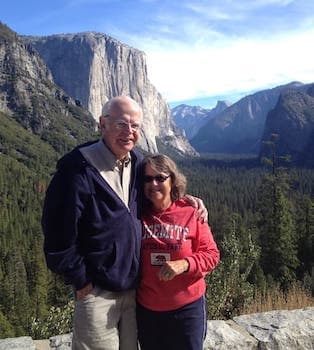
Curated with aloha by
Ted Mooney, P.E. RET
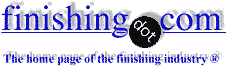
The authoritative public forum
for Metal Finishing 1989-2025
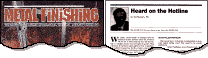
-----
Black parts after zinc plating process
Why would I have black parts after the zinc plating process? They are supposed to be a clear finish on a silver based part. After coming out of zinc plating they are black, after the plating process they go into an over^oven and turn brown. We have stripped them and replated with the same results.
fasteners - Columbus, Indiana, USA
2006
First of two simultaneous responses --
More information is needed on the problem and process. Are the parts really silver or a silver alloy or silver plated. Does the black look uniform or are you talking about spots. Does the black appear immediately after plating or after chromating?
Gene Packmanprocess supplier - Great Neck, New York
2006
Second of two simultaneous responses --
Did you mean 'oven' or 'over'. Please rephrase your question, what is the spec, process, and what is a more accurate description of the problem?
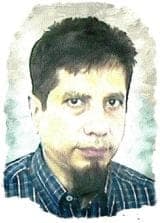
Khozem Vahaanwala
Saify Ind

Bengaluru, Karnataka, India
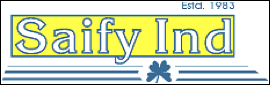
2006
First of three simultaneous responses --
Hello
One question this is barrel or hang [rack] system.
- Cieszyn, Poland
2006
Second of three simultaneous responses --
The parts are silver alloy. The black is uniform and it appears immediately after the plating process and after going thru an oven they turn brown.
Terry McClintic- Columbus, Indiana, USA
2006
Third of three simultaneous responses -- 2006
TERRY !
PARTS CAME OUT BLACK AFTER ZINC PLATE ,DO YOU HAVE NITRIC ACID DIP AFTER ZINC? CHECK THE ZINC METAL IN YOUR ZINC TANK MAY BE VERY LOW.
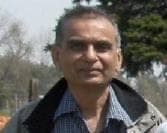
Popatbhai B. Patel
electroplating consultant - Roseville, Michigan
2006
Yes we do have the acid dip after zinc plating. I will check the zinc level in the tanks but it should be ok.
I appreciate all advise I can get. Thank you everyone
We have a barrel system
- Indiana, USA
First of two simultaneous responses --
I think that you do not have a thick enough zinc deposit to prevent a reaction between your chromate and the underlying silver. If you are not controlling your thickness via a thickness testing instrument, try doubling your plating time and see if you reduce or eliminate the problem. If so you are either not getting enough thickness (causes could be low metal, anode area, low current, additives, poor agitation, etc)or have a porous deposit (check plating additives). BTW what does your zinc brightener and/or chromate supplier have to say?
Gene Packmanprocess supplier - Great Neck, New York
2006
As an addendum to my previous reply, you should check that your danglers are in good condition (no external or internal breaks) and that the contacts are resting correctly in clean saddles. Also check that the barrel holes are not clogged. BTW what color are the danglers in the barrel (the contact area at the end of the insulation) after you have processed the parts that turn black? If they are not black this would pretty much prove my previous hypothesis.
Gene Packmanprocess supplier - Great Neck, New York
2006
Second of two simultaneous responses --
Hello Terry;
Your plating bath has got contaminated with metallic impurities that have most probably come out of your silver alloy parts. Try purifying the bath; if it doesn't work you will have to discard the bath.
In future you will have to ensure that you have a live entry for your barrel, ie: the danglers have to be connected to the cathode before the barrel enters the plating solution and preferably at a much higher current than the normal current to ensure your parts do not dissolve into the solution before plating starts.
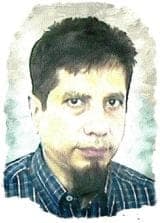
Khozem Vahaanwala
Saify Ind

Bengaluru, Karnataka, India
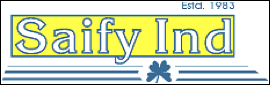
2006
2007
Dear sir,
first you check your pretreatment process,after this you check your bath composition(maintain it) dummy the solution,carbon treatment, with low conc. on brightener & additive with live current put barrer into the tank or keep first tank as strike tank with 10 minutes plating than go to main tank. I give you sequence of plating process
hot soak
anodic
HCL
anodic
H2So4
strike zn
main Zn
0.5% HNO3
passivation trivalent chrome if you go for heating than only
every step require rinse with water in between
- Mumbai, Maharashtra, India
Q, A, or Comment on THIS thread -or- Start a NEW Thread