyte. Insure that when you remove the tubes after processing from your tank, that the current is OFF and check your washing procedures giving particular attention to the internal surfaces.
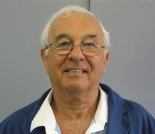
Joel Levinsohn
- Sydney, Australia
2000
Electro polishing of inside of SS pipe
Q. Dear sir, I want to electropolish SS 316 pipe of 30 to 40 mm ID from inside having length of 300 mm and 600 mm.
Please advise process, equipment needed, and chemicals and its suppliers.
Your early response will be highly appreciated.
systems and engg. - Ahmedabad, India
2005
adv.
We have developed way of polishing such tubes without etching the corners, due to saline-based electrolyte, the temperature of polishing around 50 °C.
Contact us if interested.
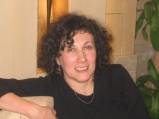
Anna Berkovich
Russamer Lab

Pittsburgh, Pennsylvania
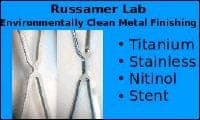
2005
2006
Q. Howdy Folks,
Been browsing here and haven't yet found the answer I seek. I would like to know if there is a relatively simple process to polish the ID of type 316 stainless steel tubing, preferably electrolessly.
I have a 1.5" long section of tubing, McMaster-Carr #51755K35 to be exact, which I am trying to use as a millimeter-wave waveguide. The problem is it is very lossy and I attribute this partly to the 0.001" high "bumps" I see on the inside of the tubing and the very rough surface. I would like to know if there is a chemical polish which will at least smooth the surface somewhat, if not remove some of the higher bumps. Some details:
* the tube is no longer round, or I might have been able to run a wire through it and polish
* it's too long to drill or ream (we've tried)
* we do have a means of pumping a solution through it, though flow is low
I am hopeful there is a technique out there. I've seen the insides of some syringe needles are very nicely polished and they look to have been chemically polished, so I am hoping I can use a similar technique.
If I can't polish, are there any recommended ELECTROLESS techniques to plate gold or copper onto 316 stainless?
Thanks in advance for your time in replying. For reference, NRAO does have a reasonably well equipped plating/chem lab so I am willing to try a variety of credible suggestions. It's the time and resources for the initial research we can't spare, so I am hoping someone can point me in the right direction and provide some advice.
Thanks much,
Natl. Radio Astronomy Observatory - Charlottesville, VA, U.S.A.
A. Your tubing has 0.0030±.002" ID. If too deformed to permit passage of a fine cord or wire, then polish the ID of some new tubing.
First use Miniature Round Sanding Cord, coated with 200 grit silicon carbide, available in 0.018" and 0.025" diameters. Apply
Simichrome
⇦ this on
eBay or
Amazon [affil links]
, a slightly abrasive polish, to the cord for a smoother finish. Pull back & forth through the tubing, and rotate the tubing on a taut cord, too.
Degrease (SimiChrome leaves a protective film).
Electropolish the tubing ID. As cathode, use a Continuous-Flex Miniature Single-Conductor Copper Wire, AWG 36 (OD 0.016"), with PVC insulation good to +176° F. Remove a ring about 1 mm long of the PVC insulation to expose some cathode area. Slowly pull the cathode through the electrolyte-filled tubing for polishing -- maybe submerge the tubing vertically & pull the cathode wire slowly upward to allow bubbles to escape upwards.
- Goleta, California

Rest in peace, Ken. Thank you for your hard work which the finishing world, and we at finishing.com, continue to benefit from.
2006
A. You have a 1.5" piece of tubing? For goodness sake, buy a new piece of tubing with the proper interior finish.
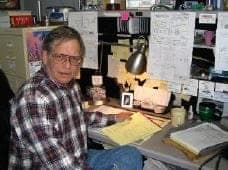
Jeffrey Holmes, CEF
Spartanburg, South Carolina
2006
Electropolish vs Passivate
I need some answers, I have a tube 316 s/s OD 1.05 and ID .625 which ID is honed to a 64 finish after we finish machining and welding 2 nozzles on the outside. Our customer has us electropolish the outside and inside of the tube to remove any contamination from the metal. The question is if we passivate it which is easier and faster does it not do the same or better to remove contamination from the surface? We would still have to electropolish outside for cosmetics but I am hearing that electropolish is better from several sources and passivate is better from others.
Al MannhalterMachine Shop - Vancouver, WA USA
2007
A. Hi, Al. Neither electropolishing nor passivation are really intended to remove contaminants except for steel particles that can lead to rust. Both processes prevent rusting (about equally well).
But electropolishing smoothes the surface, removing "tooth", and making it more difficult for contamination from service conditions to stick to the surface. Thus electropolishing is often specified for components that will be used in food service and pharmaceutical service, and I suspect that your customer specifies electropolishing of the inside of the tubing for this reason. If this didn't answer your question, please follow up. Good luck.
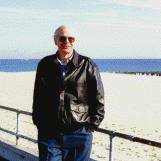
Ted Mooney, P.E.
Striving to live Aloha
finishing.com - Pine Beach, New Jersey
2007
A. They are two different processes that contribute to corrosion resistance via different methods. As Ted said, electropolishing smooths the surface, making the corrosion reaction less able to occur. Passivation removes the free iron from the surface, making it unavailable for forming rust. The ultimate possible in corrosion protection is electropolishing followed by citric acid passivation, thus combining both effects.
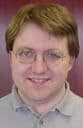
Ray Kremer
Stellar Solutions, Inc.

McHenry, Illinois
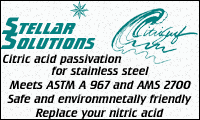
2007
Q, A, or Comment on THIS thread -or- Start a NEW Thread