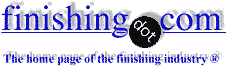
-----
Hot dipped galvanized vs. electroplated galvanized
We are fabricating and installing gutters that need to be made of a paint grip type galvanized metal. This galvanized metal can be hot dipped or electroplated and phosphatized. What are the characteristics of the two types of treatments and which will hold up to the elements the best without rusting until paint is applied?
Karen BusynConstruction - Houston, Texas
2006
2006
The corrosion protection of these three process is Galvanising best, electroplating second, and phosphate last.
The first two are dependent on the thickness of the coating, and typically material about 6mm thick will be coated about 90 microns in Galvanizing, about 8 microns in Zinc plating, and 3-9 microns in phosphate.
But there are other plating technologies than zinc plating, for example zinc-nickel, which has about 10 times the corrosion protection of 100% Zn plating, for the same thickness, but its expensive, about double the cost of galvanizing.
Getting paint to adhere to these three is quite different. Galv is difficult unless a competent pretreatment is used, such as chromate or phosphate on top.
Plating is similar. Phosphate is a good painting surface, but not much good for corrosion protection on its own.
You didn't state the duty of the material? Indoors, outdoors? Marine or country environment? These factors have a large bearing on whats appropriate. Galv for indoor use is in some cases using a sledgehammer to crack a nut. Phosphate or Zn plate for marine use is a waste of time.
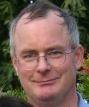
Geoff Crowley
Crithwood Ltd.
Westfield, Scotland, UK
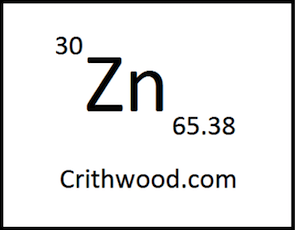
Q, A, or Comment on THIS thread -or- Start a NEW Thread